Did you know your e-coating line might be quietly siphoning profits while you’re busy chasing production targets? Most manufacturers obsess over upfront equipment costs or coating quality (and rightly so), but here’s the kicker: industry studies show 72% of operations overlook recurring hidden expenses that add up faster than overspray on a conveyor belt.
Think about it – that humming, dutiful e-coating line of yours isn’t just dipping parts and applying finishes. It’s making silent financial decisions every minute. A slight voltage hiccup here, a half-degree temperature drift there, and suddenly you’re hemorrhaging thousands monthly without even realizing it. The bitter truth? These stealthy profit killers compound over time, turning what seemed like a competitive edge into a financial anchor.
But here’s the good news: Once you see these leaks, you can’t unsee them. In the next 5 minutes, we’ll pull back the curtain on the three most common (and costly) blind spots haunting modern e-coating lines.
Ready to stop funding your e-coating line’s secret spending habits? Let’s expose what your balance sheet isn’t telling you.
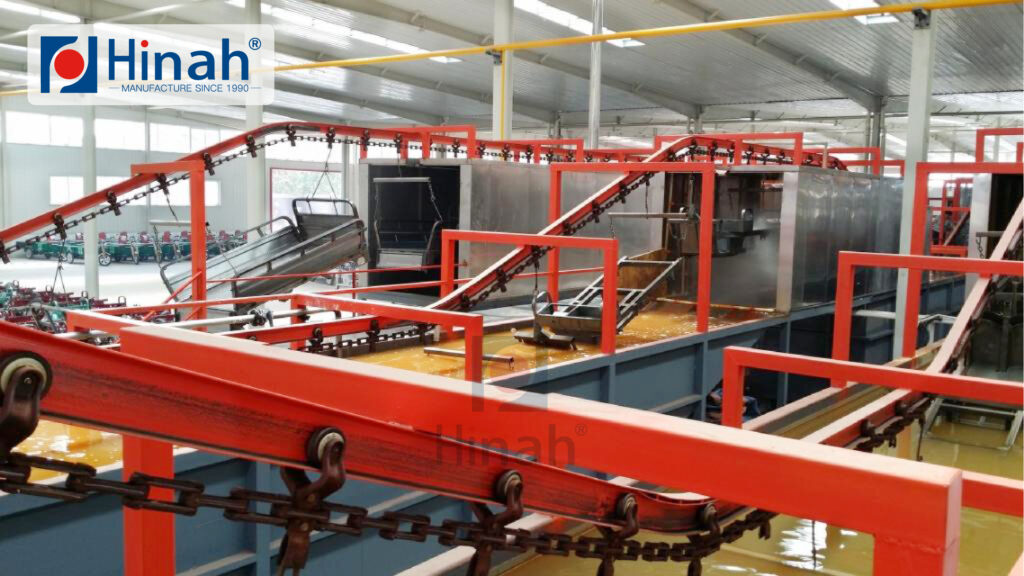
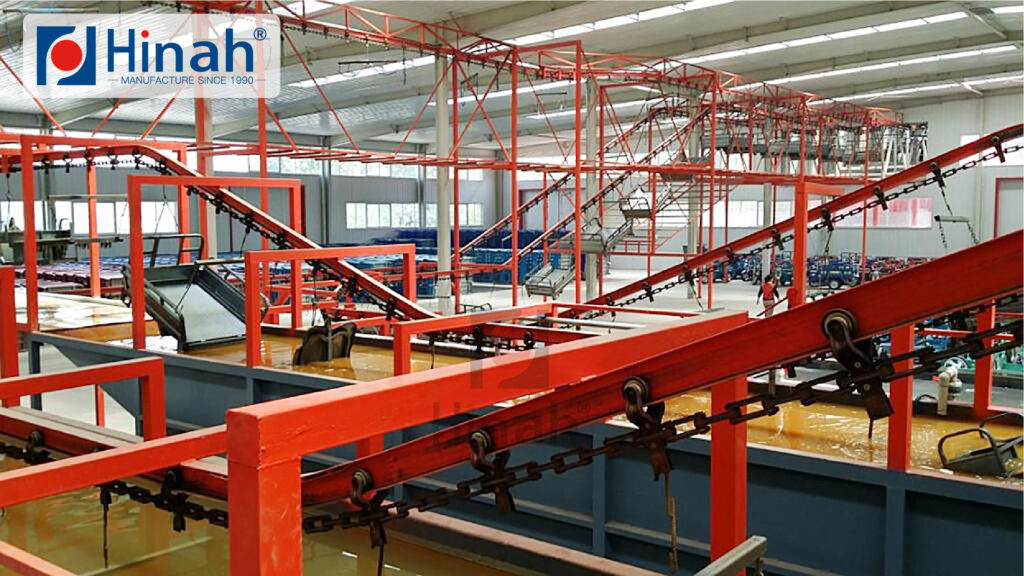
Hidden Cost #1: Energy Inefficiency in Your E-Coating Line
Let’s be honest—energy costs often sneak under the radar until the bills start stacking up. While your e-coating line may seem to be running smoothly, inefficiencies in how it consumes power could be silently draining your profits month after month.
Voltage Optimization Failures
Your rectifiers might be doing their job, but are they doing it efficiently? Many e-coating lines run at higher voltages than necessary, assuming that “more power = better coating.” In reality, this overkill not only wastes electricity but also increases wear on your equipment and can even affect coating quality. Without proper voltage optimization, you’re quite literally paying for power you don’t need.
Pump System Energy Waste
Pumps are the unsung heroes of the e-coating process—constantly circulating fluids, maintaining pressure, and supporting consistent coating. But if your pump system is outdated or improperly sized, it could be guzzling far more energy than required. Think of it as leaving a high-powered fan running in an empty room all day. Over time, that inefficiency adds up to a significant, and completely avoidable, expense.
Tank Temperature Maintenance Costs
Maintaining the correct bath temperature is critical for optimal coating performance, but heating systems can be a hidden energy trap. Poor insulation, aging heaters, or lack of real-time temperature monitoring leads to overcompensation—your system works harder than it should. This isn’t just a maintenance issue; it’s a silent budget killer that most manufacturers don’t notice until the utility bill lands.
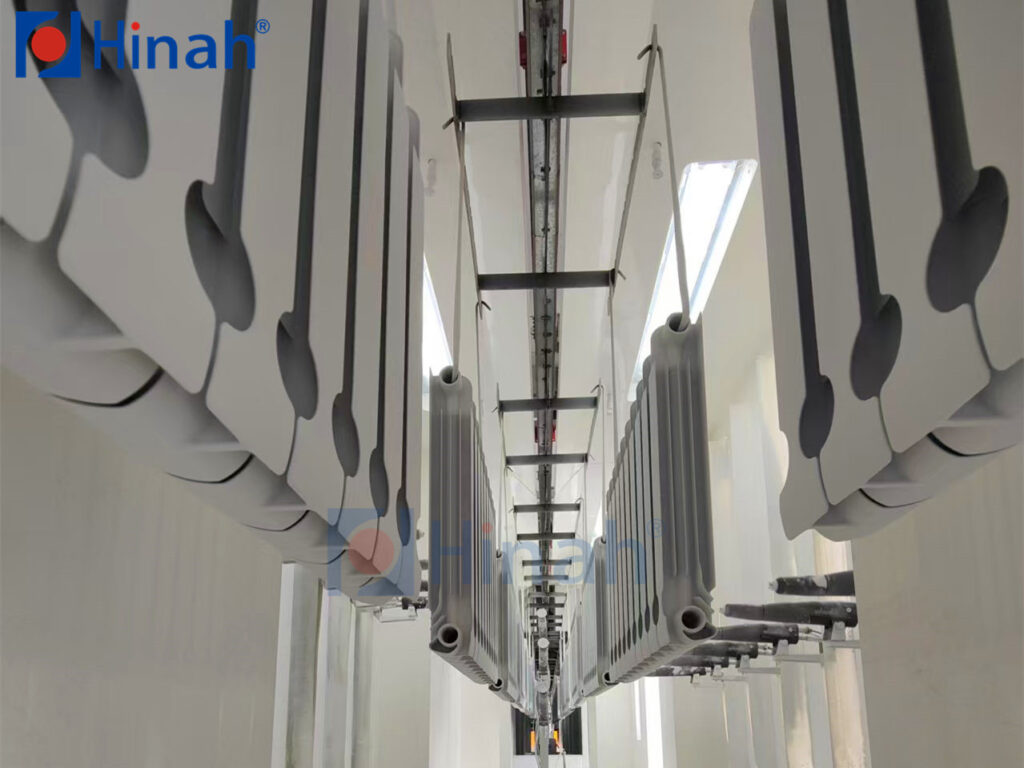
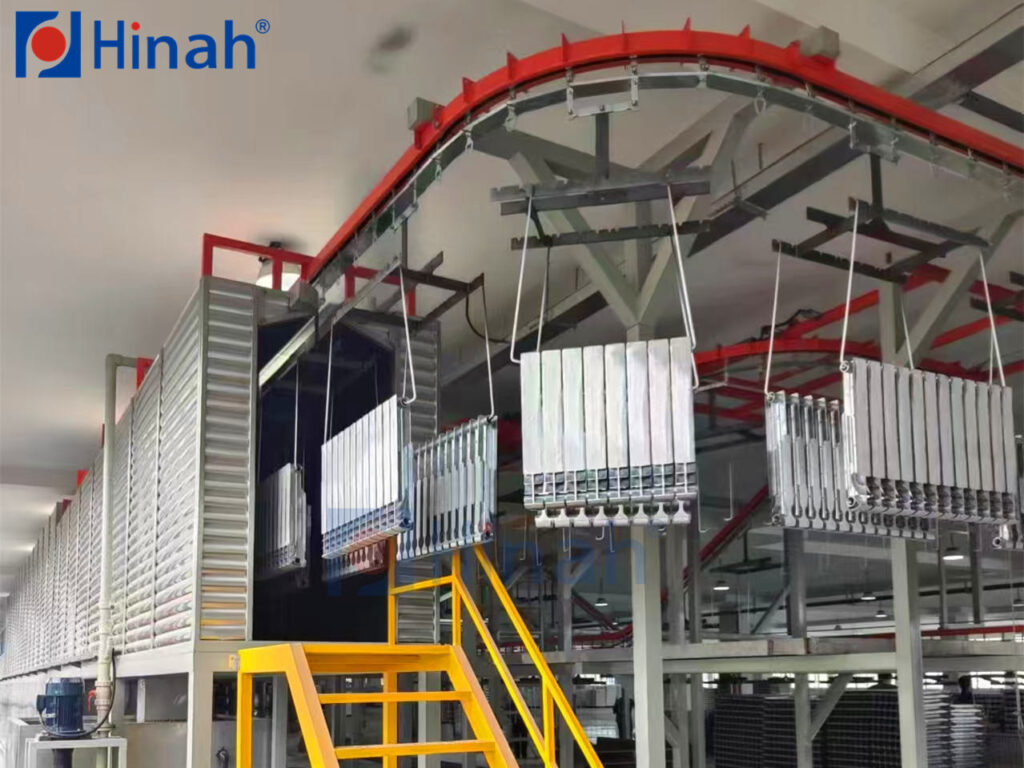
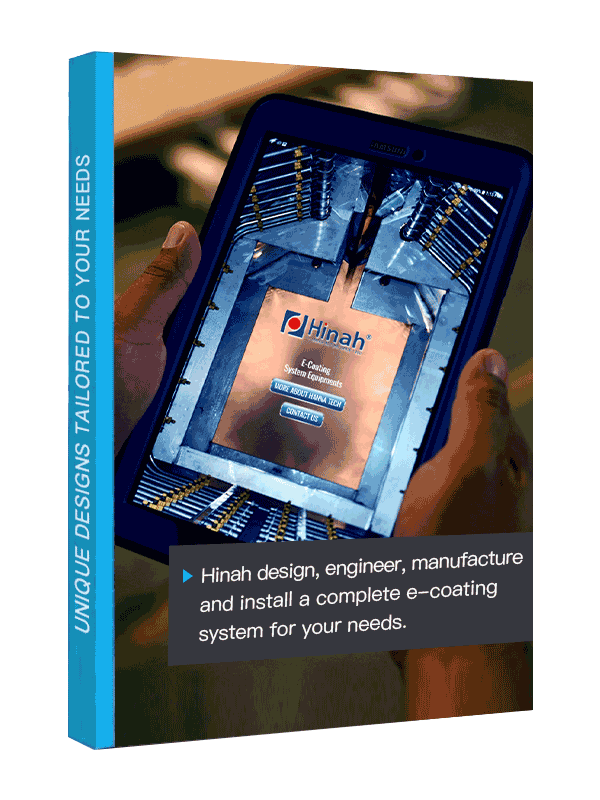
Let's Have A Chat
Get An E-coating Line Planning !
Match Your Products, Get The Solution & Price..
Hidden Cost #2: The Maintenance Iceberg of E-Coating Lines
At first glance, your e-coating line might look like it’s in perfect working order. Everything’s moving, spraying, dipping, curing—just as it should. But beneath that smooth surface lies a ticking clock of wear and tear. This is what we call the “maintenance iceberg”—because the real costs aren’t what you see, it’s what’s hiding underneath.
Take your spray nozzles, for instance. They’re small, often overlooked, but when they clog—production suffers. Maybe it’s a patchy coat, maybe it’s a full stop on the line. Either way, it creates waste, delays, and frustration. And it happens more often than most admit, especially when routine cleaning slips off the radar in busy production schedules.
Then there’s the conveyor system—the workhorse moving every component through your process. Over time, wear patterns develop. Chains stretch, rollers wobble, alignments shift. It doesn’t break overnight, but it gradually drags down your efficiency. And by the time operators report issues, you’re already dealing with a costly slowdown or an unexpected repair.
Let’s not forget the rectifiers. These power-supplying giants are essential, but they’re sensitive to neglect. Without proper cooling, stress monitoring, or performance checks, their lifespan gets cut short—and their failure isn’t something you can just shrug off. It means downtime, replacements, and often an expensive scramble to fix what could have been prevented.
The truth is, maintenance isn’t just about keeping things clean and oiled. It’s about protecting your profit margins. What you don’t see—or delay fixing—can quietly cost you far more than scheduled upkeep ever will.
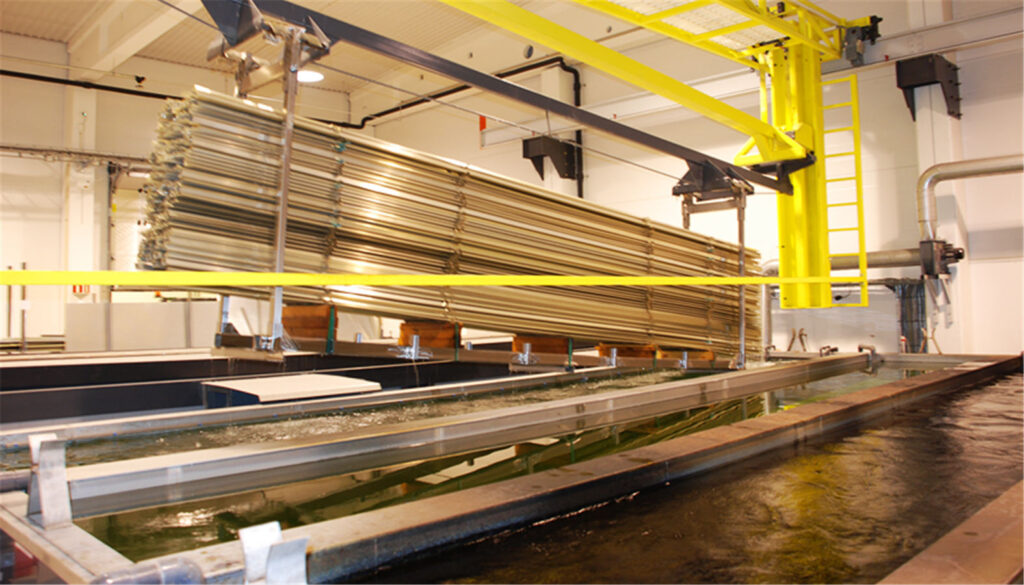
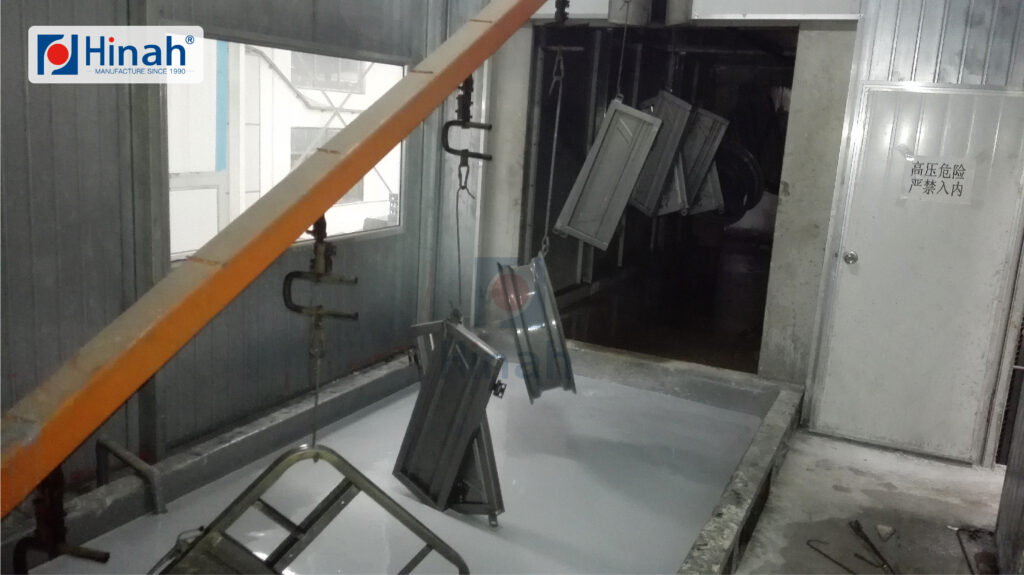
Hidden Cost #3: Material Waste in E-Coating Processes
Waste in e-coating isn’t always obvious. It’s not a dramatic spill on the floor or barrels of paint being dumped. More often, it’s quiet, steady, and invisible—coating materials being lost bit by bit, shift after shift, in ways that go unnoticed until someone digs into the numbers.
One of the biggest culprits? Overspray recovery. While most modern systems are designed to reclaim unused material, many are far from efficient. Poor air flow design, worn filters, or outdated recovery units can mean that valuable coating material ends up in the waste stream instead of back in the tank. It’s a slow leak in your profitability—small percentages that turn into big losses over time.
And what about bath contamination? A single misstep—like poor pre-treatment, inconsistent filtration, or lack of bath monitoring—can lead to contamination that compromises the entire coating process. You end up with reworks, rejected parts, or even the need to dump and refill the bath. That’s not just material waste—it’s labor, time, and money out the door.
Then there’s the rinsing system. If it’s not properly designed or maintained, you might be using more water and chemicals than necessary—or worse, failing to remove enough residue before parts move on. That results in lower coating adhesion, more defects, and higher reject rates. In other words, you’re paying for flawed performance, and the material waste becomes just one layer of a much deeper problem.
Material waste doesn’t always look like waste. Sometimes it looks like “normal production.” But the most efficient e-coating lines are the ones that challenge that assumption—and squeeze value from every drop, every cycle, every part.
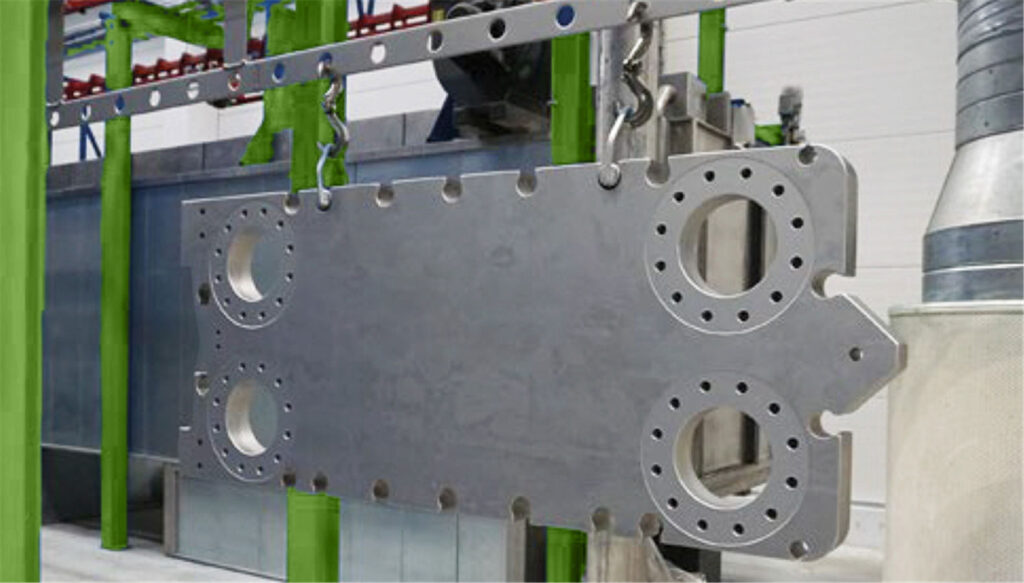
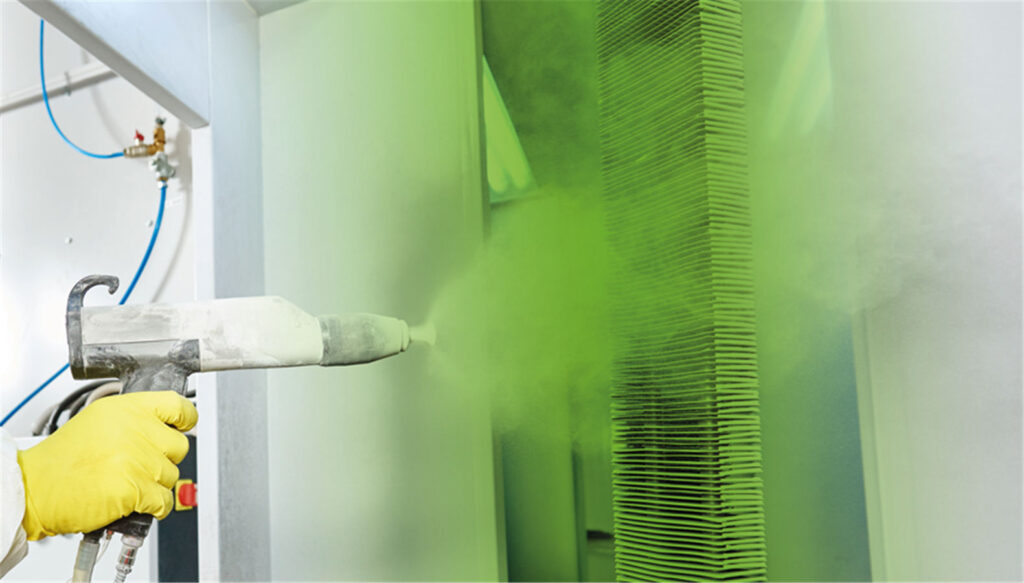
Are You Paying for What You Can’t See?
On paper, your e-coating line may look like a solid investment. But the reality is, what you don’t see often costs more than what you do. Energy inefficiencies, hidden maintenance traps, and subtle material waste—these aren’t just technical details. They’re silent profit drains, quietly reducing your ROI with every passing shift.
The good news? These hidden costs aren’t inevitable. With the right technology, smarter system design, and a proactive mindset, you can identify and eliminate them—before they start eating into your bottom line.
So ask yourself: When was the last time you truly audited your line—not just for output, but for efficiency? Are you still focused only on the upfront cost, or are you ready to see the full picture?
The most successful manufacturers aren’t the ones who spend the least. They’re the ones who understand what every dollar spent actually buys.