Home » Products » Pretreatment Systems » Spray Pretreatment
Spray Pretreatment
Flexible and efficient e-coating system.
Spray pretreatment is a method of cleaning and treating products by spraying cleaning agents and chemicals in the form of a spray through spray nozzles onto the surface. It usually uses a high-pressure water stream and the mechanical movement of the nozzle to achieve the spraying action.
Advantages:
- Uniformity: Spray pre-treatment sprays cleaning agents and treatment solutions uniformly over the entire product surface, ensuring that every area is adequately cleaned and treated.
- Efficient: spray pre-treatment enables the cleaning and treatment process to be completed in a short time, making it suitable for high throughput production environments and increasing production efficiency.
- Flexibility: Spray pre-treatment can be adapted to different product shapes and sizes for a wide range of product types and sizes.
- Resource-saving: Compared to dip tank pre-treatment, spray pre-treatment typically requires less cleaning agent and treatment fluid, thus reducing resource consumption.
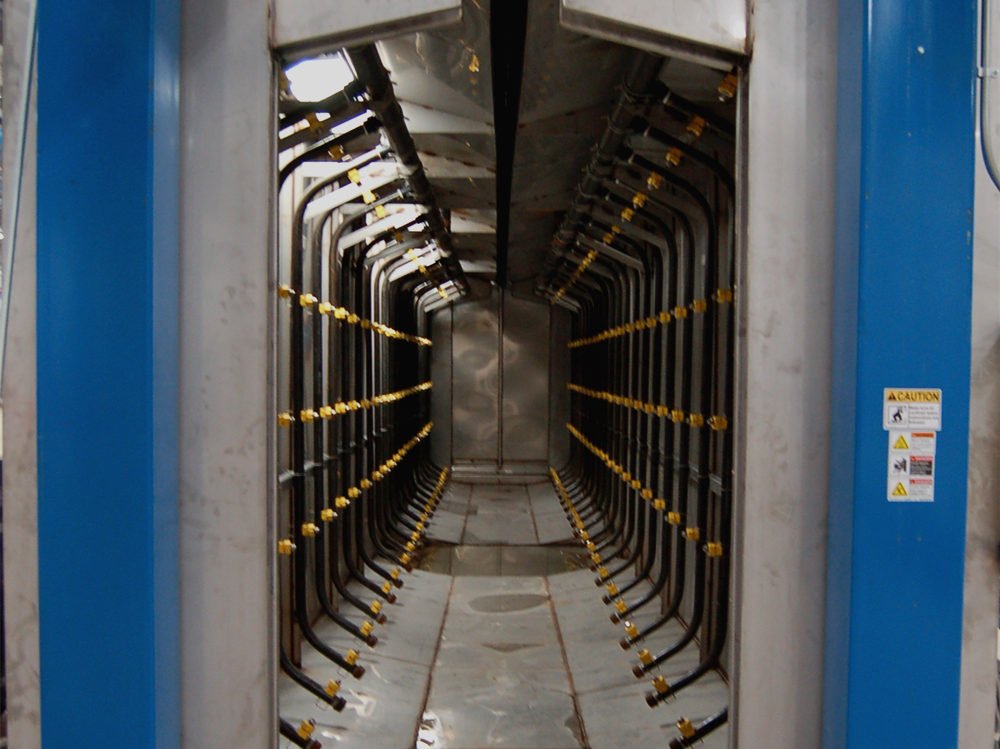

Product Description
Spray-on pre-treatment has an important role and importance in paint production.
The following are some key points on the importance of spray-on pre-treatment:
Thorough cleaning of the surface: Spray-on pre-treatment allows the surface to be thoroughly cleaned of dirt, grease, dust, and other impurities by spraying the treatment solution. This is a crucial step in the painting process as any impurities left on the surface can affect the adhesion and quality of the coating. Spray-on pre-treatment ensures that the product surface is clean and provides a good basis for the coating.
Improves coating adhesion: Spray-on pre-treatment increases the adhesion between the coating and the substrate, either by chemical reaction on the surface or by mechanical action. It removes surface oxides, rust, and other undesirable substances, providing a clean, rough surface that helps the coating adhere better to the substrate, providing better durability and protection.
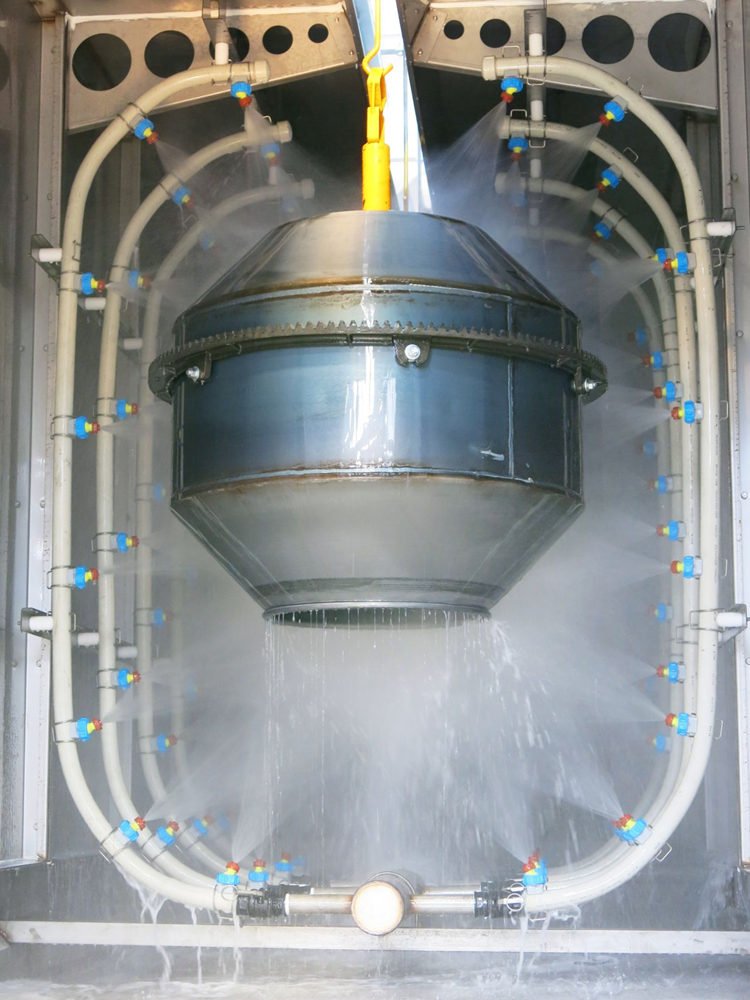
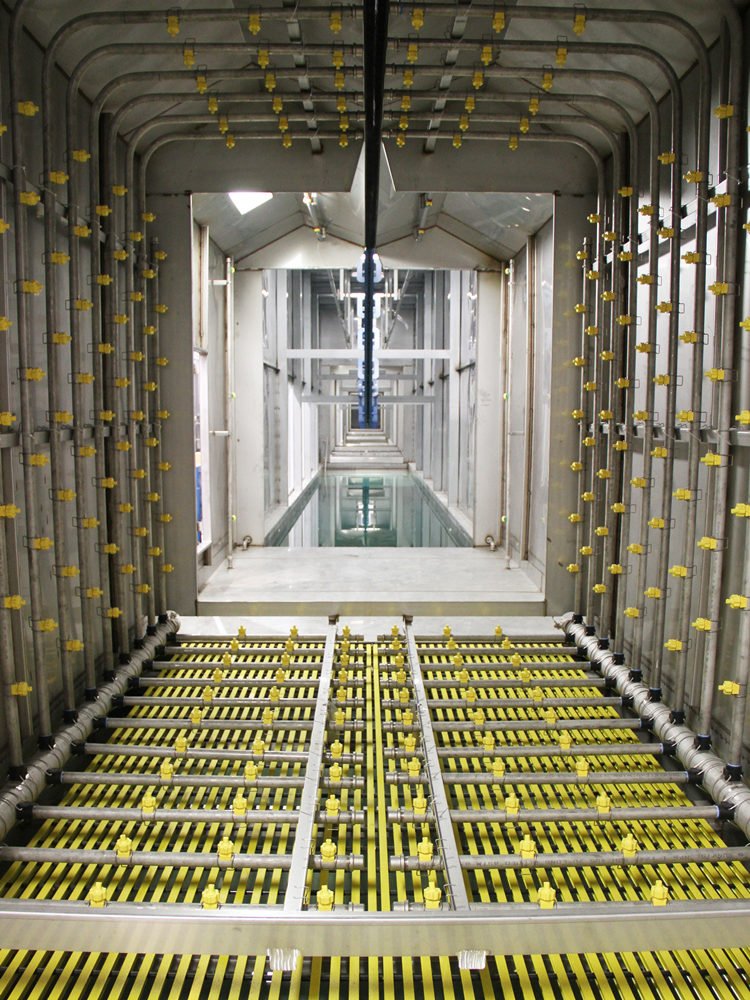
Enhanced corrosion resistance: Spray-on pre-treatment allows the application of special chemical solutions or coatings to form a protective layer of corrosion resistance. This protective layer protects the substrate from oxidation, corrosion, and other external aggressions, increasing the durability and longevity of the product.
Improved coating quality and consistency: spray pre-treatment enables uniform and consistent coating results. By controlling parameters such as the temperature, concentration, and spraying method of the spray solution, you can ensure that each product receives the same pre-treatment quality, avoiding problems such as uneven coating thickness and color variations, and improving the quality and consistency of the coating.
Increased process flexibility: Spray pretreatment has a high degree of process flexibility. Depending on the coating requirements and product characteristics, different treatment liquids, spraying methods, and process parameters can be selected to meet different application requirements. This flexibility makes spray pre-treatment suitable for a wide range of different types of products and coating processes.
Overall, spray pre-treatment plays an important role in coating production by ensuring product surface cleanliness, improving coating adhesion and corrosion resistance, increasing coating quality and consistency, and providing process flexibility. With spray pre-treatment, customers can achieve superior coating results, and improve the durability and appearance of their products, thus meeting market demands and increasing competitiveness.
Hinah Spray Pre-treatment Systems
Our spray pre-treatment systems offer the following product advantages:
- Automated conveying systems: By using automated conveying systems, our spray pre-treatment systems can increase productivity by a factor of 2-4 compared to manual and semi-automatic lines. Such an automated system significantly reduces labor costs and time consumption and increases productivity and throughput.
- Hinah automated pre-processing lines: Our system with Hanna automated pre-processing lines requires only one technician and two general workers to operate, thus saving even more human resources. This high degree of automation allows for a more efficient line and a better allocation of manpower.
- Optimization of spraying methods: We have optimized the spraying methods, shortened the system lines, and increased the efficiency of land use. Through precise spraying methods and layout design, we minimize material and water wastage, while ensuring consistency and stability of pre-treatment results.
- Water seal design: Our spray pre-treatment system uses a water seal design that keeps the top of the shed isolated from outside steam. This design effectively controls steam loss and maintains the stability and safety of the spray environment.
- High-quality materials: Our spray pre-treatment systems are manufactured from stainless steel and include the shed, tank, and spray pipework. These components are finely welded to ensure their strength and durability. As a result, our systems have a service life of more than 15 years and can operate consistently for a long time.
- Optimized design of the process sections: each process section is equipped with contoured baffles and appropriate transitions to prevent cross-flow phenomena. This optimized design maintains fluid separation between the process sections and ensures the effectiveness and quality of the process.
- Top ventilation: Our spray pre-treatment systems are designed with top ventilation to prevent acidic gases and vapors from accumulating at the top in time. This design ensures good ventilation within the system, effectively controlling the spread and build-up of gases and improving the safety of the operating environment.
- Safety and reliability: Our spray pre-treatment systems incorporate advanced safety measures to ensure the safety of operators and equipment. The systems feature multiple protection mechanisms such as overload protection, temperature monitoring, and emergency shutdown devices to ensure timely shutdown in abnormal situations and to avoid potential hazards.
- Environmental protection and energy saving: Our spray pre-treatment systems are designed with environmental protection and energy saving in mind. Through precise spraying methods and control systems, the system minimizes water and chemical consumption, thereby reducing the amount of wastewater discharged. In addition, the spraying system effectively controls the emission of exhaust gases and reduces the negative impact on the environment.
- Flexibility and customisability: Our spray pre-treatment systems can be custom-designed to meet the specific needs of our customers. Whether treating different types of material or responding to different sizes and process requirements, systems can be flexibly adapted and expanded. Our technical team will work with our customers to provide expert advice and solutions to meet their unique production needs.
- Automated control systems: Our spray pretreatment systems are equipped with advanced automated control systems that allow precise control of spray timing, spray dosage, and spray pattern. With real-time monitoring and adjustment, the system maintains consistent production efficiency and product quality, reducing the need for human intervention and improving the consistency and traceability of the production process.
- Ease of maintenance and servicing: Our spray pre-treatment systems are designed with ease of maintenance and servicing in mind. Key components and equipment are installed and removed in a modular design, making repair and replacement easier and more efficient.
In addition, the system offers comprehensive fault diagnosis and remote monitoring capabilities, allowing potential problems to be identified and resolved promptly, reducing downtime and production losses.
Product Features
- Automated conveying systems.
- Hinah automated pre-treatment lines.
- Optimisation of spraying methods.
- Water seal design.
- High quality materials.
- Optimised design of the process section.
- Top air permeation.
- Safety and reliability.
- Environmentally friendly and energy efficient.
- Flexibility and customisability.
- Automated control systems.
- Easy maintenance and servicing.
Need a design plan, now?
Product Video
FAQ
Answer: We understand your concern about the quality of the coating. To ensure consistent coating quality, we use advanced process controls and equipment to ensure that parameters such as temperature, concentration and pH of the treatment solution are precisely controlled. We also carry out stringent quality monitoring and testing to ensure that each product meets high quality standards. In addition, our engineering team will work with you to optimise the pre-treatment solution to your product characteristics and requirements in order to provide consistent and reliable coating results.
Answer: We take environmental protection and sustainable development very seriously. Our pre-treatment systems are designed with wastewater treatment in mind. We use advanced wastewater treatment technology to effectively remove pollutants from our wastewater through processes such as sedimentation, filtration and neutralisation, and ensure that the discharge meets environmental standards. We also actively promote the recycling of wastewater to minimise the impact on the environment. We continue to continuously improve our wastewater treatment technology to meet the needs of our customers and the environment.
Answer: Absolutely! Our pre-treatment systems are designed to be highly efficient and productive solutions. With automated control and intelligent operation, our systems enable fast processing and continuous production, increasing production efficiency and capacity. We also offer customised solutions, adapting the system configuration and parameters to your production needs and product characteristics to best meet your requirements.
Answer: We deeply understand your needs. Our pre-processing systems can be customised and integrated to suit the requirements of your existing production line. Our team of engineers will work with you to carry out site surveys and technical assessments to ensure that our systems fit seamlessly into your production line. We will provide the necessary technical support.
Answer: We attach great importance to emergency response and rapid repair services. We are equipped with a professional technical support team that can respond and solve system failures quickly. We offer a 24-hour technical support hotline and you can contact our technicians for assistance at any time. In addition, we offer our customers regular maintenance and servicing services to prevent breakdowns and extend the life of the equipment.
Answer: Our pre-treatment systems are carefully designed and manufactured using wear and corrosion resistant materials and high quality components to ensure the durability and stability of the system. In addition, we offer regular maintenance and servicing, including cleaning, lubrication and replacement of worn parts, to ensure proper operation and a long service life of the system. We also provide a supply of spare parts so that parts that need replacing can be replaced in a timely manner.
Answer: Yes, our pre-treatment systems focus on energy saving and efficient performance. We use advanced process control and automation technology to minimise energy consumption and optimise system operating efficiency. We also use intelligent monitoring and regulation devices to monitor and adjust the parameters of the treatment fluid in real time to ensure efficient use of energy. In addition, we offer consultancy and advice on energy management to help our customers further optimise energy consumption and operating costs.
Answer: Of course! Our company offers customised solutions for pre-treatment systems. Our team of engineers will work with you to gain an in-depth understanding of your needs and requirements and develop an individual solution based on your product characteristics, production processes and objectives. Our goal is to provide you with the most suitable pre-treatment system that meets your specific requirements and expectations.