E-coating line demands flawless paint bath purity to achieve uniform, defect-free finishes. Even microscopic contaminants—metal shavings, oils, or dust—disrupt deposition, causing pinholes, uneven textures, and weakened corrosion resistance. Traditional single-stage filters often fail to trap submicron particles, leading to costly rework and downtime.
Modern e-coating lines now integrate advanced filtration systems as a non-negotiable safeguard. By eliminating impurities down to 0.5 microns, these technologies preserve bath chemistry, extend coating material lifespan, and ensure consistent quality in automotive, aerospace, and industrial applications. Discover how precision filtration elevates e-coating performance while slashing operational costs.
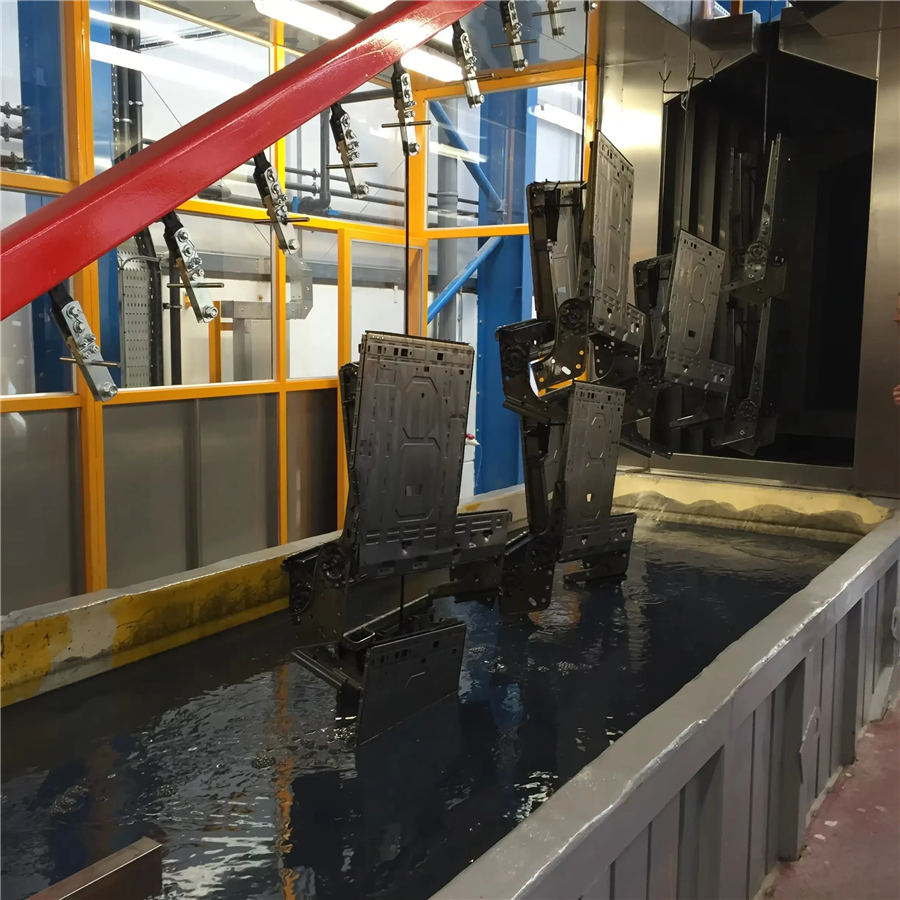
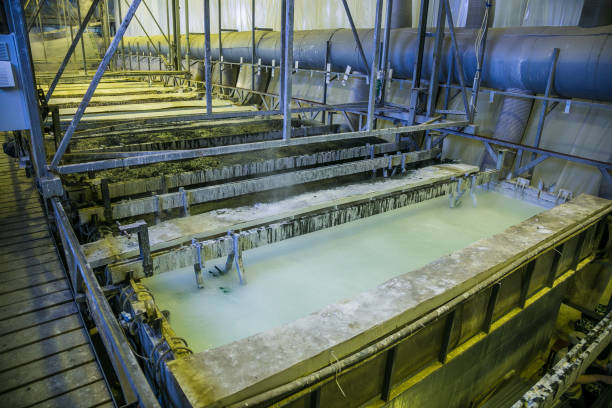
Common Contaminants in E-Coating Line Paint Bath
The effectiveness of an e-coating line hinges on maintaining pristine paint baths, yet contaminants inevitably infiltrate the system through multiple pathways. Understanding these pollutants is key to optimizing filtration strategies:
Primary Contaminant Types:
- Metal Particles: Iron or aluminum shavings from pretreatment stages or conveyor wear.
- Organic Residues: Oils, greases, or silicones from unrinsed substrates.
- Resin Aggregates: Gel-like clumps formed by unstable bath chemistry.
- Environmental Debris: Dust or fibers introduced during open tank transfers.
Critical Contamination Sources in E-Coating Line:
- Pretreatment Carryover: Residual phosphates or surfactants from inadequate rinsing.
- Mechanical Abrasion: Wear particles from pumps, hoses, or racking systems.
- Atmospheric Exposure: Airborne particulates in non-enclosed bath zones.
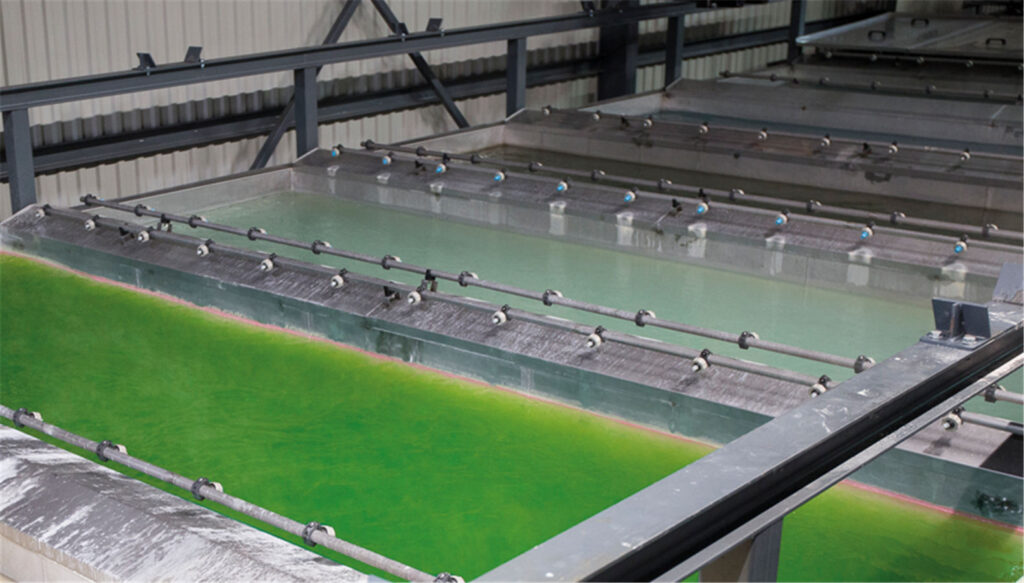
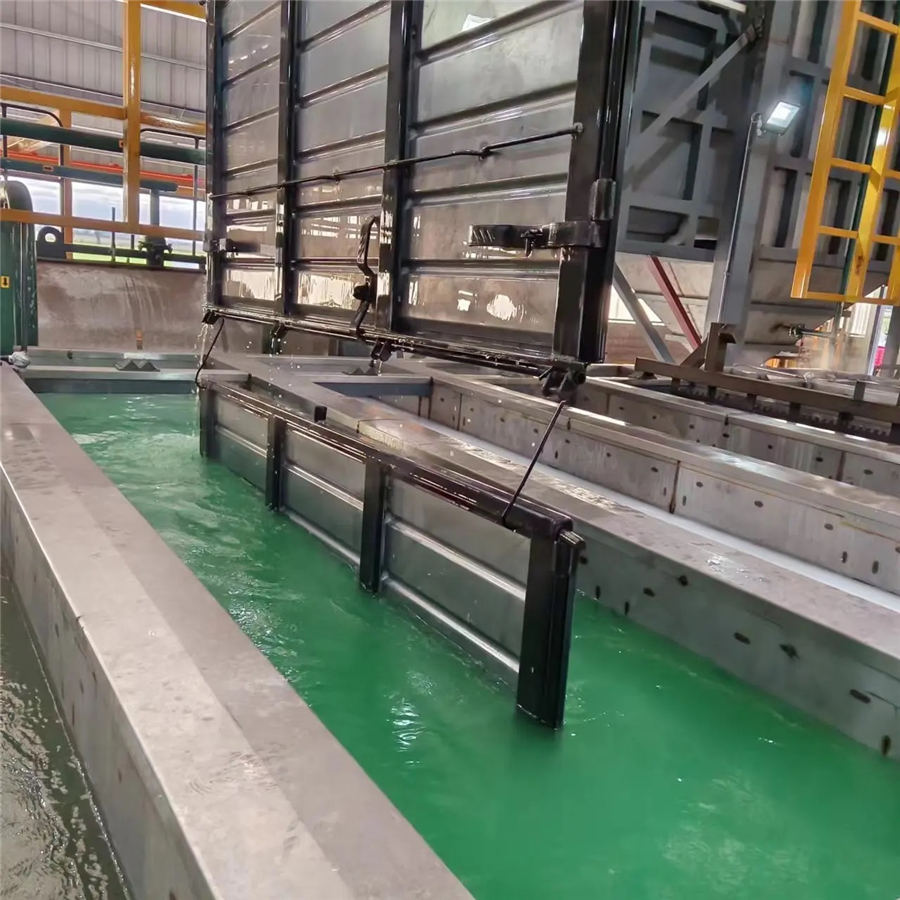
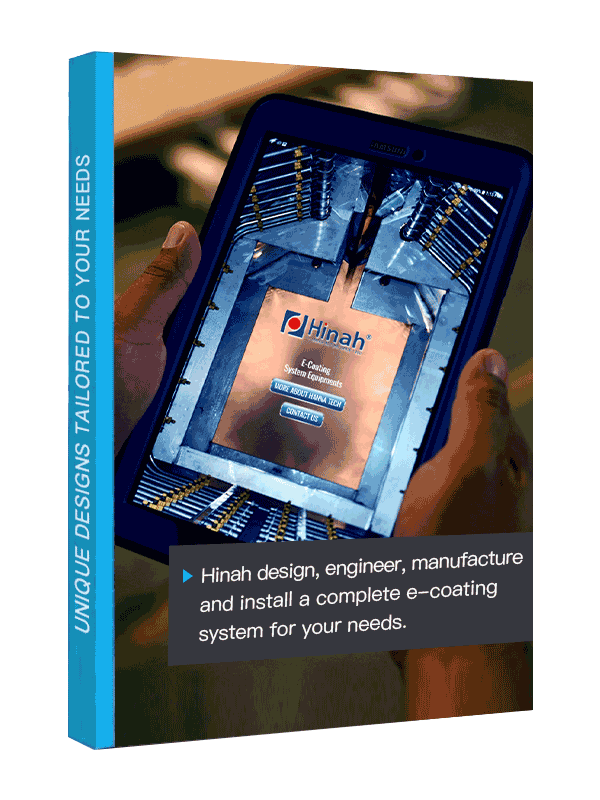
Let's Have A Chat
Get An E-coating Line Planning !
Match Your Products, Get The Solution & Price..
Traditional vs. Advanced Filtration Systems for E-Coating Line
The evolution of filtration technology in e-coating lines reflects the industry’s push toward precision and efficiency. Here’s how traditional methods stack up against cutting-edge solutions:
Traditional Filtration Systems: Limitations Exposed
- Single-Stage Design: Basic mesh filters (50–100 µm) trap large debris but ignore submicron particles.
- Frequent Downtime: Manual filter replacement every 40–60 hours disrupts production.
- Blind Spots: Unable to capture oils, gels, or particles below 5 µm, leading to gradual bath degradation.
- Reactive Maintenance: Issues detected only after defects appear on coated parts.
Advanced Filtration Systems: Precision Engineering for E-Coating Line
- Multi-Stage Filtration:
- Pre-filters (25 µm) remove bulk contaminants.
- Ultrafiltration modules (0.1–0.5 µm) target resins and emulsified oils.
- Magnetic separators extract ferrous particles missed by screens.
- Material Innovations:
- Ceramic membranes withstand harsh bath chemistries (pH 5–9).
- Nanofiber cartridges with electrostatic charge adsorb ultrafine particles.
- Smart Automation:
- Self-cleaning mechanisms triggered by pressure sensors.
- Real-time particle counters alert operators before contamination thresholds are breached.

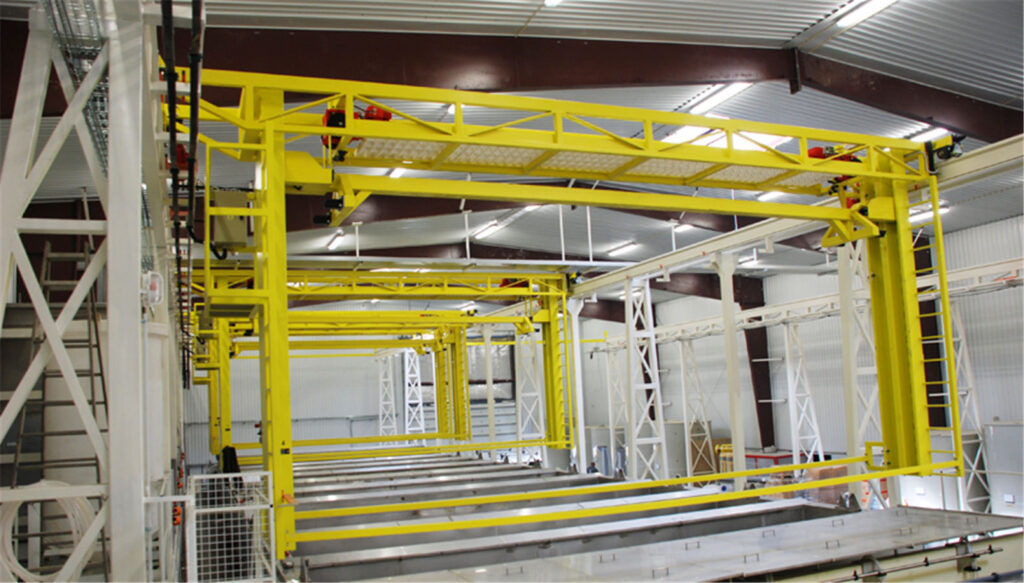
Key Components of Modern E-Coating Line Filtration Systems
- Multi-Stage Pre-Filtration Units
Multi-stage pre-filtration units act as the first defense, removing debris larger than 25 µm (rust, dirt, pretreatment residues) using corrosion-resistant stainless steel screens and layered filter cartridges. By blocking coarse particles early, they protect downstream sophisticated equipment like pumps and ultrafiltration modules, reducing wear and maintenance costs in high-volume e-coating operations.
- Ultrafiltration (UF) Membrane Modules
Ultrafiltration membranes target submicron contaminants (0.1–0.5 µm), including emulsified oils and resin gels. Made of pH-resistant ceramic or polymers, they operate in harsh bath environments while recirculating paint to minimize waste. This stabilizes bath conductivity and cuts VOC emissions by 20–30%, ensuring consistent coating quality.
- Magnetic Separators
High-gradient rare-earth magnetic separators (12,000+ Gauss) capture micron-sized ferrous particles like iron shavings, which evade traditional filters. Auto-cleaning wipers purge debris into sludge tanks, eliminating manual intervention. Critical for automotive e-coating lines, they prevent metal-induced coating flaws.
- Automated Backflush Systems
Automated backflush systems clear blockages with reverse-flow pulses triggered by pressure sensors or IoT algorithms. This extends filter lifespan 4x vs. manual cleaning and reduces downtime—e.g., a plant reported 40% fewer stoppages post-implementation.
- Real-Time Monitoring Sensors
Sensors track particle counts, turbidity, and pressure drops, feeding data to SCADA systems for predictive maintenance. In aerospace applications, they’ve preempted defects by triggering purges during particle spikes, ensuring contamination-free baths.