In harsh industrial environments, aluminum parts face relentless challenges—corrosion from moisture and chemicals, uneven wear on complex geometries, and ever-tighter regulations around environmental impact. Traditional finishing methods often fall short, leaving critical components vulnerable to premature failure and costly downtime.
Enter e coating aluminum, a high-precision, immersion-based process that delivers uniform, chemically bonded coatings even in the most intricate recesses. By combining exceptional corrosion resistance with minimal waste and energy use, e coating aluminum is reshaping how manufacturers protect and prolong the life of their parts—unlocking performance gains that were once out of reach.
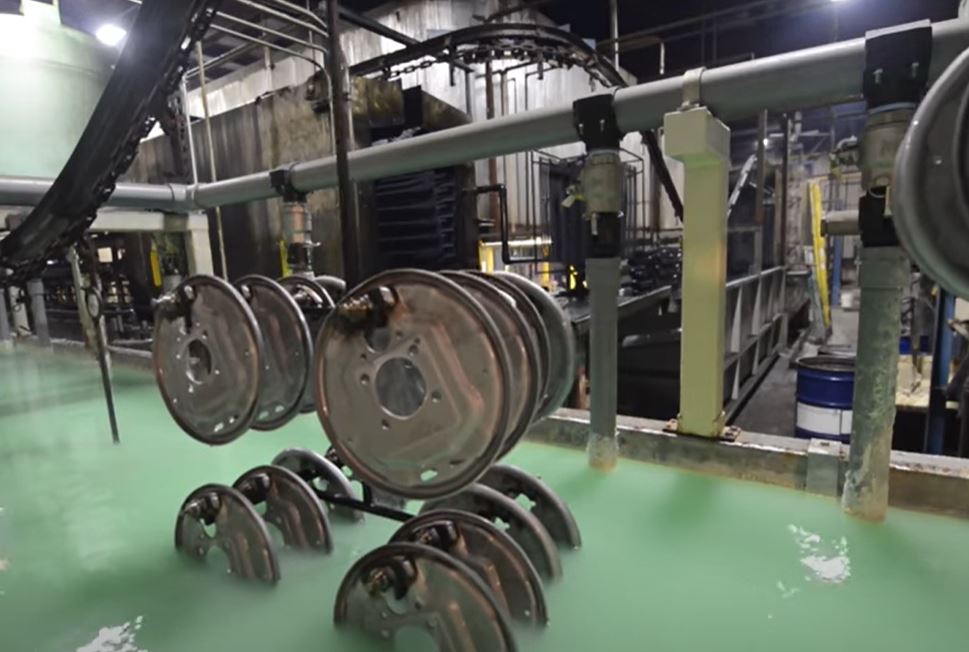
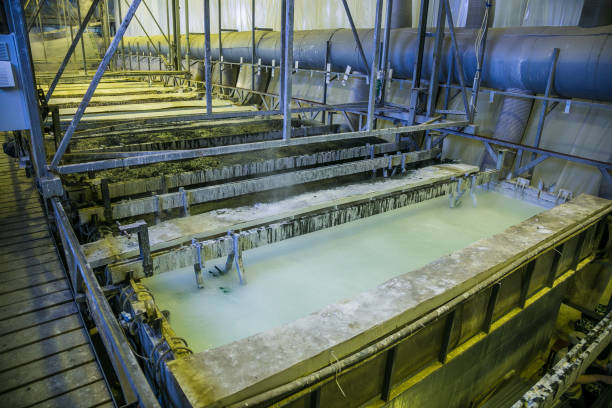
I. What Is E Coating Aluminum?
E coating aluminum is an electro-deposition finishing process in which charged paint particles are drawn to a grounded aluminum substrate through an immersion bath. During this process, parts are first cleaned and pret-treated to remove oils and oxides, then submerged in a water-based bath containing electrically charged coating resin. When an electric current is applied, the resin particles uniformly deposit onto every exposed surface, forming a thin, tightly bonded film. After removal from the bath, the parts are cured in an oven to cross-link the coating, creating a tough protective layer.
Unlike spray-on or powder methods, e coating aluminum achieves complete coverage—even in deep recesses and intricate profiles—thanks to the attraction of charged particles. Traditional spray painting can leave thin spots or runs, and powder coating often struggles with sharp edges or internal cavities. E coating also operates at lower film thicknesses, reducing material usage and ensuring consistent adhesion, which translates into superior corrosion resistance and longer service life for industrial components.
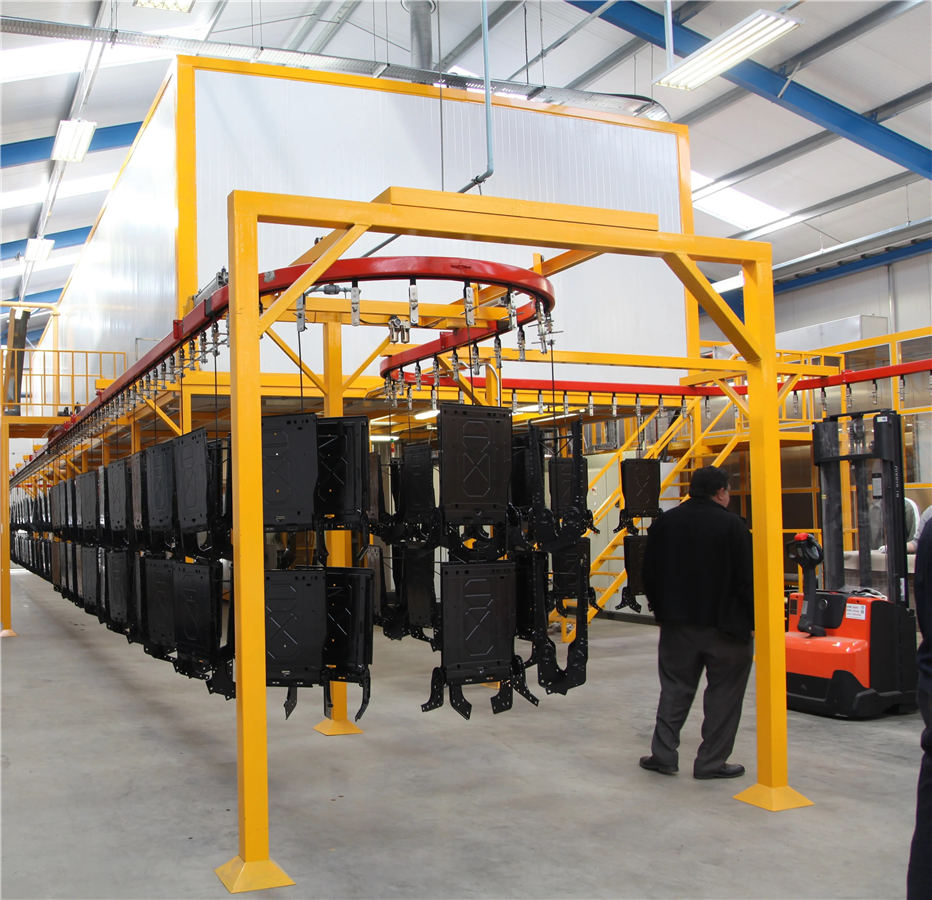
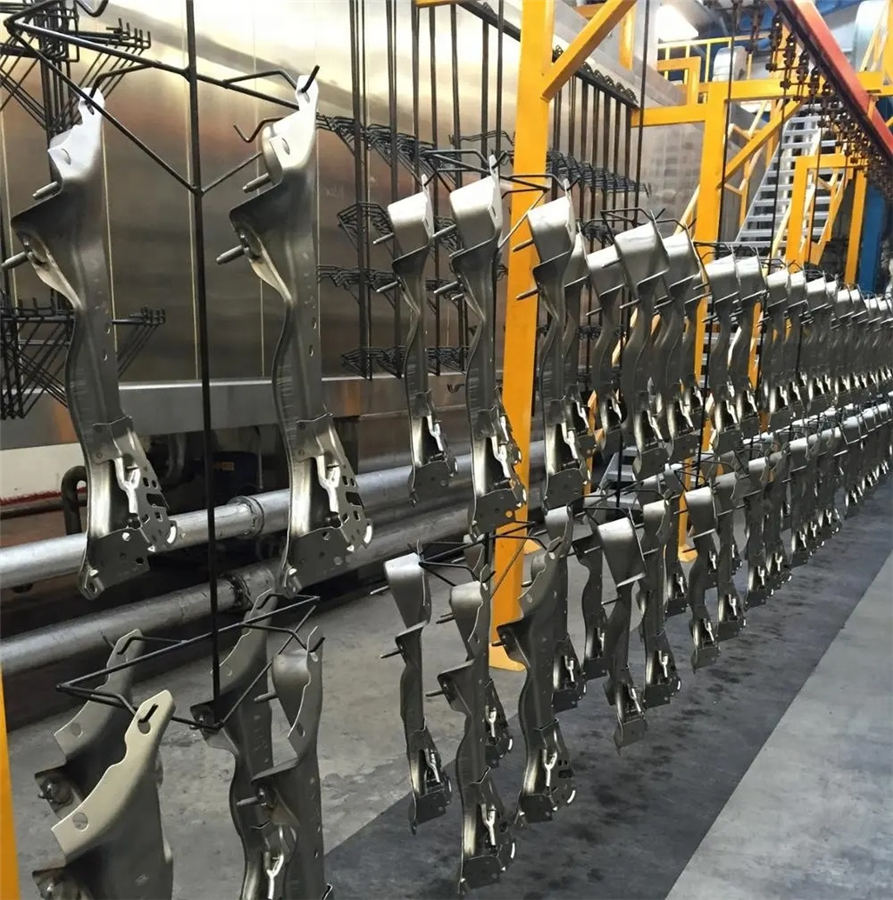
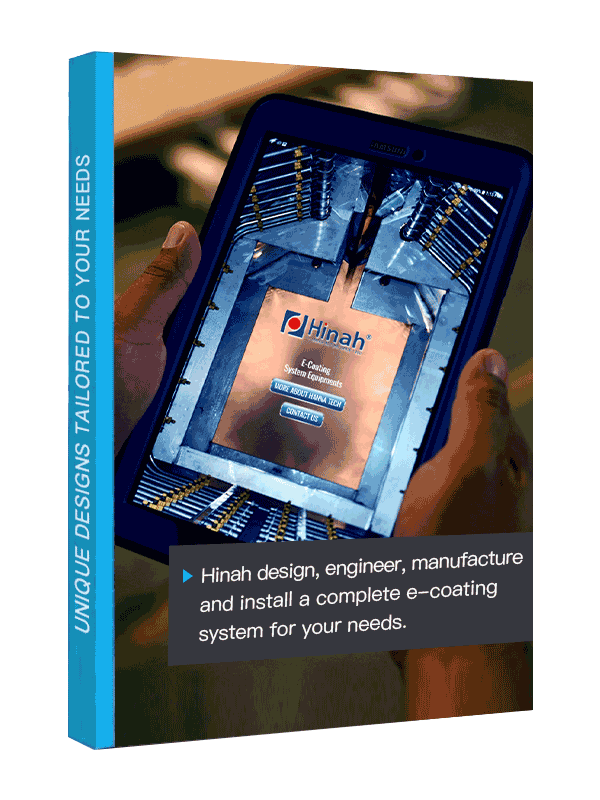
Let's Have A Chat
Get An E-coating Line Planning !
Match Your Products, Get The Solution & Price..
II. How Does the E Coating Aluminum Process Work?
The e coating aluminum workflow unfolds in three core stages:
- Cleaning & Degreasing: Parts enter a multi-stage wash to strip oils, machining residues, and fingerprints.
- Conversion Coating: A chemical conversion (typically phosphate or zirconium) is applied to activate the aluminum surface, promoting adhesion and enhancing corrosion protection.
2. Immersion (Electrodeposition)
- Bath Composition: Parts are submerged in a water-based tank containing finely dispersed, electrically charged coating resin.
- Electrical Charge: The aluminum acts as the cathode while anodes in the bath carry the opposite charge. Once voltage (typically 200–400 V) is applied, resin particles migrate and deposit uniformly on all exposed surfaces.
- Deposition Time: Controlled immersion time (often 2–4 minutes) determines the wet film thickness, generally in the 15–25 µm range before curing.
3. Curing oven
- Oven Bake: Coated parts travel through an oven at 160–200 °C for 20–30 minutes.
- Cross-Linking: Heat triggers chemical cross-linking, converting the wet film into a hard, chemically bonded finish that resists abrasion, chemicals, and corrosion.
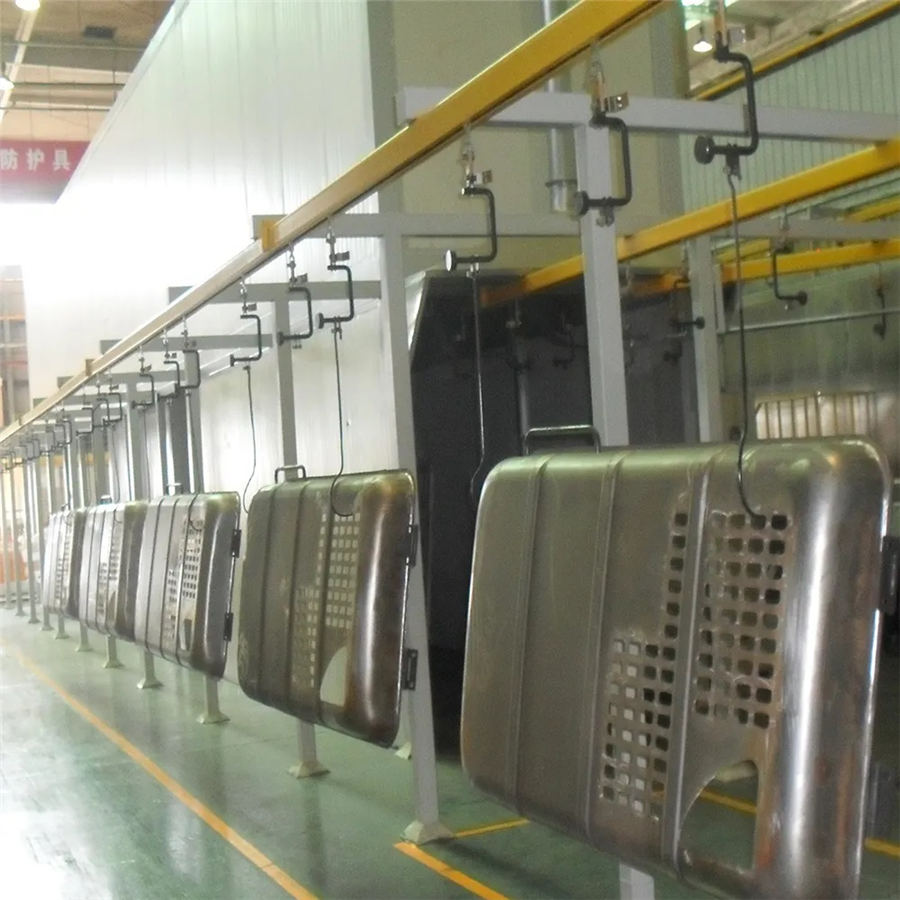
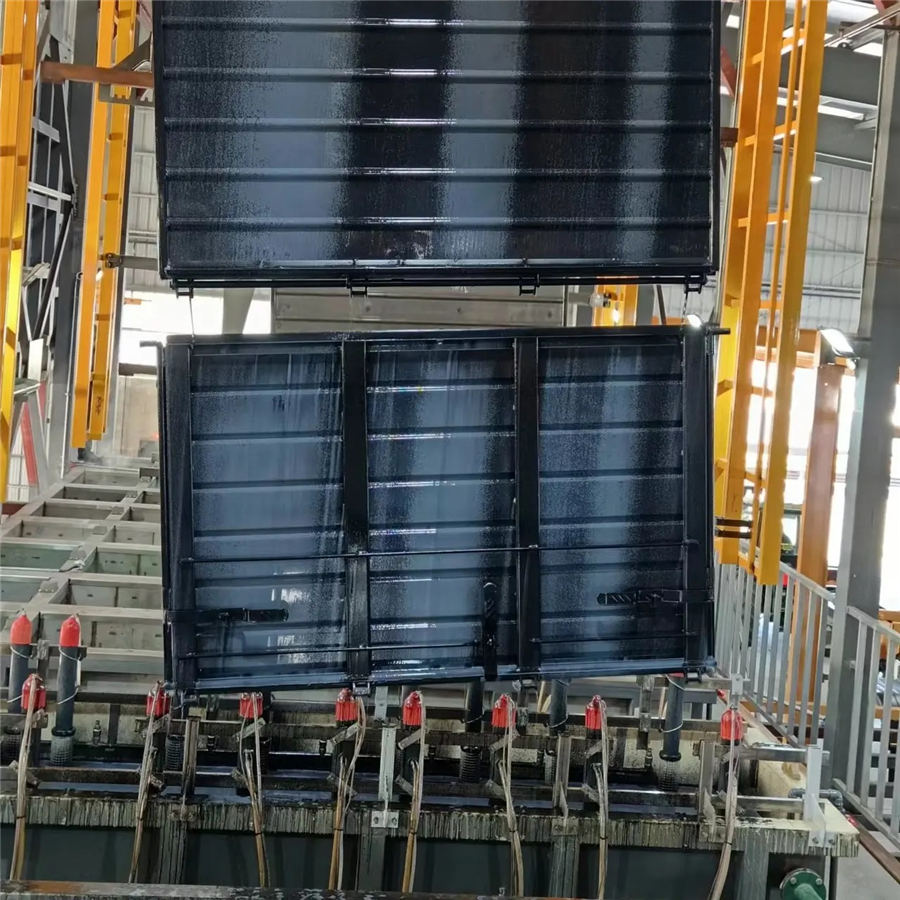
III. Key Benefits of E Coating Aluminum for Industrial Parts
- Corrosion Resistance and Durability
E coating aluminum delivers an exceptionally uniform, chemically bonded finish that protects parts against rust, salt spray, and chemical exposure far better than conventional paint systems. The tight adhesion created during the curing stage prevents underfilm corrosion, meaning even if the coating is scratched, moisture cannot easily penetrate to the bare metal. Over its service life, e-coated aluminum parts maintain structural integrity and appearance, reducing replacement cycles and unplanned downtime.
- Uniform Coverage on Complex Geometries
One of the standout advantages of e coating aluminum is its ability to coat every surface—inside bores, under flanges, and around sharp edges—without thinning or runs. Charged resin particles are drawn into and adhere to all exposed areas, ensuring consistent film thickness across both simple and highly intricate components. This uniformity not only maximizes protection but also eliminates costly touch-up work and inspection failures often associated with spray or powder methods.
- Environmental and Cost Advantages
Because e coating aluminum uses a water-based bath, volatile organic compound (VOC) emissions are minimal compared to solvent-borne paints, helping manufacturers meet stringent environmental regulations. The process also boasts high transfer efficiency—typically over 95%—which means less wasted material and lower raw-coating costs. Additionally, the thin, consistent films require less energy to cure, translating into reduced oven run times and utility expenses, while delivering a premium finish that drives down total cost of ownership.
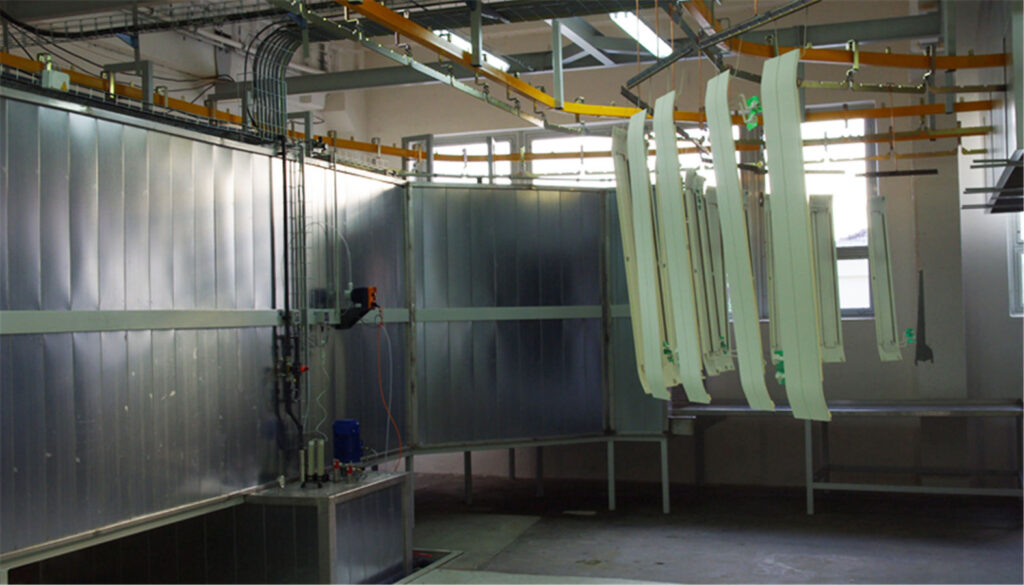
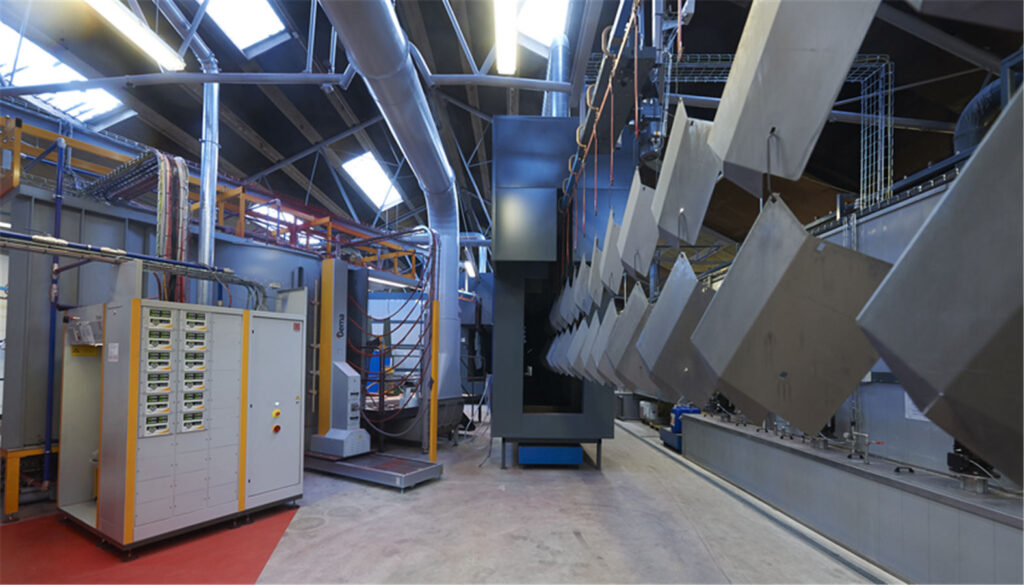
IV. Conclusion
E coating aluminum stands out as the definitive solution for industrial part protection—combining unmatched corrosion resistance, flawless coverage on even the most intricate geometries, and a greener, cost-efficient footprint. By embracing this electro-deposition technology, manufacturers can significantly extend component life, reduce maintenance and rework, and achieve compliance with tightening environmental standards.
Ready to transform your production line? Partner with an experienced e-coating provider to tailor a process that meets your exact specifications and unlocks the full potential of aluminum in your applications.