Electrical conductivity is a cornerstone parameter in modern electrocoating line operations, directly influencing coating quality, process stability, and production efficiency. In cathodic electrodeposition systems, conductivity measures the tank liquid’s ability to carry electrical current, which governs how uniformly paint particles migrate and adhere to substrates.
For industrial electrocoating lines, maintaining conductivity within a strict range is non-negotiable. Deviations compromise coating performance, emphasizing the need for precise monitoring and control systems tailored to electrocoating processes.
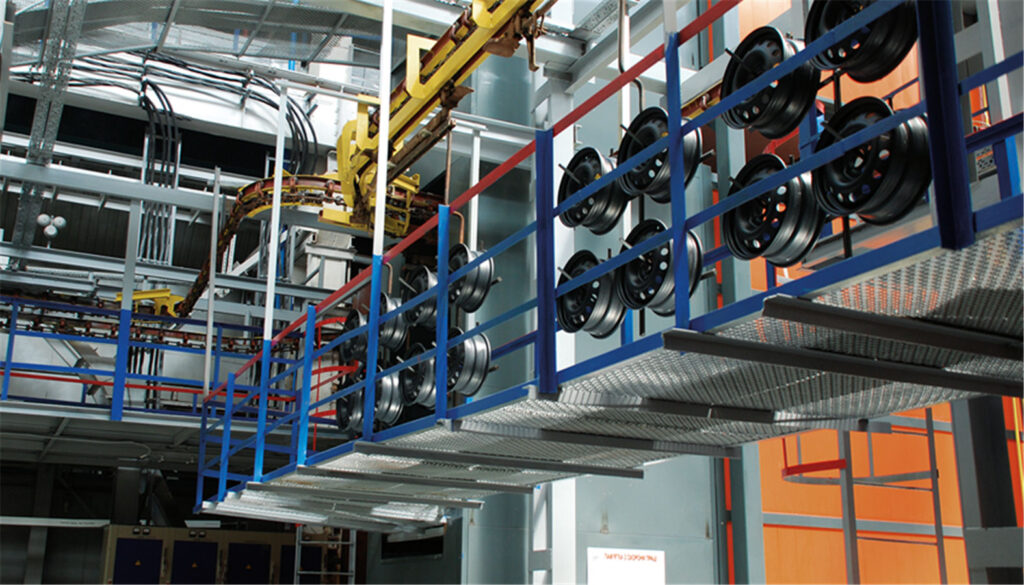
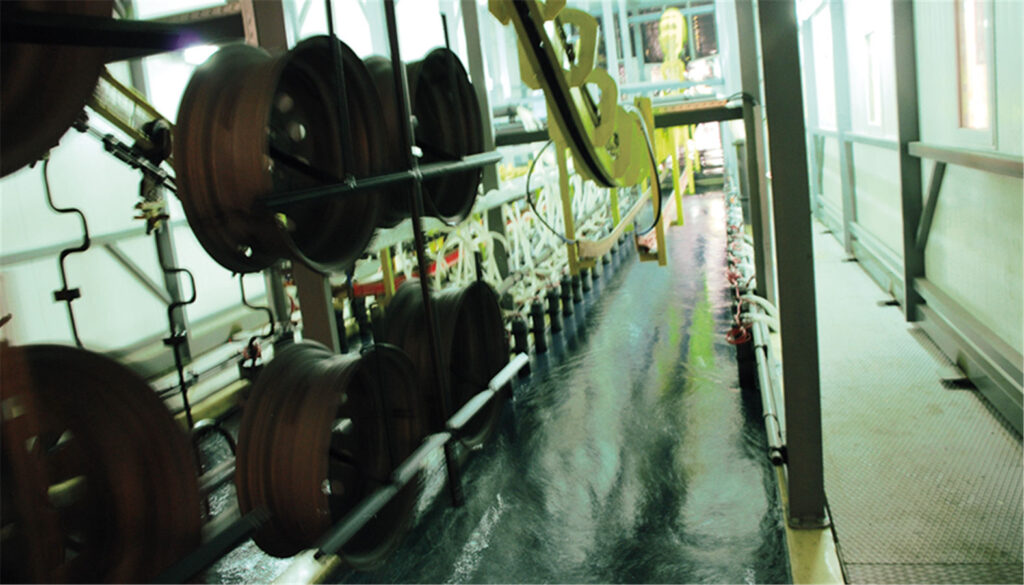
I. What is Conductivity in Electrocoating Line
In the context of electrocoating line processes, conductivity serves as a fundamental metric to evaluate the electrical behavior of the tank liquid. Defined as the ability of a solution to conduct electric current, conductivity is measured in microsiemens per centimeter (μS/cm) and is inversely proportional to specific resistance (Ω·cm). This relationship is mathematically expressed as:
For example, a tank liquid with a conductivity of 1,200 μS/cm has a specific resistance of approximately 833 Ω·cm.
In practical electrocoating line operations, conductivity directly reflects the concentration of ions in the bath, including resin solids, pH-adjusting agents, and contaminants. These ions facilitate the electrodeposition process by enabling current flow, which drives paint particles to adhere to the substrate. However, excessive ionic content (e.g., from impurities or degraded resin) elevates conductivity, destabilizing the bath and compromising coating quality.
Key Measurement Points
To maintain process stability, conductivity is monitored at critical stages within the electrocoating line:
- Main Tank Liquid: The primary focus, where conductivity typically ranges between 900–1,500 μS/cm for cathodic electrocoating. Deviations signal issues like contamination or resin depletion.
- UF Permeate: Ultrafiltration (UF) systems produce permeate used for rinsing. Conductivity here must stay low (<50 μS/cm) to avoid reintroducing ions into the bath.
- Anolyte/Catholyte: Electrode compartments require stable conductivity to prevent pH swings and ensure efficient current distribution.
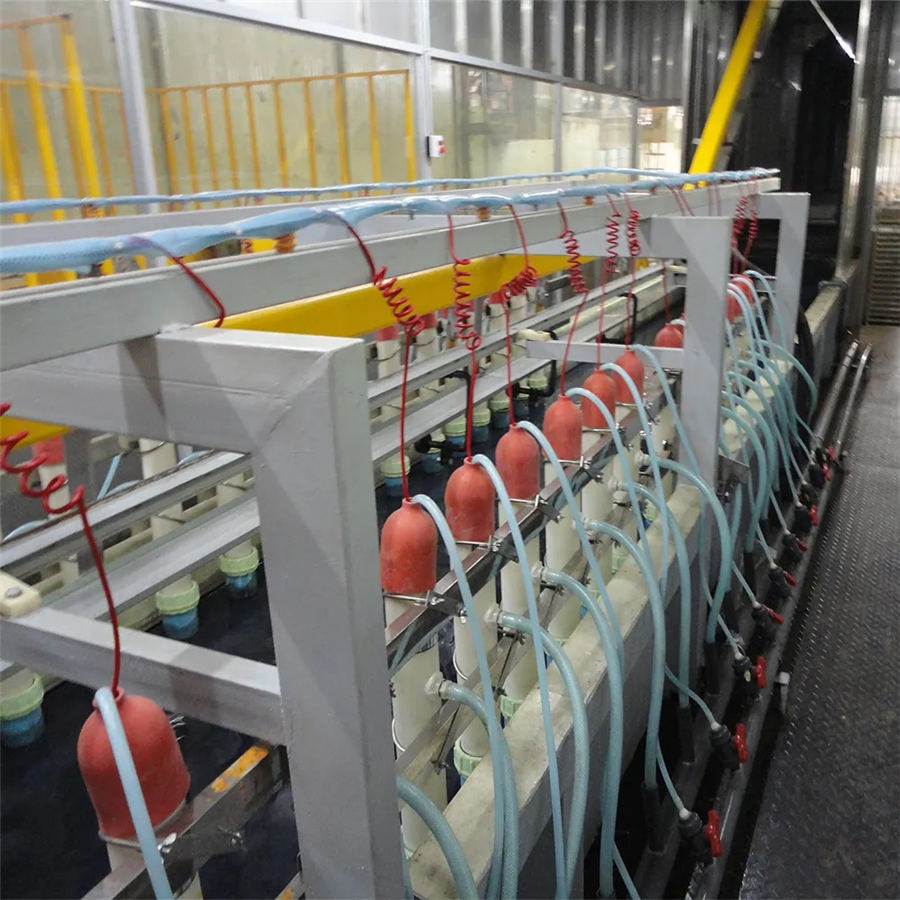
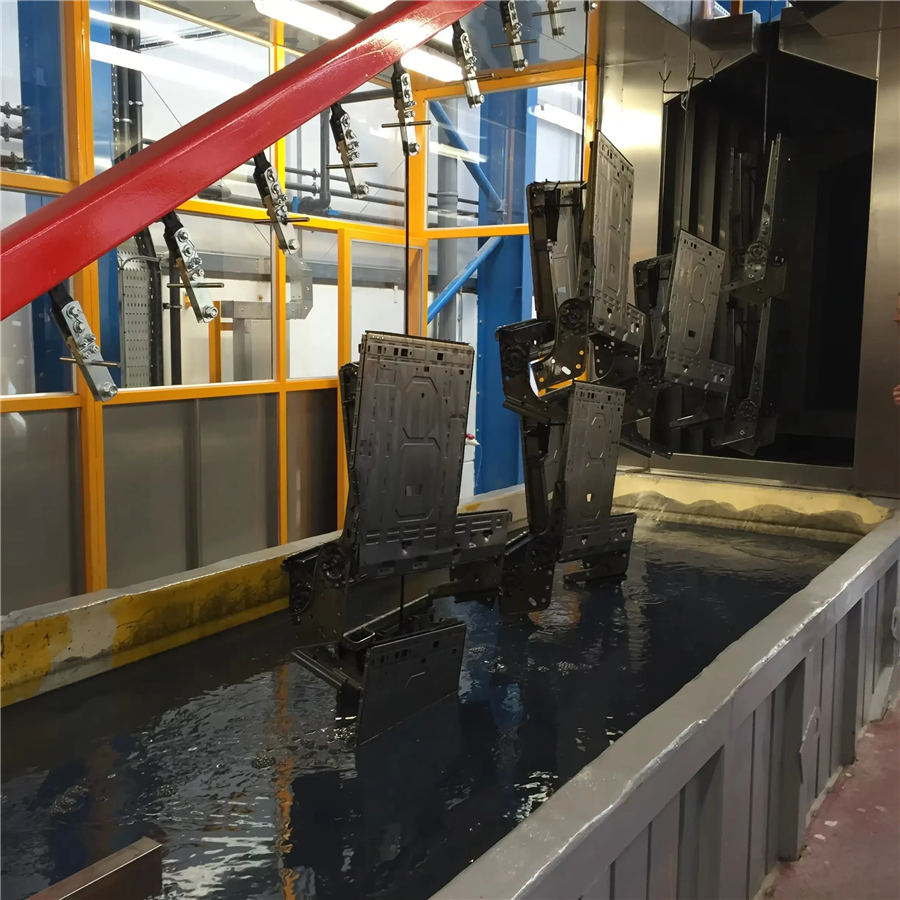
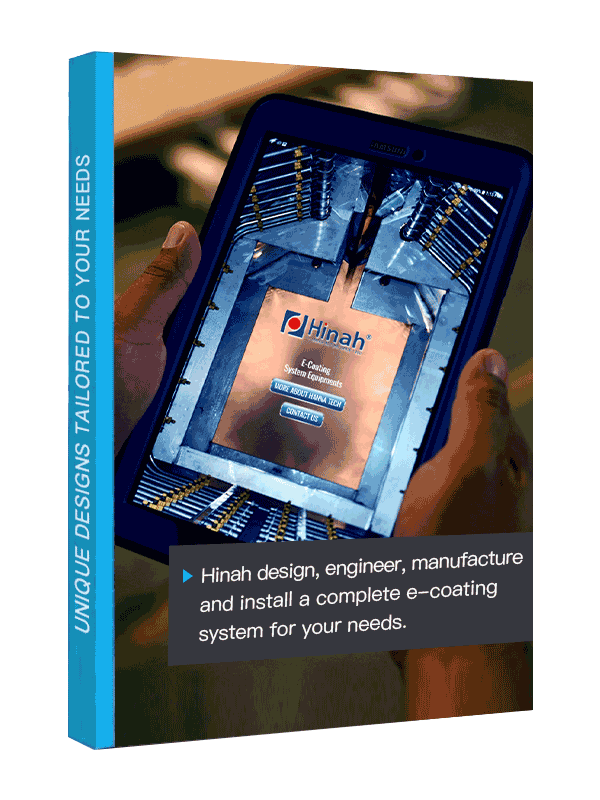
Let's Have A Chat
Get An E-coating Line Planning !
Match Your Products, Get The Solution & Price..
II. Factors Affecting Conductivity in Electrocoating Line
- Tank Liquid Composition
Conductivity in electrocoating line is primarily governed by the tank liquid’s chemical makeup. Resin solids content directly influences ionic activity, as higher concentrations of charged polymer groups elevate conductivity, though excessive solids can destabilize deposition uniformity. Simultaneously, pH levels within the typical cathodic electrocoating range (5.8–6.5) modulate ion mobility; deviations outside this window disrupt conductivity and trigger defects like pinholes. Contaminant ions (e.g., Na⁺, Cl⁻) introduced through substrates or water further exacerbate conductivity spikes—for instance, 100 ppm of chloride ions can increase conductivity by 200–300 μS/cm, demanding rigorous impurity control.
- Process Parameters
Operational settings play a pivotal role in conductivity dynamics. Bath temperature fluctuations directly impact ion migration rates: elevated temperatures (>35°C) temporarily boost conductivity by accelerating ionic movement but risk long-term resin degradation if sustained. Voltage settings also interact with conductivity—higher voltages intensify current flow, amplifying ionic activity. However, mismatched voltage-conductivity pairings may lead to over-deposition on edges or uneven coating coverage, emphasizing the need for synchronized parameter adjustments in e-coating line operations.
- Water Quality & Rinse Systems
The purity of deionized water used in bath replenishment and rinsing is critical. Water exceeding 5 μS/cm introduces contaminant ions, gradually elevating tank conductivity. Ultrafiltration (UF) systems mitigate this by removing excess ions through permeate recycling, but aging UF membranes or inadequate flushing can compromise efficiency, inadvertently reintroducing impurities into the e-coating line. Consistent monitoring of rinse water conductivity ensures ionic loads remain within safe thresholds, preserving bath stability.
- Electrode Maintenance
Electrode health directly impacts conductivity control. Degraded anodes or cathodes release metal ions (e.g., Fe²⁺) into the bath, artificially inflating conductivity and altering deposition behavior. Membrane failures in electrode compartments further destabilize the system by allowing electrolyte crossover, which disrupts pH balance and conductivity. Regular electrode cleaning and membrane inspections are essential to prevent ionic contamination, ensuring stable performance in high-throughput electrocoating line.

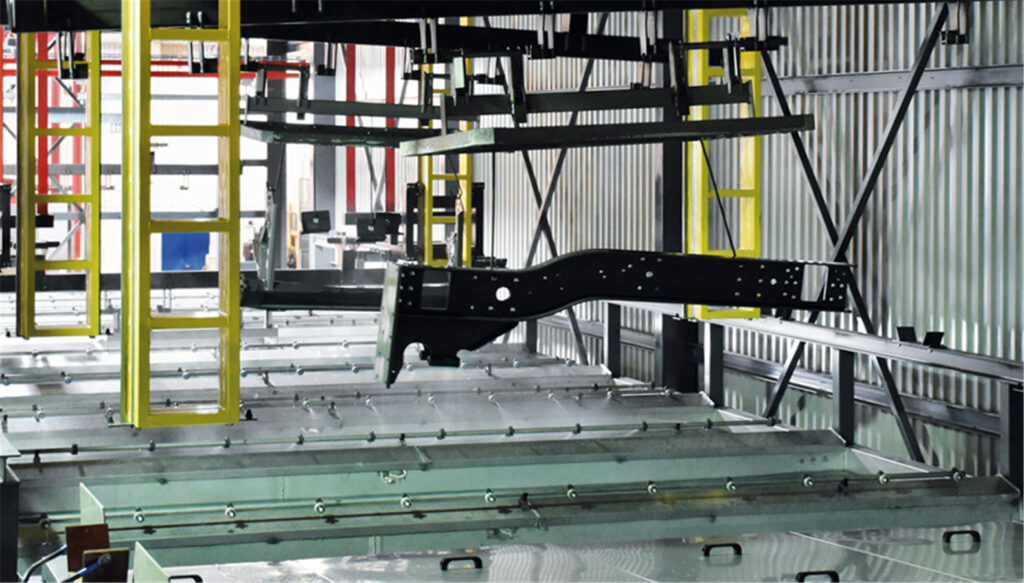
III. How Conductivity Shapes Electrocoating Line Outcomes
Conductivity is a decisive factor in determining the performance and quality of electrocoating line outputs, directly influencing deposition efficiency, film properties, and operational costs.
In cathodic electrodeposition, higher conductivity enhances throwing power—the ability of paint to penetrate recessed areas—by facilitating stronger current flow, which drives resin particles to uniformly coat complex geometries. For instance, within the optimal range (1200±300 μS/cm), conductivity ensures consistent film thickness (e.g., 20–25 μm) and smooth finishes. However, excessively high conductivity (>1500 μS/cm) accelerates deposition rates, leading to overly thick films (>35 μm) prone to defects like orange peel or edge buildup, while also increasing energy consumption due to elevated current demands. Conversely, low conductivity (<900 μS/cm) reduces throwing power, leaving cavities inadequately coated and producing thin, porous films (<15 μm) with compromised corrosion resistance.
The relationship between conductivity and film quality extends to defect generation. Impurity-driven conductivity spikes (e.g., from Na⁺ or Cl⁻ contamination) destabilize the bath, causing erratic particle migration that manifests as pinholes, craters, or redissolution marks. In electrocoating lines, such defects escalate rework rates and material waste. Furthermore, conductivity impacts long-term bath stability: uncontrolled ionic accumulation degrades resin efficiency, shortening bath life and necessitating costly replacements. Modern systems address these challenges by integrating real-time conductivity sensors with automated UF permeate flushing, ensuring deviations are corrected before they affect output. By aligning conductivity with substrate requirements and process parameters, electrocoating lines achieve balanced outcomes—optimizing adhesion, appearance, and durability while minimizing resource expenditure.
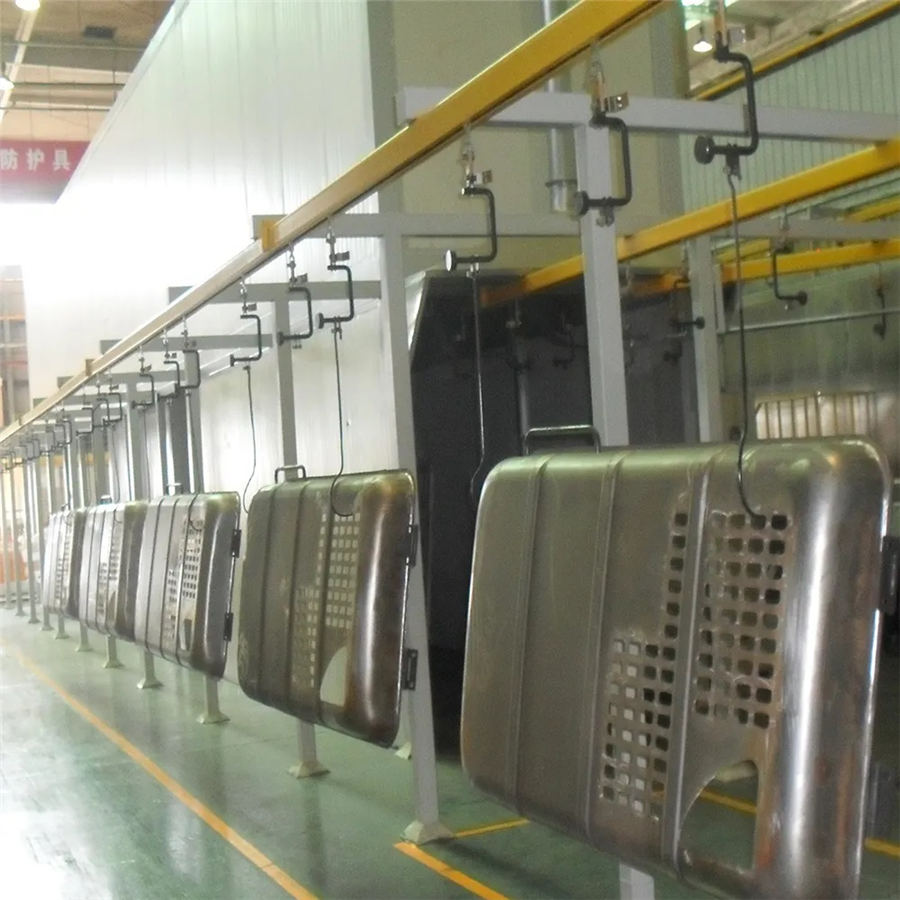
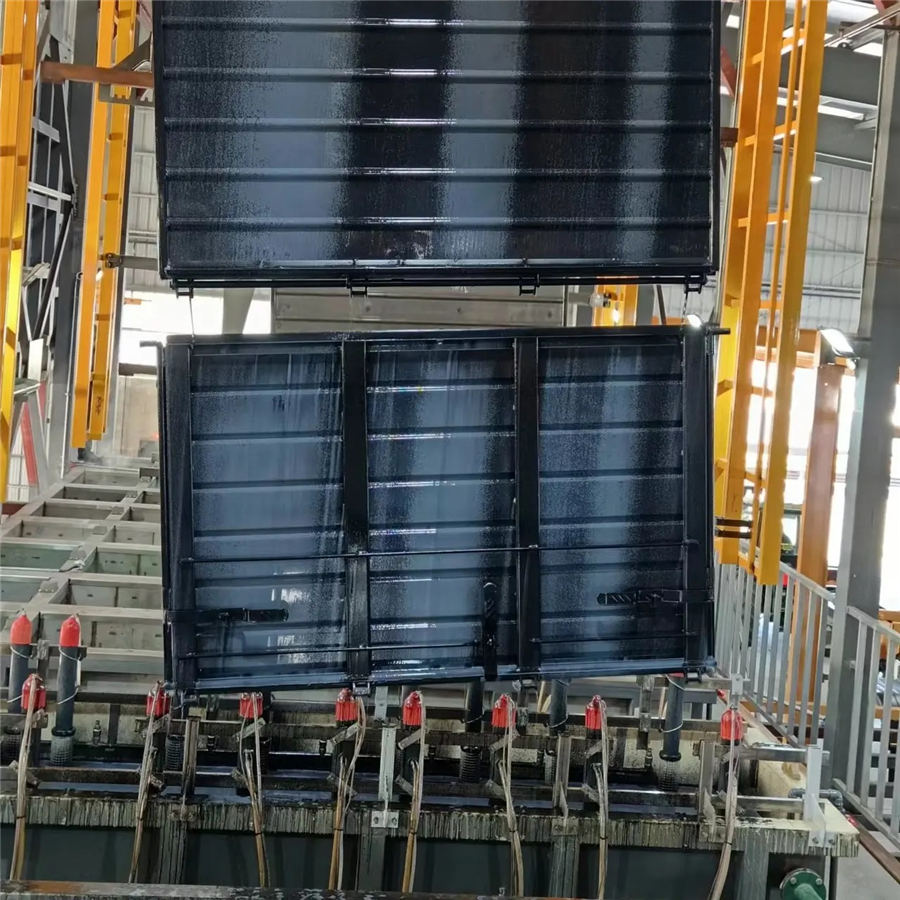
IV. Optimal Conductivity Ranges for Electrocoating Lines
Achieving precise conductivity control is essential for maximizing electrocoating line performance.
1. Standard Industry Parameters
For most cathodic electrocoating lines, the optimal conductivity range is 1,200 ±300 μS/cm. This bandwidth balances deposition efficiency, film quality, and bath stability:
- Upper Limit (1,500 μS/cm): Prevents excessive film thickness (>35 μm) and defects like orange peel.
- Lower Limit (900 μS/cm): Avoids thin coatings (<15 μm) with poor corrosion resistance.
- Tolerance Threshold: Minor adjustments (±100 μS/cm) are acceptable during routine operations without impacting coating performance.
2. Paint-Specific Adjustments
Conductivity targets vary based on resin chemistry. For example, some sensitive formulations (e.g., high-edge-corrosion resistance paints), then tighter control (±30 μS/cm) is required to maintain film integrity.