Let’s talk about a problem that keeps coating engineers up at night: orange peel. You know that frustrating moment when a freshly coated surface dries, only to look like the skin of an orange? It’s not just a cosmetic issue—it’s a red flag for quality.
Electrophoretic coating (or e-coating) is like magic for metal protection. It uses electrical currents to “pull” paint evenly onto surfaces, from car frames to delicate electronics. But even magic has its hiccups. When orange peel creeps in—those wavy bumps and valleys on what should be a smooth finish—it’s more than an eyesore. It hints at deeper issues: maybe the paint didn’t flow right, the curing went sideways, or the equipment threw a tantrum.
Think of it like a bad haircut. You wanted sleek and professional, but ended up with uneven chaos. For industries where looks and performance matter—think luxury cars or high-end appliances—orange peel isn’t just annoying. It’s costly.
But here’s the good news: understanding this sneaky defect is the first step to banishing it. Let’s dig into why it happens, how to spot it, and—most importantly—how to keep your coatings smooth as glass.
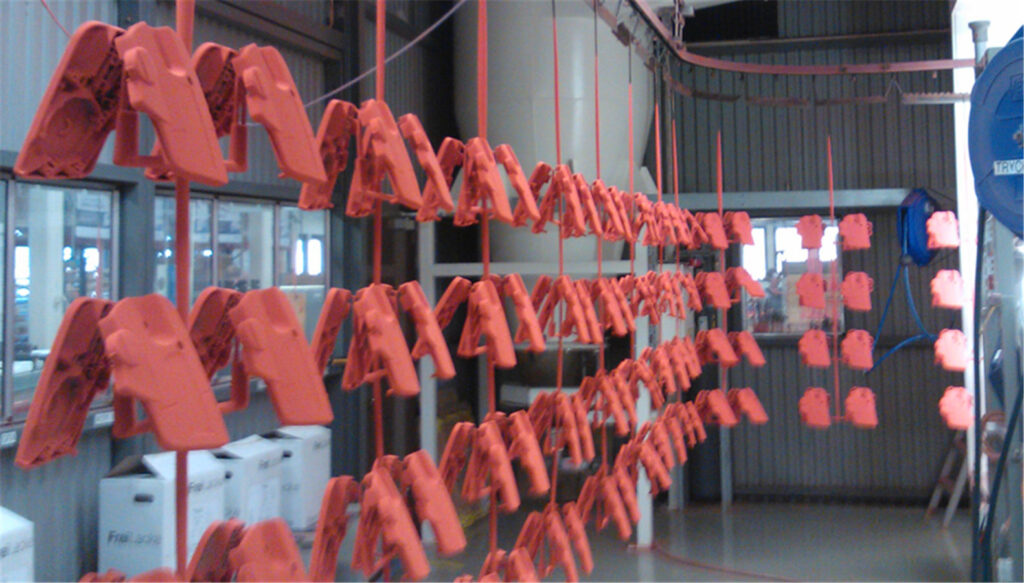
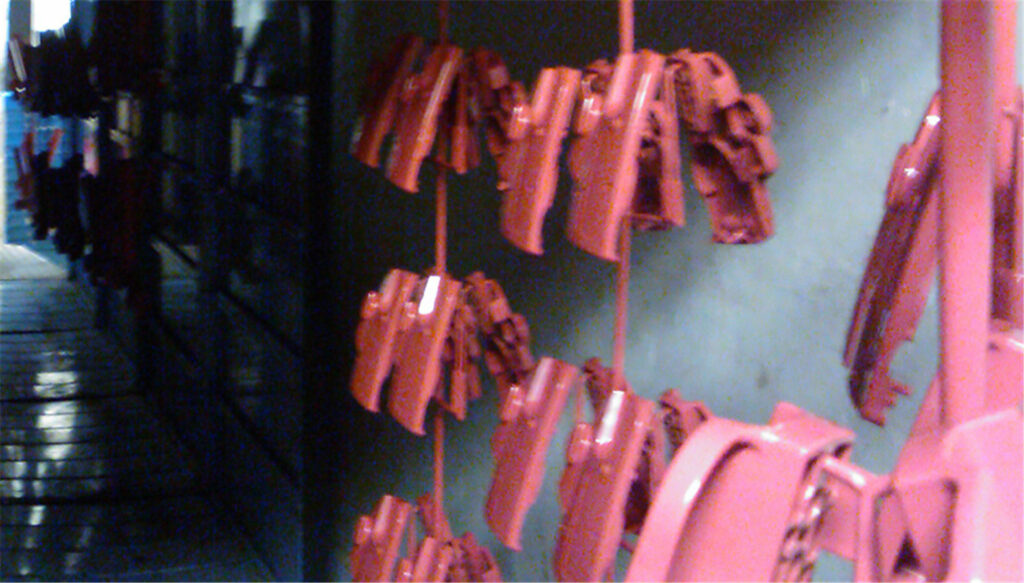
Key Causes of Orange Peel in Electrophoretic Coating Systems
Let’s get real: orange peel is like a bad recipe—too many ingredients gone wrong. Here’s how things unravel:
1. Equipment Acting Up
- Voltage mood swings: Like a flickering lightbulb, unstable voltage messes with how paint sticks to the surface.
- Bath temperature tantrums: Too hot? Paint dries too fast. Too cold? It’s like trying to spread cold butter—uneven and clumpy.
- Nozzle drama: Clogged or misaligned nozzles spray paint like a garden hose with a kink. Not pretty.
2. Material Mayhem
Picture this: Your paint is either too thick, like molasses, or too runny, like watery soup. Neither flows right. Then there’s the resin and pigment playing tug-of-war—if their ratio’s off, the coating can’t decide whether to settle smoothly or clump up. Besides, don’t forget the invisible troublemakers: tiny contaminants like dust or oil sneaking into the bath, throwing a gritty rave on your once-pristine surface.
3. Process Pitfalls
Imagine baking a cake but guessing the oven time. Undercure the coating, and it stays soft and wrinkly. Overdo it, and it cracks under pressure. Then there’s the “I’ll skip prep work” mindset: rough or dirty surfaces make the paint cling unevenly, like tape on a dusty floor. And thickness? If your coating’s thicker in some spots and thinner in others, it dries at different speeds, shrinking into those telltale bumps and valleys.
Bottom line, orange peel is a team sport for defects. Fix one weak link, and the whole game changes.
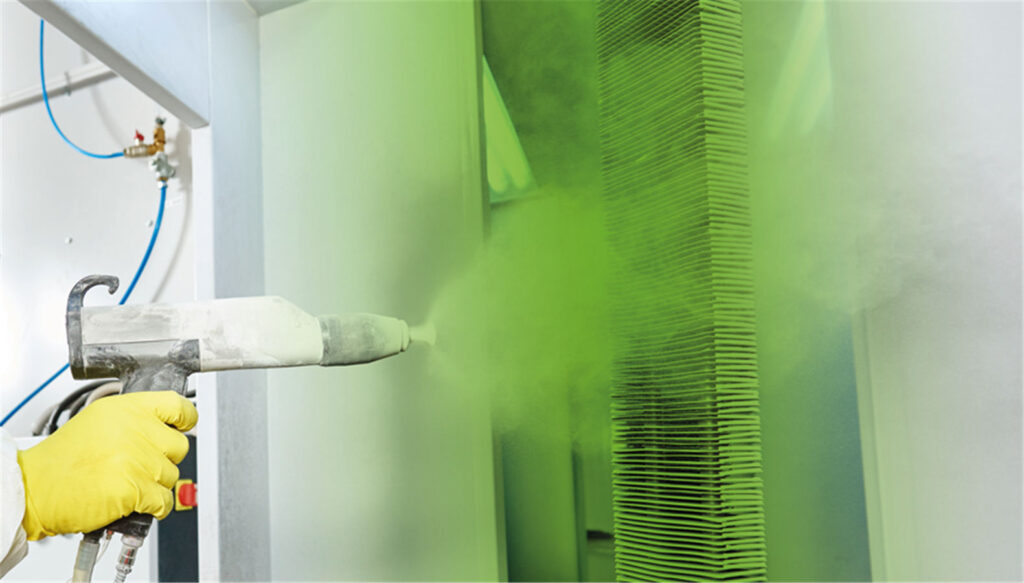
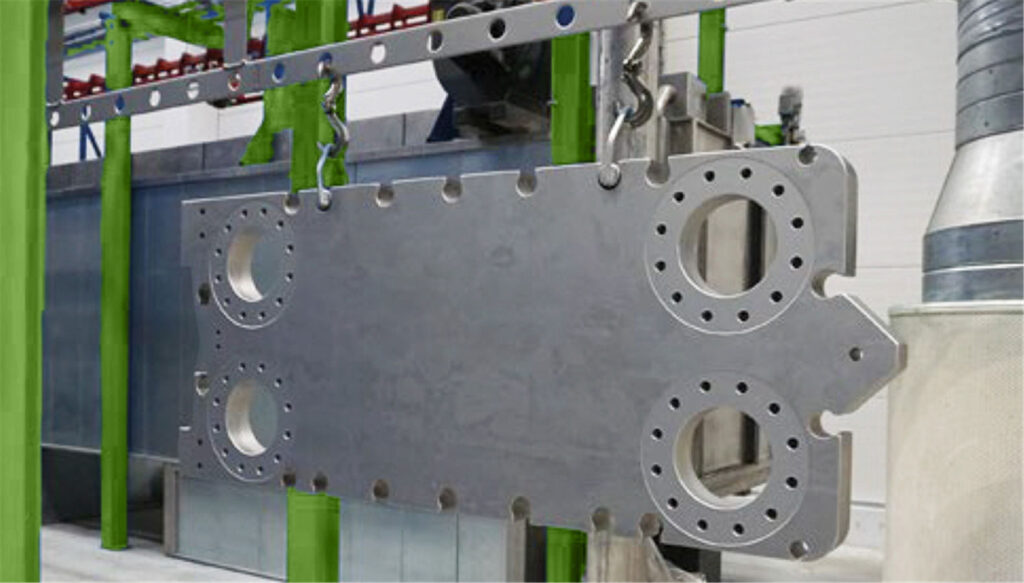
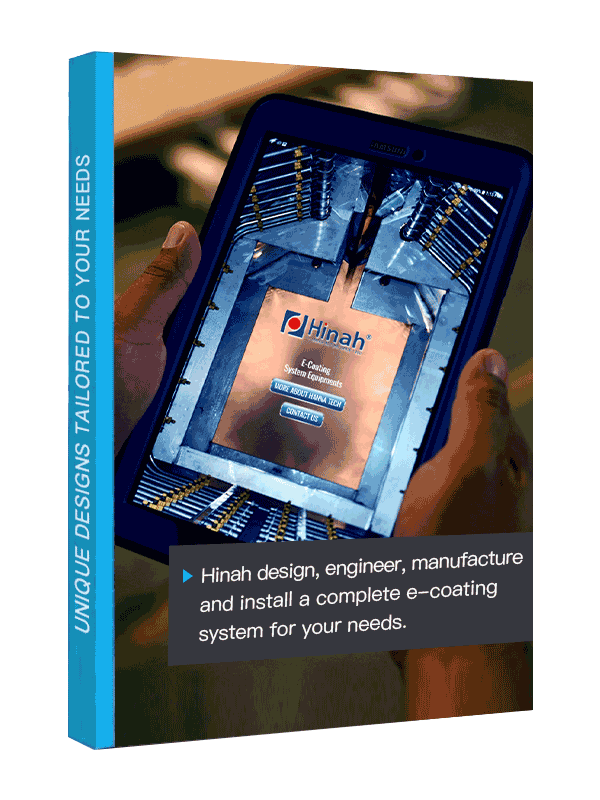
Let's Have A Chat
Get An E-coating Line Planning !
Match Your Products, Get The Solution & Price..
Detecting Orange Peel in Electrophoretic Coating Layers
Finding orange peel isn’t rocket science—but it does require a mix of sharp eyes and smart tools. Let’s break down how to catch this sneaky defect before it ruins your perfect finish:
- The Eye Test
Start with the obvious: look closely. Under bright light, orange peel shows up as a dimpled texture—like a golf ball’s surface. But don’t rely on gut feelings. Standards like ISO 4628 or ASTM D523 give you a cheat sheet for grading severity. Think of it as a “defect Richter scale” for electrophoretic coatings.
- Gloss Meters: The Coating’s Report Card
Shine a light at 60° or 20°, and a gloss meter spits out a number. Smooth coatings score high (like a polished mirror), while orange peel drags the number down. Pro tip: Use both angles. A 20° gloss measurement is like putting the coating under a microscope—it catches subtle texture changes your eyes might miss.
- Surface Profilometry: The Truth Serum
This gadget doesn’t mess around. It maps the coating’s peaks and valleys in microns, turning vague “bumpiness” into hard data. Imagine tracing your finger over sandpaper vs. glass—profilometry quantifies that difference. Bonus: It helps pinpoint if the defect comes from the substrate, the coating itself, or curing issues.
- Cross-Section Autopsy
Sometimes you need to play detective. Slice a sample vertically, pop it under a microscope, and you’ll see the coating’s layers like tree rings. Orange peel often leaves clues here: uneven thickness, poor adhesion between layers, or trapped contaminants.
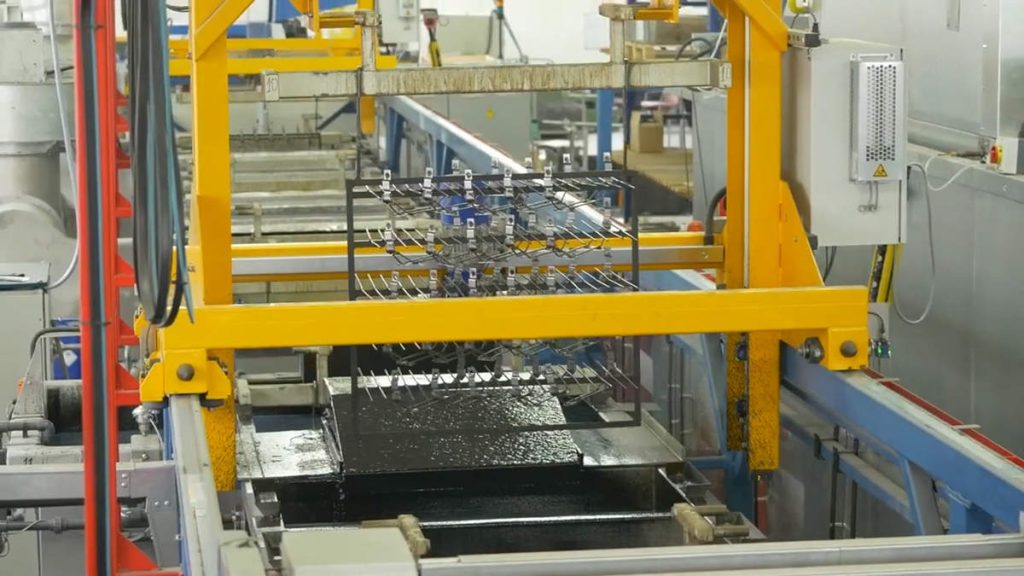
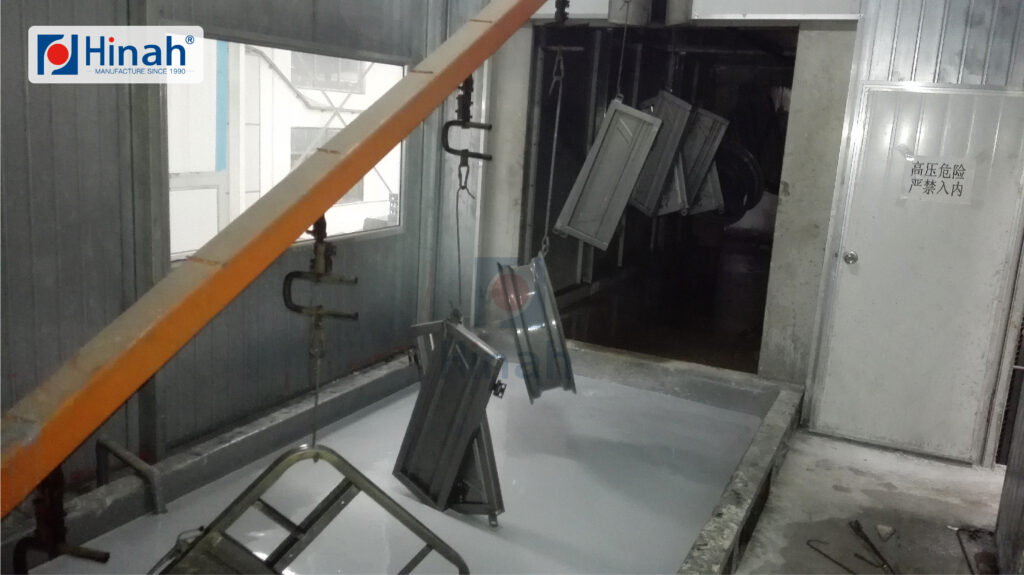
Advanced Solutions for Electrophoretic Coating Orange Peel
Addressing orange peel defects requires a systematic approach that integrates equipment refinement, material advancements, and process optimization. Below are targeted strategies to achieve defect-free electrophoretic coatings:
1. Equipment Optimization Strategies
Voltage instability, a primary contributor to uneven deposition, can be resolved through pulse rectifier technology, which ensures consistent electrical output across the coating bath. Complement this with intelligent temperature regulation systems that maintain bath temperatures within ±1°C of the target range, eliminating thermal-induced viscosity fluctuations. For spray consistency, automated bath circulation and nozzle calibration systems minimize turbulence and ensure uniform paint distribution, even on geometrically complex substrates.
2. Material Science Innovations
Modern formulations leverage nano-level additives to enhance surface leveling by reducing interfacial tension during film formation. Low-viscosity epoxy resins, engineered for optimal flow characteristics, enable seamless coverage while resisting premature curing. To mitigate contamination risks, multi-stage filtration systems with automated particle detection (<5 μm sensitivity) ensure bath purity, preventing particulate-induced texture anomalies.
3. Process Engineering Improvements
Adopt adaptive curing protocols that dynamically adjust oven temperatures and dwell times based on real-time coating thickness data, ensuring complete cross-linking without over-curing. Implement AI-driven predictive maintenance to preempt equipment deviations, such as pump wear or filter degradation, before they impact coating quality. For thickness control, laser-based inline monitoring systems provide micron-level precision, enabling immediate adjustments to voltage or dwell time during deposition.
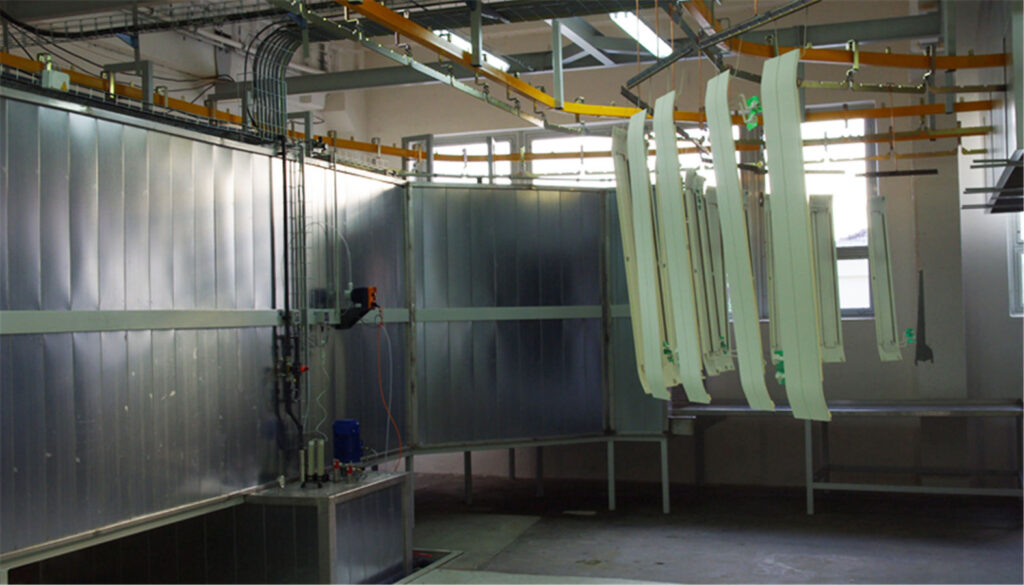
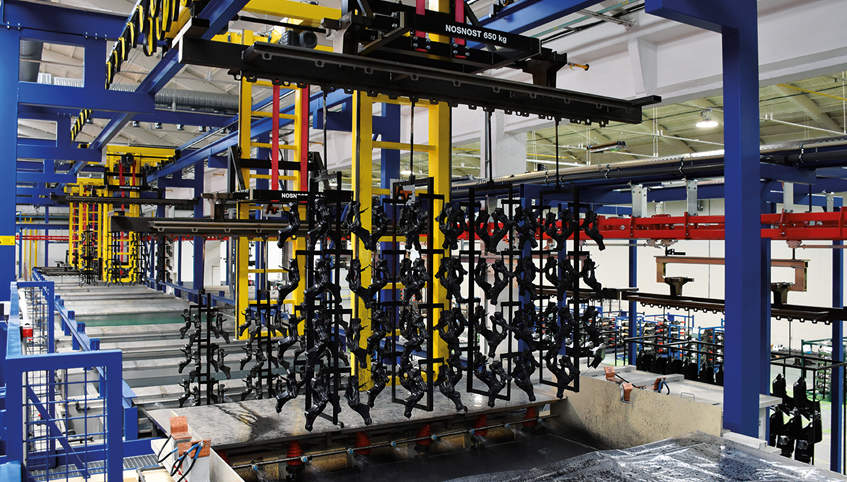
Conclusion
Eliminating orange peel defects in electrophoretic coating is not merely a technical challenge—it’s a strategic imperative for industries demanding precision, aesthetics, and durability. By addressing the interconnected triad of equipment stability, material purity, and process precision, manufacturers can transform inconsistent results into repeatable excellence.
For organizations ready to transcend orange peel challenges, the path forward is clear—proactive optimization today ensures flawless coatings tomorrow.