Pretreatment Systems
The Most Efficient Painting Solution.
E-coating line pre-treatment systems are advanced pieces of equipment used to prepare and treat product surfaces in industrial manufacturing. They play a vital role in the electrophoretic coating process, providing high-quality coating adhesion and durability.
Our pre-treatment solutions include spray pre-treatment and dip tank pre-treatment. Spray pre-treatment uses a high-pressure spray system to evenly spray chemical solutions on the surface of the workpiece to remove oil, rust, and other impurities, ensuring that the surface of the workpiece is clean and suitable for subsequent painting. Dip tank pre-treatment immerses the workpiece in a tank containing chemical solvents for thorough cleaning and rust removal and is suitable for workpieces that require deep cleaning.
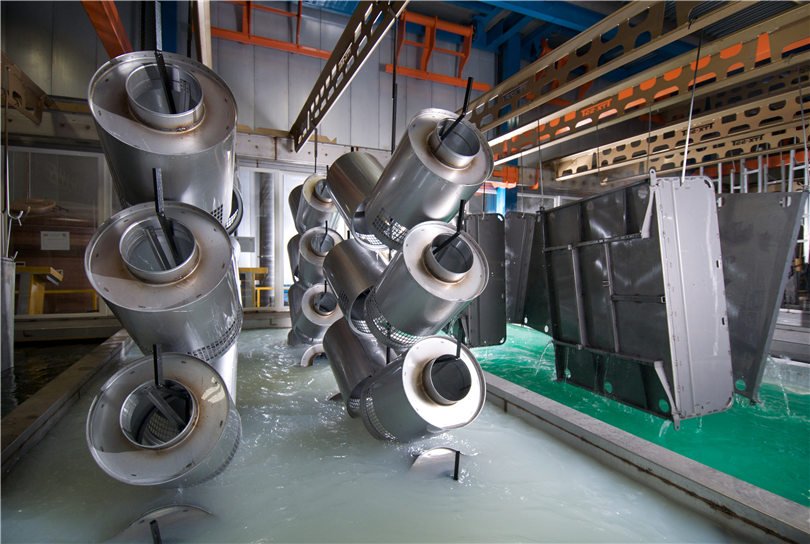

Proven
30 years of experience providing proven equipment
Lifetime Service
Maintenance is more important than repair
Maximum Efficiency
Production line capacity fully matches demand without wasting any resources
Product Description
Spray cleaning systems: Pre-treatment systems for e-coating lines are usually equipped with highly efficient spray cleaning systems that completely remove grease, dirt, and impurities from the product surface. This cleaning system uses high-pressure nozzles and special cleaning agents to ensure that the product surface is clean and dust-free, providing good adhesion to the coating.
Pre-treatment immersion tanks: Pre-treatment immersion tanks are one of the core components of the pre-treatment system for e-coating lines. They usually include alkaline cleaning tanks, pickling tanks, and phosphating tanks. These tanks remove oxides and corrosive layers from the product surface through chemical reactions and provide the ideal basis for the subsequent coating process.
Environmental performance: Modern pretreatment systems fore-coating lines are increasingly focused on environmental performance. They use highly efficient wastewater treatment systems that can treat and recycle the wastewater, reducing environmental pollution. In addition, the cleaning agents and chemicals used in the system are also becoming more environmentally friendly, reducing the emission of harmful substances.
Automated control systems: Pre-treatment systems for e-coating lines are often equipped with advanced automated control systems that enable precise control and monitoring of the coating process. These systems can regulate parameters such as coating time, temperature, and spray pressure to ensure a uniform and consistent coating for each product, improving production efficiency and product quality.
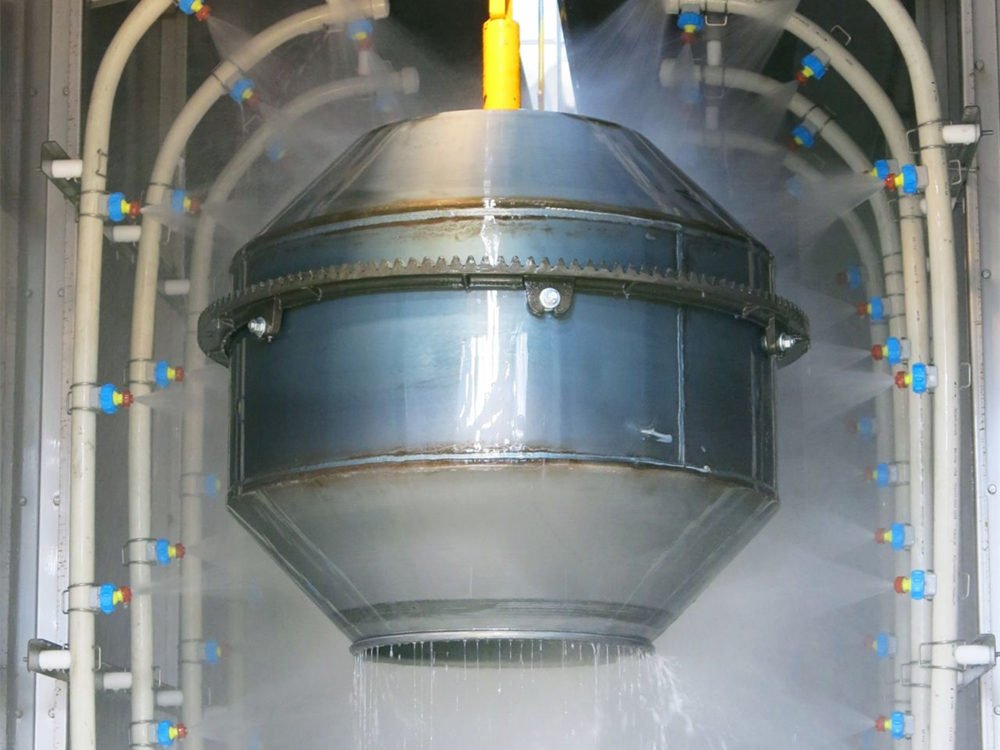
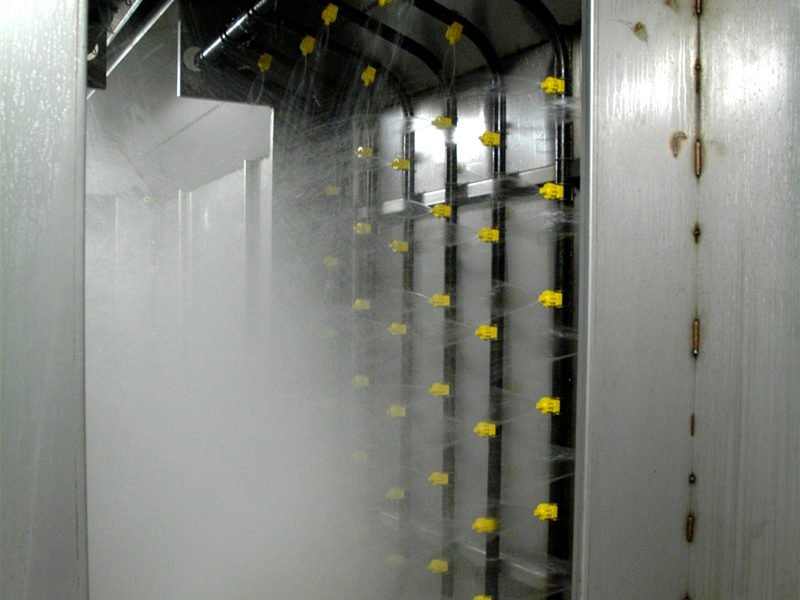
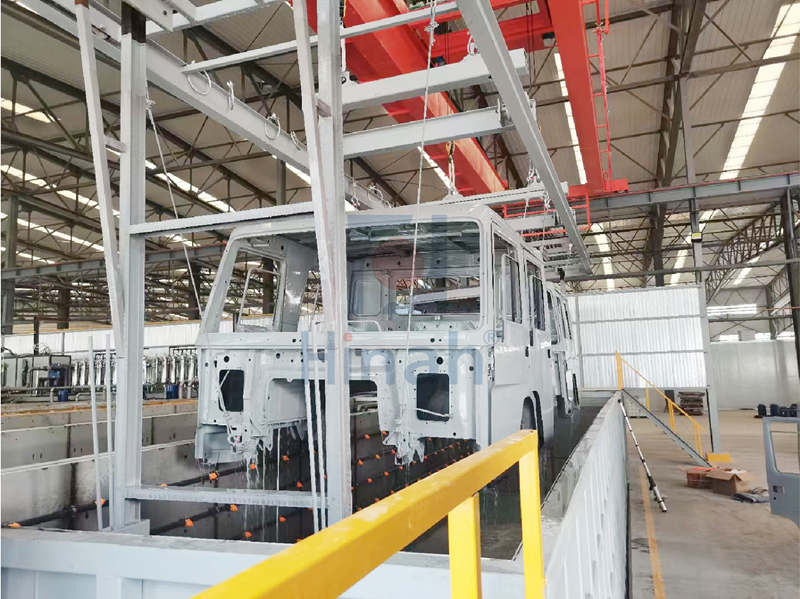
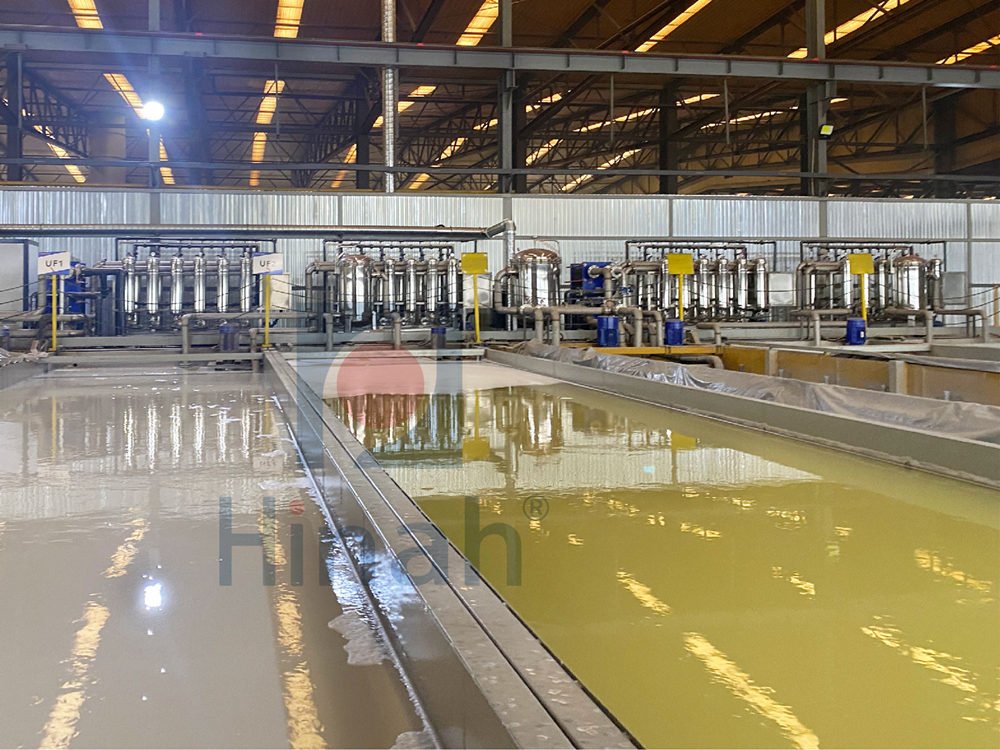
Versatility and customisability: Pre-treatment systems for electrophoretic coating lines offer a wide range of functions and flexibility. They can be adapted to different types and sizes of products and are capable of handling a wide range of materials such as metals, plastics, and composites. In addition, these systems can be custom-designed to meet the specific needs of the customer to meet their unique production requirements.
Energy-saving performance: The electrophoresis coating line pre-treatment systems use advanced energy-saving technologies such as heat recovery units and optimized spray technology: The electrophoresis coating line pre-treatment systems use advanced spray technology such as high-pressure cyclone spraying and atomized spraying to ensure uniform coating coverage and achieve the desired thickness. This optimized spraying technology minimizes paint waste and improves coating efficiency and quality.
Durability and reliability: The electrophoretic coating line pre-treatment system is manufactured from corrosion and wear-resistant materials such as stainless steel and acid and alkali-resistant materials to ensure long-term stable operation of the system. System components are precision designed and manufactured to high quality to withstand long periods of intense working conditions, reducing the risk of maintenance and failure and increasing the reliability of production.
Quick changeover and flexibility: Pre-treatment systems for electrophoretic coating lines offer the advantage of quick changeover and flexibility. They can be quickly adapted to the treatment needs of different products and batches, reducing production changeover times and allowing flexible adjustment of process parameters to meet different coating requirements. This flexibility increases production sensitivity and responsiveness to market changes and rapid changes in customer requirements.
Benefits and cost-effectiveness: Pre-treatment systems for electrodeposition coating lines offer significant benefits and cost-effectiveness. By increasing productivity, reducing scrap and paint loss, and reducing labor and energy consumption, the system can help companies reduce production costs and increase productivity and profitability. In addition, high-quality coating adhesion and durability can reduce product rework and after-sales costs.
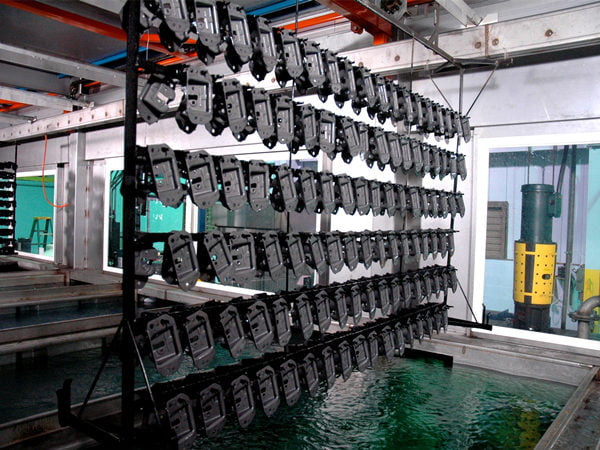
Uniform plating, no dead angle
The workpiece is covered 360° in all directions by liquid coating, and the coating is uniform, which solves the dead angle of coating.
High production efficiency, high degree of automation.

High efficiency, high utilization
The ultra-high electrophoretic paint utilization rate can reach 95%, energy saving, and environmental protection.
Widest range of application, high efficiency, good controllability
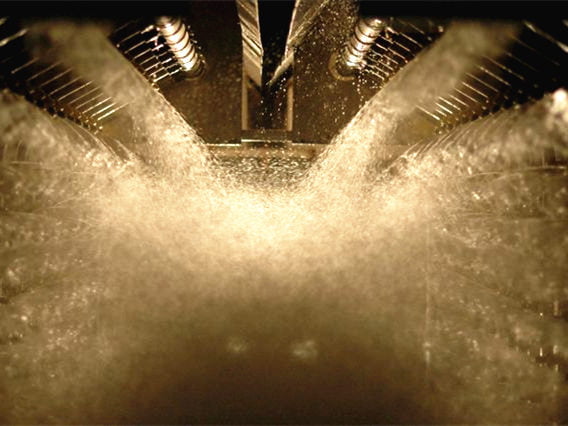
Suitable for complex shapes
It can achieve simultaneous coating of all surfaces of complex shapes, with uniform, flat and strong coverage.
Suitable for large and super-large structural parts
Spray pretreatment and immersion tank pretreatment are two common pretreatment methods for electrodeposition coating lines, each with different characteristics and advantages. They are described in detail below:
Spray pretreatment:
Features:
- Spray pretreatment is a method of cleaning and treating the product surface by spraying cleaning agents and chemicals in the form of a spray through a spray nozzle.
- It usually uses a high-pressure water stream and the mechanical movement of the nozzle to achieve the spraying action.
Advantages:
- Uniformity: Spray pre-treatment sprays the cleaning agent and treatment solution uniformly over the entire product surface, ensuring that every area is adequately cleaned and treated.
- Efficient: spray pre-treatment enables the cleaning and treatment process to be completed in a short time, making it suitable for high throughput production environments and increasing production efficiency.
- Flexibility: Spray pre-treatment can be adapted to different product shapes and sizes for a wide range of product types and sizes.
- Resource-saving: Compared to immersion tank pre-treatment, spray pre-treatment typically requires less cleaning agent and treatment fluid, thus reducing resource consumption.
Dip tank pre-treatment:
Features:
- Immersion tank pretreatment is a method of cleaning and treating products by complete or partial immersion in a pretreatment tank.
- Pretreatment tanks usually include alkaline cleaning tanks, pickling tanks phosphating tanks, etc. The product is left in the tank for a period to react and clean with the treatment solution.
Advantages:
- Thoroughness: The immersion tank-type pretreatment enables the product to be completely immersed in the treatment solution, ensuring that the treatment solution fully contacts every corner of the product surface and completely removes dirt and oxides.
- Stable treatment: Due to the long residence time of the product in the treatment solution, the immersion tank pretreatment allows for better control of the temperature, concentration, and reaction time of the treatment solution to achieve a stable treatment effect.
- Wide applicability: Immersion tank pretreatment is suitable for all types of products, especially for products with complex shapes and many holes, and can treat surface and internal dirt.
- Easy to operate: Immersion tank pre-treatment is relatively simple and easy to operate, simply place the product in the pre-treatment tank and wait for a certain amount of time to complete the treatment.
- Flexibility: Immersion tank pre-treatment is suitable for products of different shapes, sizes, and materials, offering a high degree of adaptability and flexibility. The composition of the treatment solution and the treatment time can be adjusted according to the requirements and treatment objectives of the different products to obtain the best possible pre-treatment results.
- Suitable for high-volume production: Immersion tank pretreatment is often suitable for large-scale production environments, allowing large numbers of similar products to be treated and increasing production efficiency.
- Long soak time results: Due to the long time the product spends in the treatment tank, soak tank pretreatment provides a more thorough removal of dirt and oxides from the product surface, providing better coating adhesion and durability.
- Configuration of multiple treatment tanks: Immersion tank pretreatment systems can be configured with as many treatment tanks as required, such as alkaline wash tanks, pickling tanks, phosphating tanks, etc., to enable multiple treatment steps to be carried out in succession. This can further improve the treatment effect and coating quality.
- It should be noted that spray and immersion tank pre-treatment each have their own advantages and the choice should be based on a combination of factors such as product characteristics, production requirements and budget. In some cases it is possible to use a combination of both methods, for example a spray pre-treatment for initial cleaning followed by an immersion tank pre-treatment for a more in-depth treatment.
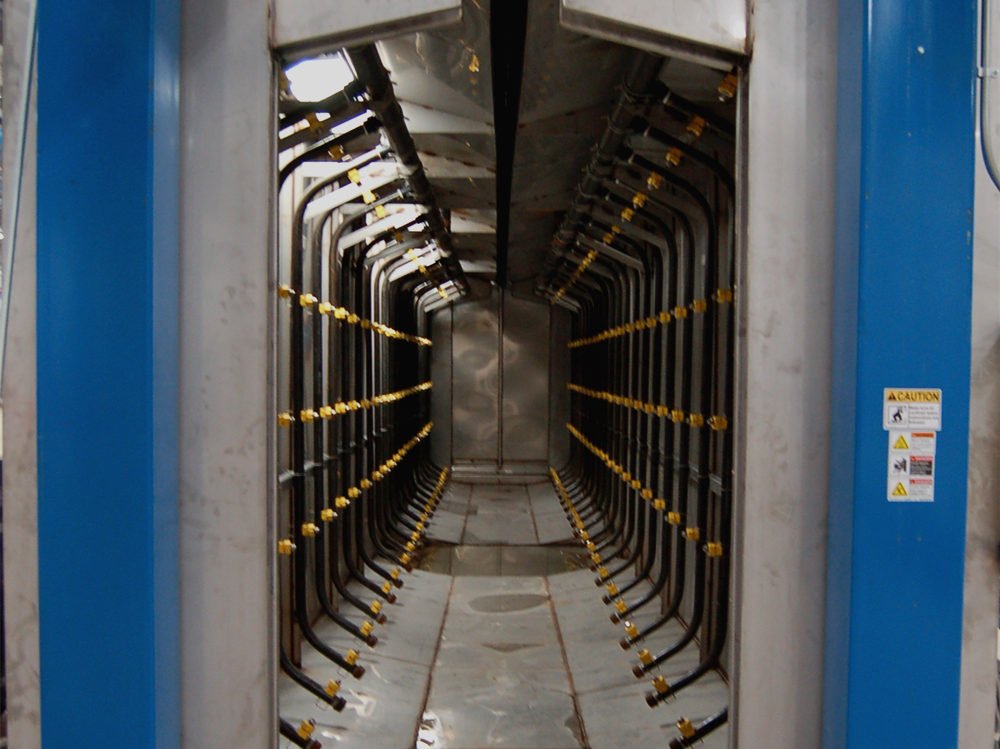
Spray Pretreatment
Spray pre-treatment can be adapted to different product shapes and sizes for a wide range of product types and sizes.
High production efficiency, high degree of automation.
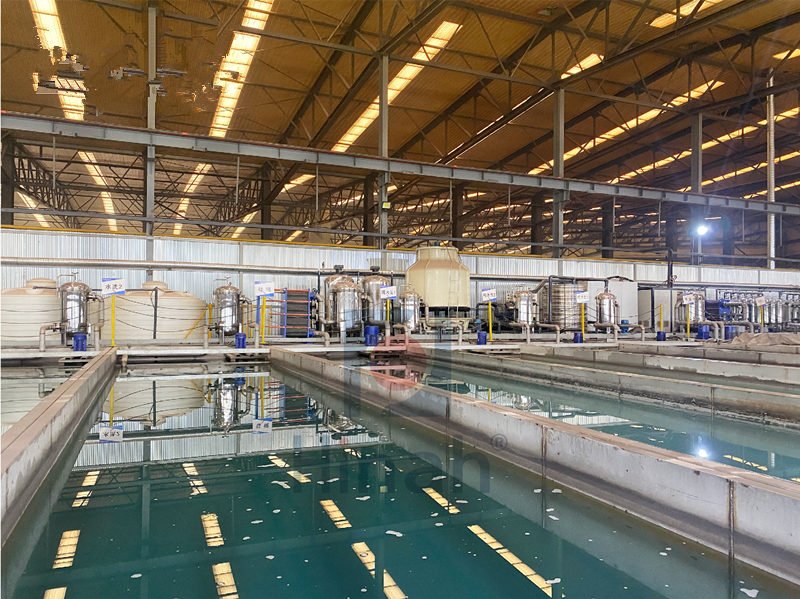
Dip Tank Pre-treatment
Suitable for all types of products, especially for products with complex shapes and many holes, and can treat surface and internal dirt.
Widest range of application, high efficiency, good controllability
Product Images
Product Feature
- Superior coating quality: Our systems use advanced processes and technologies to effectively remove dirt, grease and oxides, providing uniform and durable coating adhesion.
- Efficient throughput: through optimised process flows and automated controls, we achieve high operating speeds and continuous production, providing our customers with efficient and reliable pretreatment solutions.
- Reliable process control: Our systems are equipped with advanced automated control systems and instrumentation that allow precise monitoring and regulation of parameters such as temperature, concentration and pH of the treatment solution, ensuring that each treatment step is executed accurately.
- Resource efficient and environmentally friendly: we minimise wastage of cleaning agents and treatment liquids through effective detergent recycling and recovery systems.
- Customised solutions: Our dedicated team works closely with our customers to gain an in-depth understanding of their needs and provide the best customised solutions to meet their specific requirements and expectations.
Need a design plan, now?
Application Case
FAQ
Answer: We understand your concern about the quality of the coating. To ensure consistent coating quality, we use advanced process controls and equipment to ensure that parameters such as temperature, concentration and pH of the treatment solution are precisely controlled. We also carry out stringent quality monitoring and testing to ensure that each product meets high quality standards. In addition, our engineering team will work with you to optimise the pre-treatment solution to your product characteristics and requirements in order to provide consistent and reliable coating results.
Answer: We take environmental protection and sustainable development very seriously. Our pre-treatment systems are designed with wastewater treatment in mind. We use advanced wastewater treatment technology to effectively remove pollutants from our wastewater through processes such as sedimentation, filtration and neutralisation, and ensure that the discharge meets environmental standards. We also actively promote the recycling of wastewater to minimise the impact on the environment. We continue to continuously improve our wastewater treatment technology to meet the needs of our customers and the environment.
Answer: Absolutely! Our pre-treatment systems are designed to be highly efficient and productive solutions. With automated control and intelligent operation, our systems enable fast processing and continuous production, increasing production efficiency and capacity. We also offer customised solutions, adapting the system configuration and parameters to your production needs and product characteristics to best meet your requirements.
Answer: We deeply understand your needs. Our pre-processing systems can be customised and integrated to suit the requirements of your existing production line. Our team of engineers will work with you to carry out site surveys and technical assessments to ensure that our systems fit seamlessly into your production line. We will provide the necessary technical support.
Answer: We attach great importance to emergency response and rapid repair services. We are equipped with a professional technical support team that can respond and solve system failures quickly. We offer a 24-hour technical support hotline and you can contact our technicians for assistance at any time. In addition, we offer our customers regular maintenance and servicing services to prevent breakdowns and extend the life of the equipment.
Answer: Our pre-treatment systems are carefully designed and manufactured using wear and corrosion resistant materials and high quality components to ensure the durability and stability of the system. In addition, we offer regular maintenance and servicing, including cleaning, lubrication and replacement of worn parts, to ensure proper operation and a long service life of the system. We also provide a supply of spare parts so that parts that need replacing can be replaced in a timely manner.
Answer: Yes, our pre-treatment systems focus on energy saving and efficient performance. We use advanced process control and automation technology to minimise energy consumption and optimise system operating efficiency. We also use intelligent monitoring and regulation devices to monitor and adjust the parameters of the treatment fluid in real time to ensure efficient use of energy. In addition, we offer consultancy and advice on energy management to help our customers further optimise energy consumption and operating costs.
Answer: Of course! Our company offers customised solutions for pre-treatment systems. Our team of engineers will work with you to gain an in-depth understanding of your needs and requirements and develop an individual solution based on your product characteristics, production processes and objectives. Our goal is to provide you with the most suitable pre-treatment system that meets your specific requirements and expectations.