In an era where vehicles face increasingly harsh environments—from road salt to extreme temperatures—the demand for long-lasting car parts has never been higher. This is where e-coating line technology emerges as a game-changer.
Electrophoretic coating (e-coating) systems apply a uniform, electrostatically bonded layer to metal surfaces, ensuring complete coverage even on complex geometries like engine brackets or underbody components—a critical advantage as electric and autonomous vehicles push coating performance to new limits.
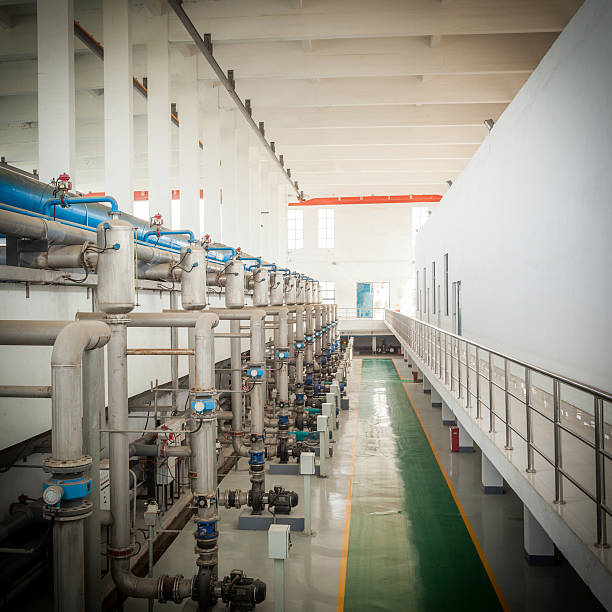
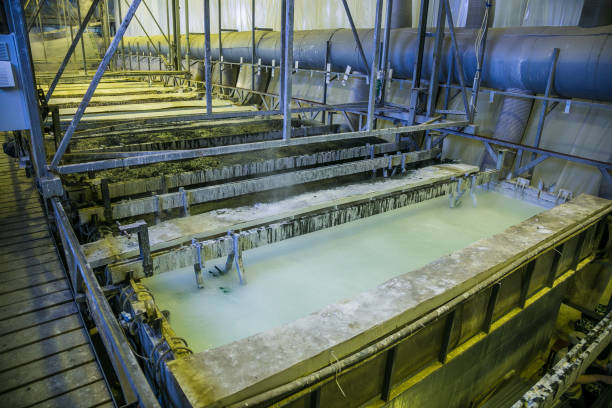
How E-Coating Line Technology Boosts Car Parts Durability
1. Electrostatic Deposition Ensures Complete, Durable Coverage
E-coating line technology leverages electrophoresis, a process where an electric field directs charged paint particles to uniformly coat grounded metal surfaces. This method eliminates coverage gaps, even on complex geometries like threaded bolts or engine brackets, by ensuring 100% surface adhesion. The electrostatic bond formed during deposition is 2-3x stronger than traditional spray methods, preventing flaking and creating a foundation for long-term corrosion resistance. By penetrating recesses and edges that manual spraying often misses, e-coating lines eliminate weak spots—critical for parts like suspension components exposed to road debris and moisture.
2. Built-In Corrosion and Wear Resistance
The cured e-coating film acts as a molecular shield, offering multi-layered protection against environmental stressors. Its dense, non-porous structure blocks salt, moisture, and UV radiation—key culprits in automotive degradation. Additionally, the coating’s abrasion resistance prevents chipping in high-impact areas like wheel hubs and brake calipers, ensuring parts retain structural integrity even under gravel bombardment or thermal cycling.
3. Thermal Curing Locks in Long-Term Performance
The final durability boost comes from precision thermal curing, where coated parts are baked at 160–200°C. This stage transforms the deposited particles into a seamless, crosslinked film with enhanced chemical and mechanical properties. The curing process increases hardness while maintaining flexibility, preventing cracks during part vibrations or impacts. It also reduces porosity, creating a moisture-proof barrier that withstands extreme temperatures.
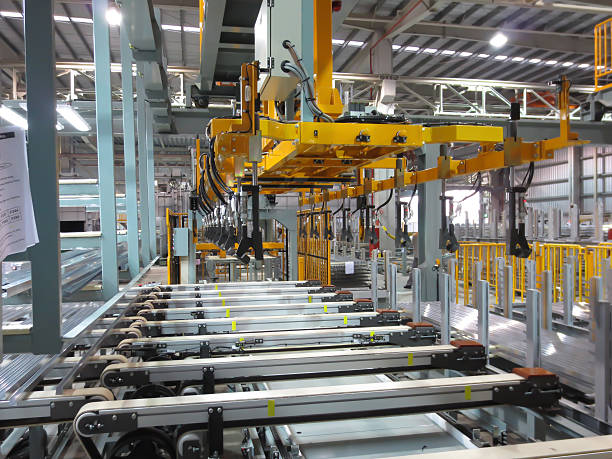
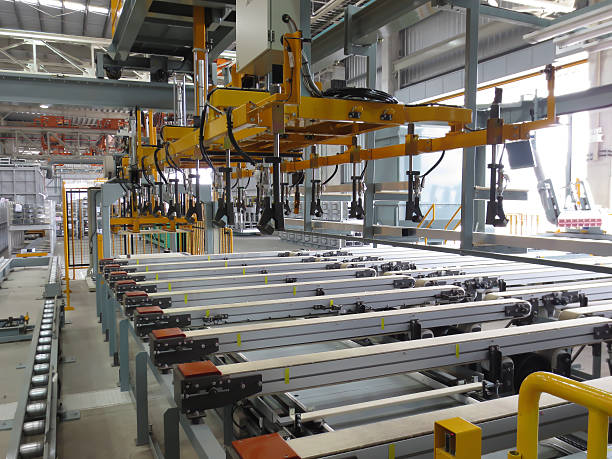
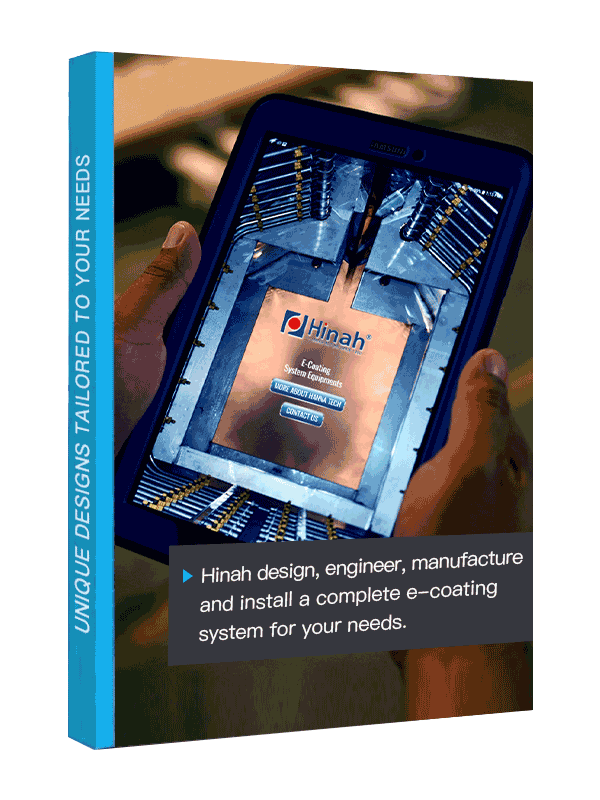
Let's Have A Chat
Get An E-coating Line Planning !
Match Your Products, Get The Solution & Price..
Key Automotive Applications of E-Coating Line Systems
- Underbody & Structural Components
E-coating lines provide 15–25 µm uniform coatings that penetrate recesses and welds on chassis frames and suspension parts, blocking corrosion in salt-rich environments. With 1,500+ hours of ASTM B117 salt spray resistance, these coatings triple the lifespan of underbody components compared to traditional methods, reducing winter-driven warranty claims by 35%.
- Wheels & Brake Systems
Thin yet robust 10–15 µm e-coatings protect alloy wheels and brake calipers from gravel impacts (SAE J400 compliant) and 200°C heat. Real-world data shows 95% coating integrity after 8 years—outperforming liquid paints by 35%—while preventing galvanic corrosion on lightweight alloys.
- Engine Bay & Powertrain Parts
E-coating lines create chemically resistant films for engine mounts and heat shields, surviving 1,000+ thermal cycles (-40°C to 150°C). The cured coatings repel oils and fuels (ASTM D1308 tested), with turbocharged engine brackets showing zero corrosion after 7 years of extreme heat and vibration.
- EV-Specific Components
EV battery enclosures and motor housings benefit from e-coating’s moisture-proof, UL 94 V-0 flame-retardant films. By preventing galvanic corrosion in multi-metal designs, the technology cuts defects by 30% in humid climates, while insulating layers ensure electrical safety in high-voltage components.
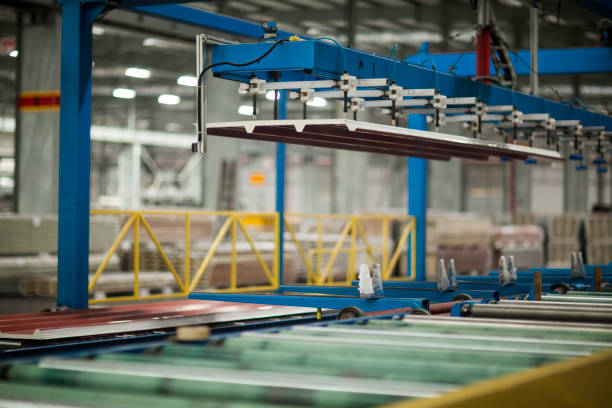
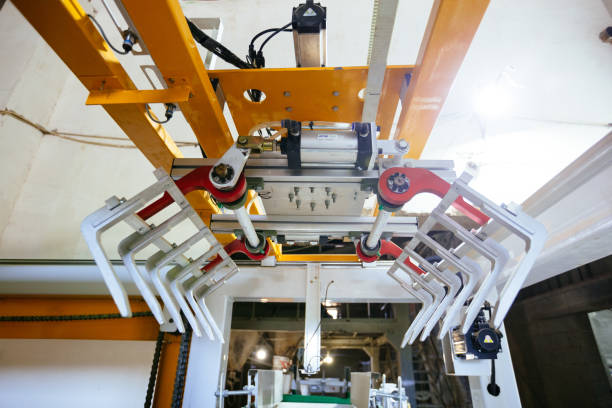
Conclusion
The e-coating line has redefined durability in automotive manufacturing, offering unmatched protection for components exposed to harsh environments. As the automotive industry shifts toward electric and lightweight designs, e-coating lines will remain pivotal in meeting evolving durability demands while cutting lifecycle costs.
Ready to future-proof your automotive components? Explore how our e-coating line solutions deliver lifespan-defining protection for your most critical parts.