Coating uniformity is one of the most critical quality indicators in an electrophoresis coating line, directly impacting corrosion resistance, appearance, and overall product performance. In industries like automotive, appliance, and metal furniture manufacturing, even slight inconsistencies in film thickness can lead to costly rework or product failure.
Achieving a consistent and even coating is not just about controlling one variable — it requires a well-balanced system that integrates surface preparation, electrical settings, chemical stability, and mechanical design. This article explores the key factors that influence coating uniformity and offers practical insights for optimizing each stage of the process.
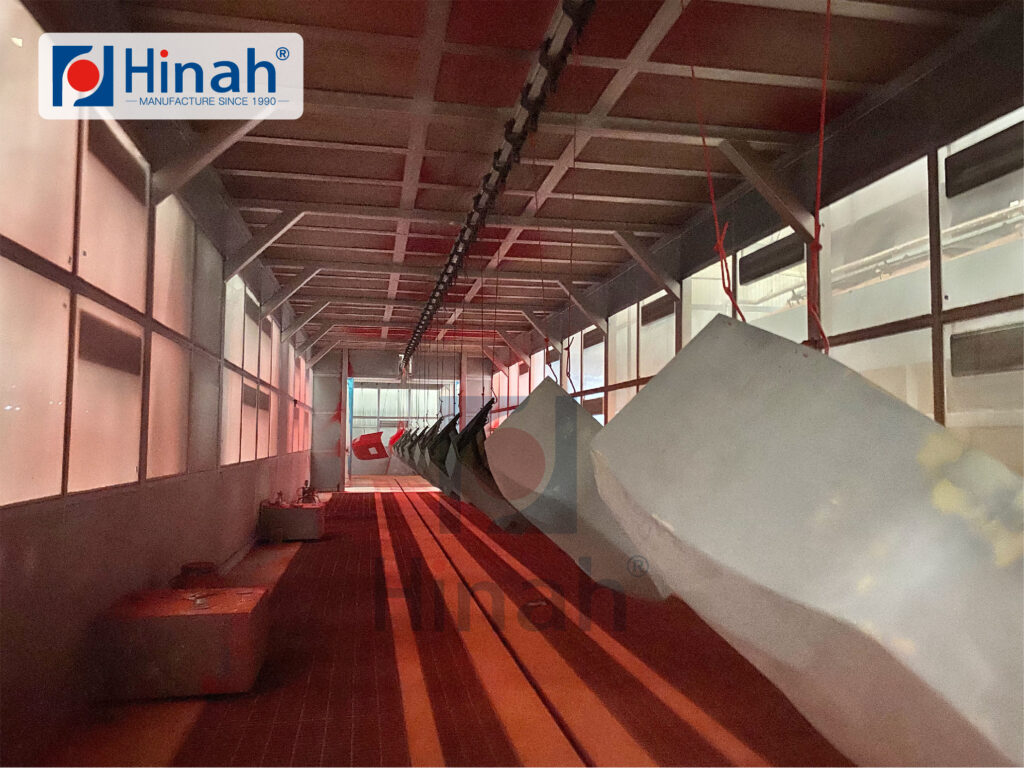
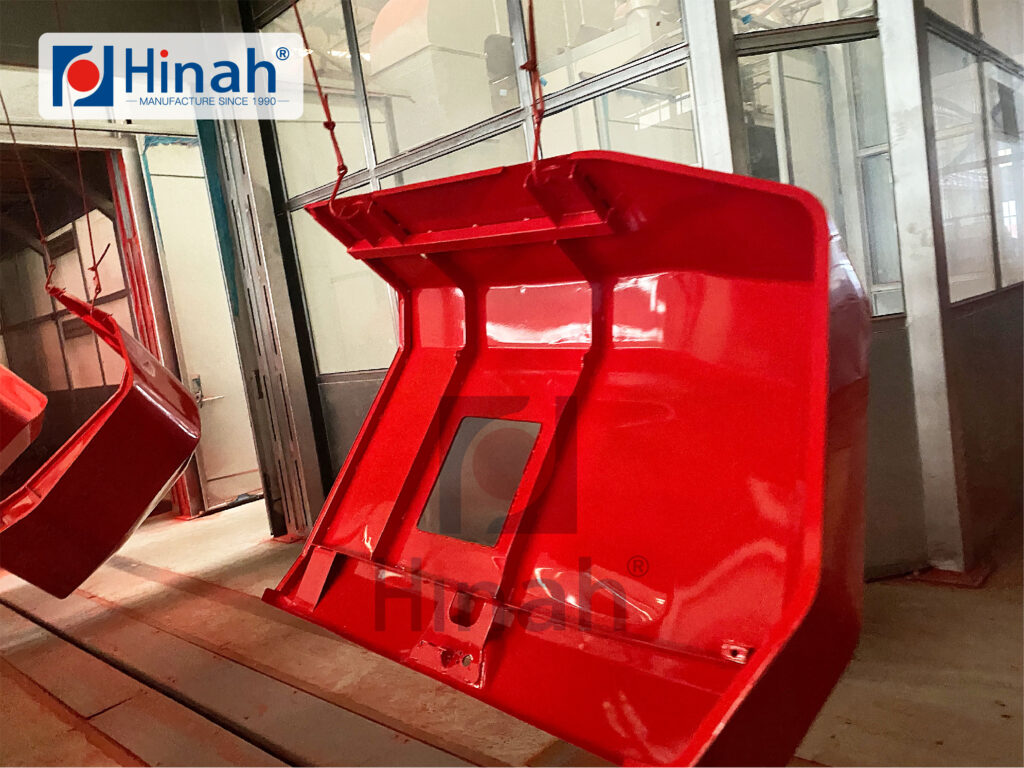
I. Substrate Preparation and Cleanliness
Substrate preparation is not just a preliminary step in electrophoretic coating — it is one of the most critical factors that determine whether the final coating will be uniform, durable, and defect-free. No matter how advanced the coating line or how stable the bath chemistry, poor surface preparation will inevitably lead to coating failure.
In electrophoresis, the coating material is deposited by an electrical charge, which relies on direct contact between the charged particles and the conductive surface of the substrate. Any contamination — such as oil, grease, rust, fingerprints, or welding residue — can block this interaction, creating localized areas with low conductivity. The result is uneven deposition, poor adhesion, or complete coating voids.
A well-designed pretreatment system typically includes multiple stages: degreasing to remove oils and organic contaminants, rinsing to eliminate chemical residues, and phosphating to provide a uniform conversion layer that enhances corrosion resistance and coating adhesion. Each stage must be precisely controlled in terms of chemical concentration, temperature, and dwell time.
Even minor variations in pretreatment quality can cause large inconsistencies in the e-coating layer. For example, under-phosphated areas may lead to thinner coating films, while over-phosphating can cause flaking or poor adhesion. Therefore, regular bath analysis, line maintenance, and proper part loading are essential to ensure full surface activation and optimal coating performance.
In short, substrate preparation is not just important—it is foundational. Without it, achieving coating uniformity in an electrophoresis coating line is virtually impossible.
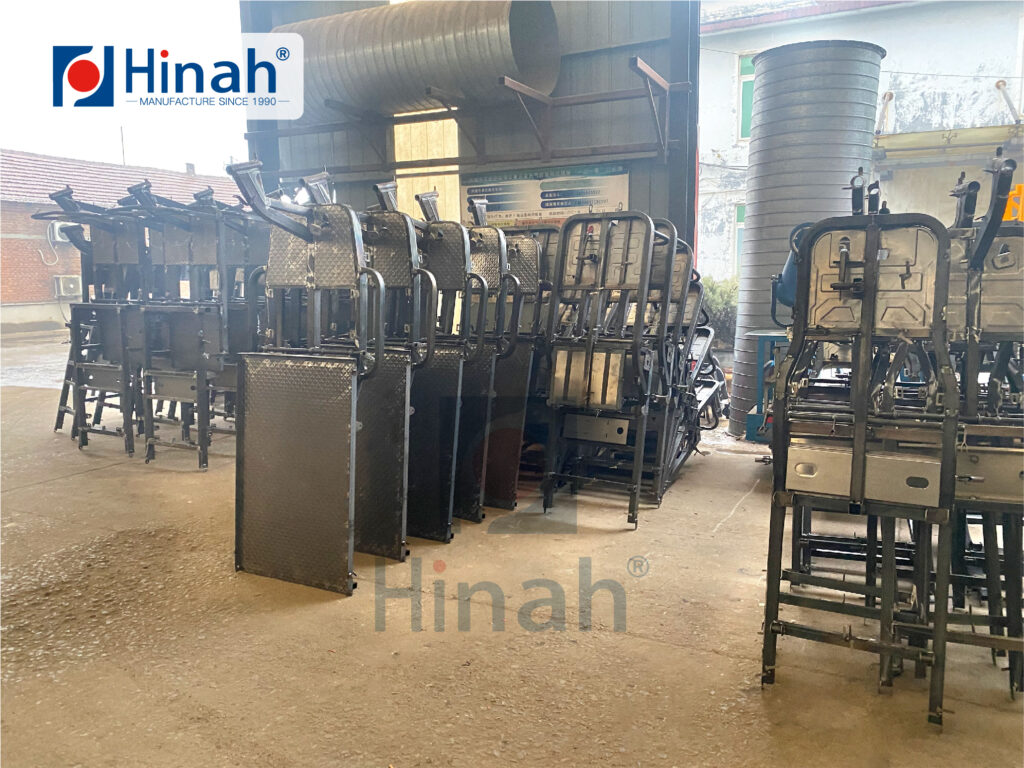
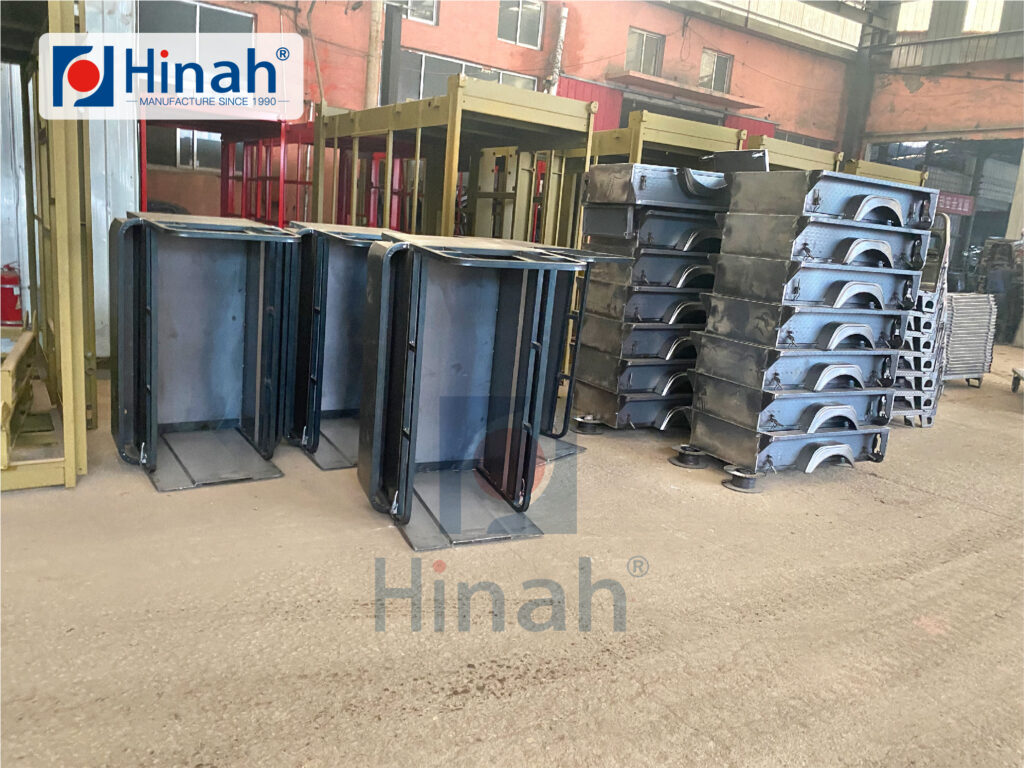
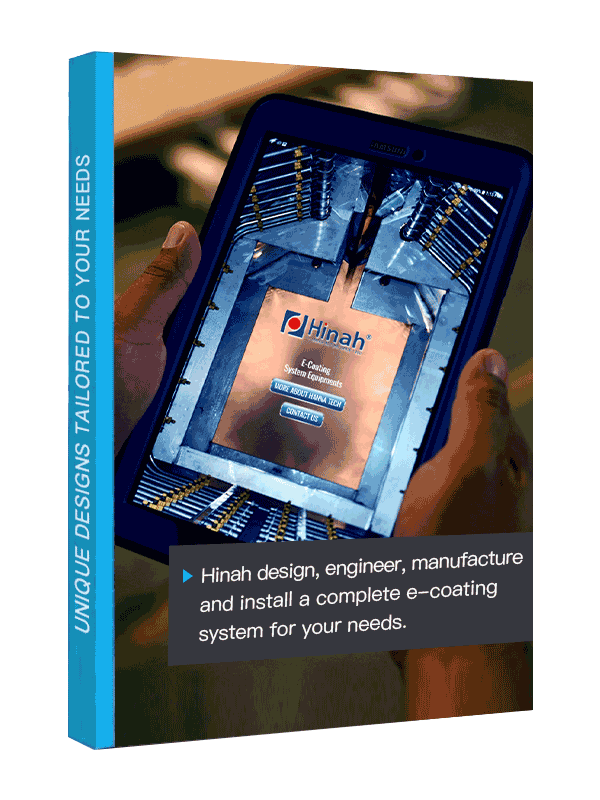
Let's Have A Chat
Get An E-coating Line Planning !
Match Your Products, Get The Solution & Price..
II. Electrical Settings and Part Geometry
Electrical parameters play a central role in determining coating thickness and uniformity in an electrophoresis coating line. The applied voltage and current control the deposition rate—too low, and the coating may be thin or incomplete; too high, and it can lead to overcoating, roughness, or edge buildup. Maintaining the right electrical settings for different part types is essential to achieve a consistent film.
In addition, part geometry significantly affects current distribution. Sharp edges, deep recesses, and complex shapes can cause uneven electrical fields, resulting in irregular coating thickness. Proper racking and orientation can help minimize these effects by ensuring uniform exposure and reducing shadowed areas. Adjusting voltage ramps and dwell times for complex parts is also an effective strategy for improving uniformity.
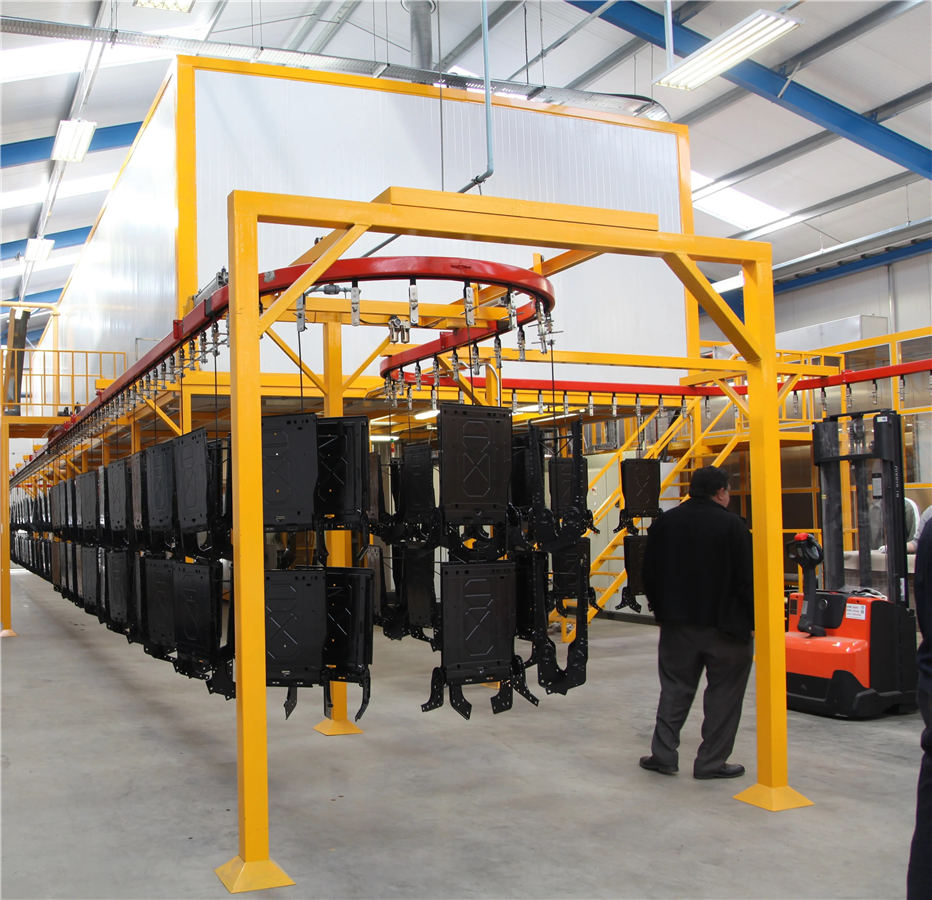
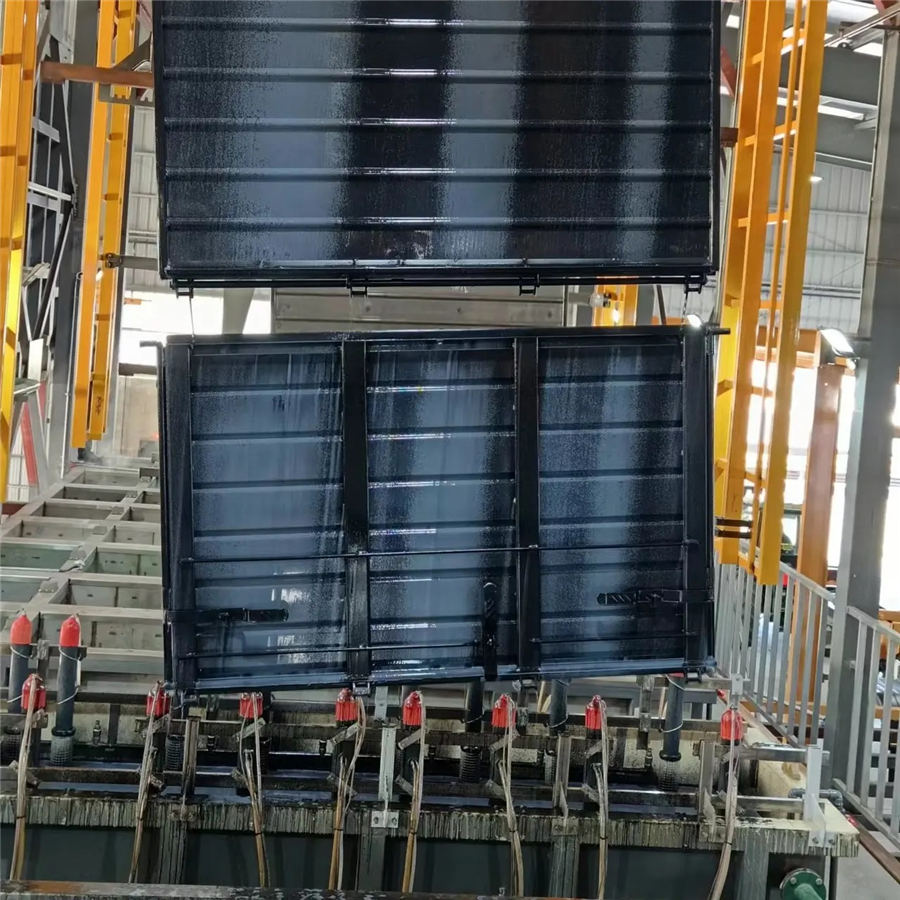
III. Bath Composition and Process Parameters
The chemical stability of the electrophoresis bath plays a critical role in coating uniformity. Key parameters—such as pH, bath temperature, resin solids content, and conductivity—must be continuously monitored and tightly controlled. Even minor deviations can cause issues like uneven film thickness, streaks, or defects around edges and recessed areas.
In addition to chemical balance, the physical design and maintenance of the e-coating tank itself are equally important. Proper tank circulation ensures that the bath composition remains homogeneous throughout the entire volume. Poor circulation or dead zones can result in localized inconsistencies in coating quality. Installing overflow systems, well-positioned inlet/outlet points, and agitation mechanisms helps maintain fluid movement and temperature balance.
Filtration is another essential component of bath management. A clogged or underperforming filtration system can allow contaminants or coagulated particles to remain in the tank, leading to surface defects. Regular cleaning and maintenance of ultrafiltration units and anode cells help remove impurities and maintain bath stability over time.
By maintaining a stable, clean, and well-agitated bath environment, manufacturers can ensure uniform coating across all parts, even in high-throughput or multi-shift operations.
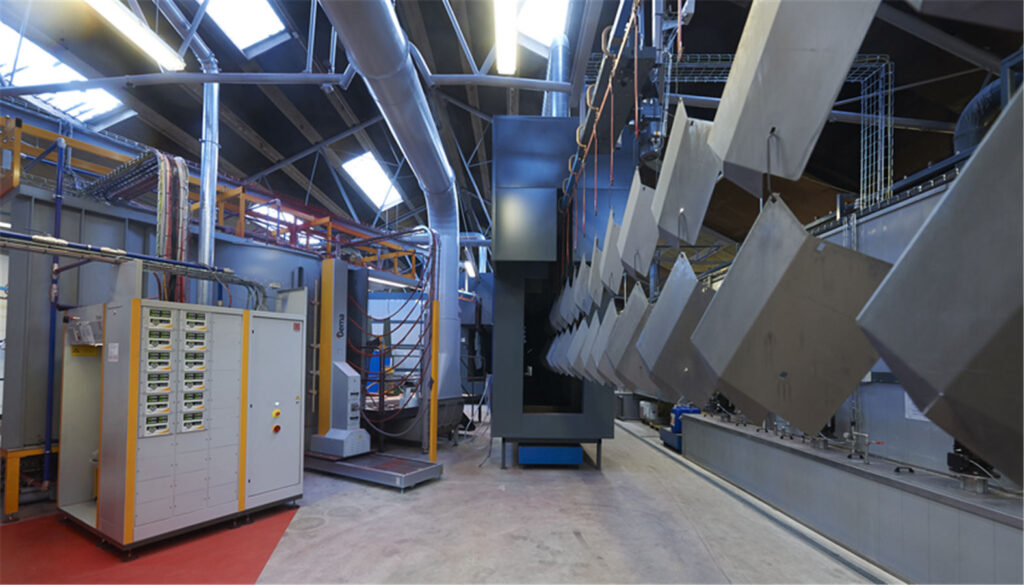
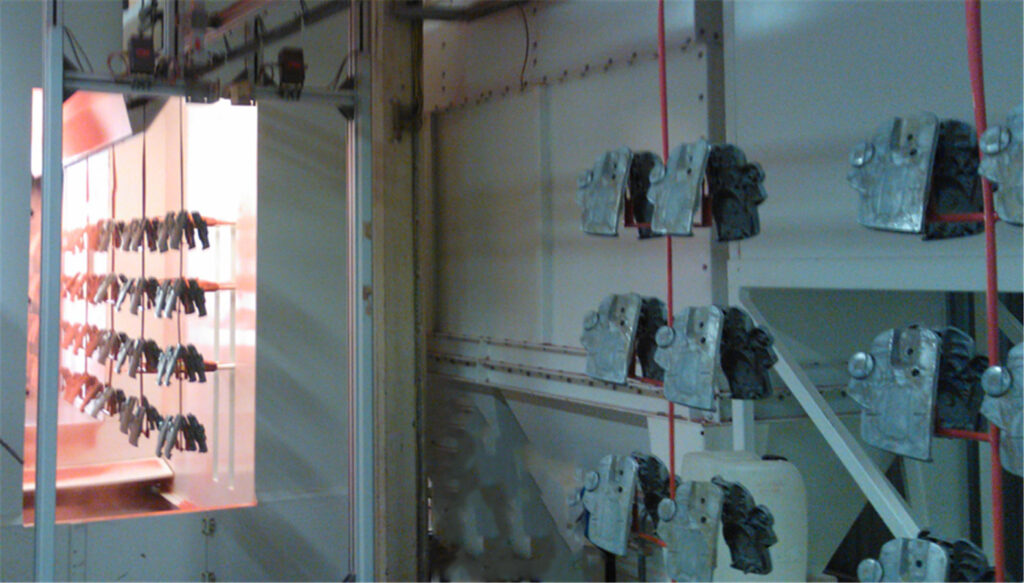
IV. Racking Method and Line Speed
How parts are racked and moved through the electrophoresis line significantly affects coating uniformity. Improper racking can lead to inconsistent electrical contact, uneven current distribution, and shadowing—especially on complex or densely arranged parts. Good racking practices ensure stable contact points, uniform spacing, and proper orientation to maximize exposure to both electrical fields and bath circulation.
Line speed and dwell time also play a key role. If parts move too quickly through the bath, there may be insufficient deposition time, resulting in a thinner film. Conversely, excessive dwell time can cause overcoating or rough finishes. Synchronizing the conveyor speed with part geometry and coating requirements is essential for process stability.
Optimizing both racking configuration and line speed helps ensure that every surface—flat or recessed—receives a consistent, high-quality coating. Regular inspection of racks for damage or contamination and adjusting part spacing for airflow and drainage are also important steps in maintaining coating uniformity across production runs.
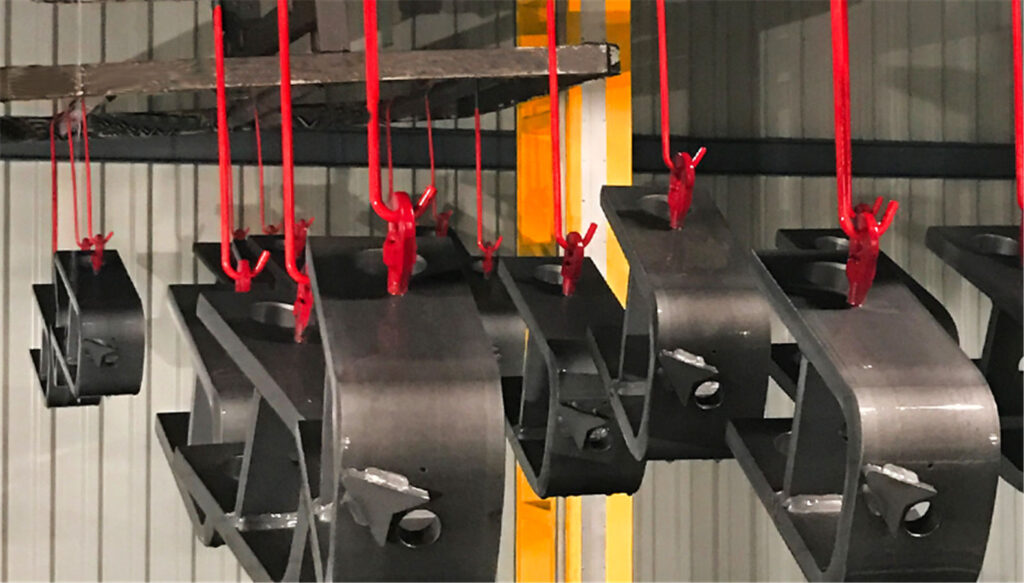
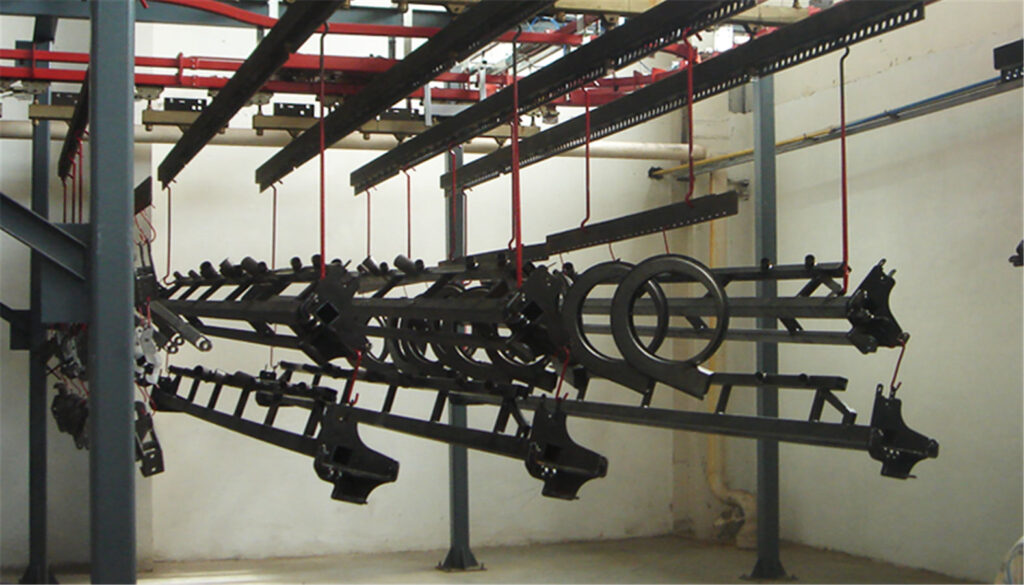
Conclusion
Ensuring coating uniformity in an electrophoresis coating line is essential for producing high-quality, durable finishes. By optimizing substrate preparation, electrical settings, bath composition, and racking methods, manufacturers can achieve consistent film thickness and superior corrosion resistance. Proper control of these factors helps maintain the efficiency and reliability of the electrophoresis coating line, meeting the strict standards required in automotive, appliance, and industrial applications.