Electrocoating (e-coating) is a foundational process for achieving superior corrosion protection and uniform finish adhesion on metal substrates across automotive, appliance, and industrial applications. However, the long-term durability and performance of the e-coat film are intrinsically dependent on the quality of the surface preparation before the coating is applied. This makes the pretreatment stages within an e coat line not merely preparatory steps, but the decisive factor in ensuring optimal coating adhesion and overall product integrity.
Adhesion failures – manifesting as blistering, peeling, or under-film corrosion – often trace their root cause back to inadequacies in the e-coat line’s pretreatment sequence. Contaminants like oils, rust, or poorly formed conversion coatings create weak interfaces where the e-coat cannot bond effectively to the metal. Consequently, optimizing each stage of the pretreatment process is not an option; it is an essential engineering requirement for maximizing the adhesion performance and reliability of the entire e-coat line.
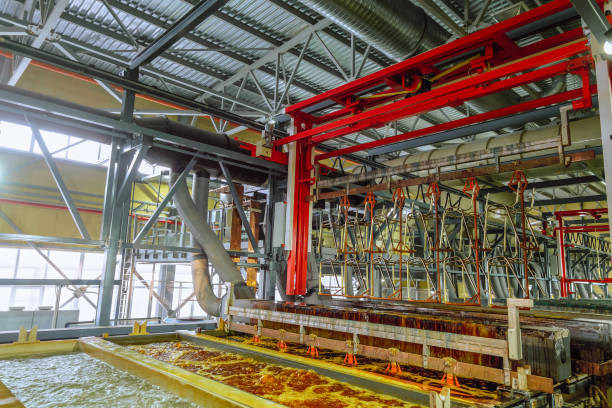
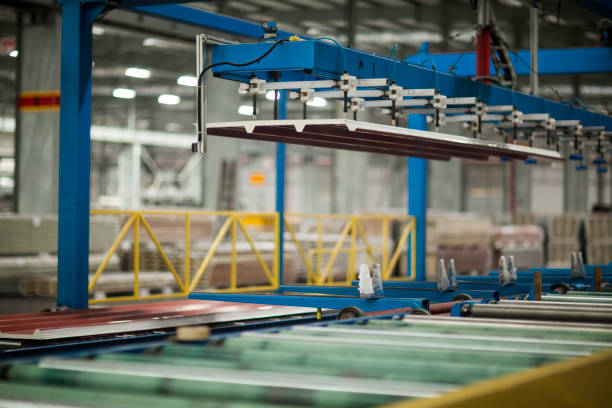
Anatomy of an E Coat Line Pretreatment Process: Stages Explained
The pretreatment sequence is the vital preparatory backbone of any e-coat line, meticulously designed to transform the raw metal surface into an ideal substrate for optimal e-coat adhesion and performance. This multi-stage process, typically integrated seamlessly within the e-coat line’s material handling path, involves precise chemical and physical interactions. Understanding each stage is fundamental to effective optimization. Here’s a breakdown of the core stages:
Stage 1: Cleaning – Removing Oils, Grease, and Soils
The initial and critical step to remove bulk oils, greases, lubricants, drawing compounds, metal fines, and particulate soils from the substrate surface. Any residue compromises subsequent stages and adhesion.
Stage 2: Rinsing – Ensuring Contaminant Removal
To thoroughly rinse away loosened soils and residual cleaning chemicals from Stage 1. Inadequate rinsing leads to chemical contamination carryover, poisoning subsequent stages and causing adhesion defects.
Stage 3: Surface Conversion – Creating the Adhesive Base
The cornerstone of adhesion. This stage chemically reacts with the cleaned metal surface to create a microcrystalline or amorphous layer. This layer significantly increases surface area, provides mechanical keying sites, and offers a chemically receptive surface for the e-coat to bond with covalently.
Stage 4: Final Rinsing – Purity Before E-Coat
To remove any traces of conversion coating bath chemicals or reaction by-products and ensure an ultra-clean, ionic contaminant-free surface immediately before the e-coat tank. Dissolved salts or minerals can cause craters, poor wetting, or adhesion loss in the e-coat.
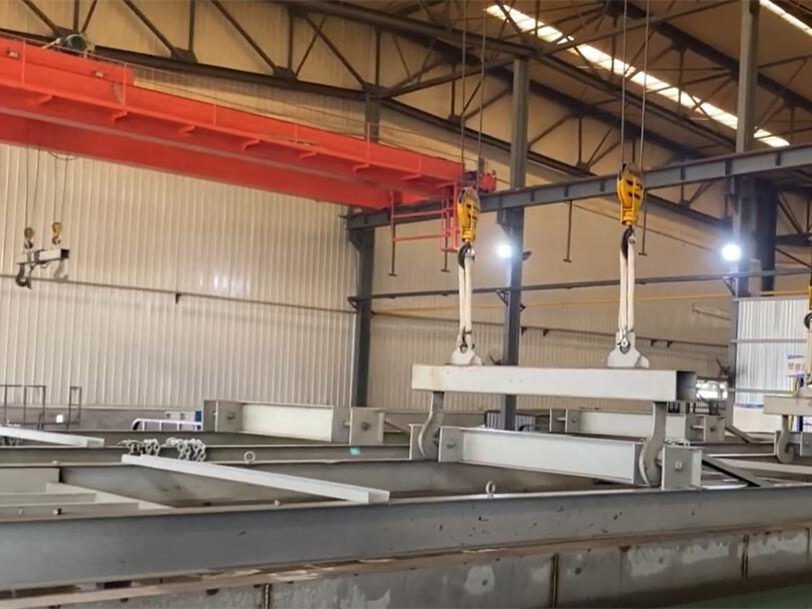
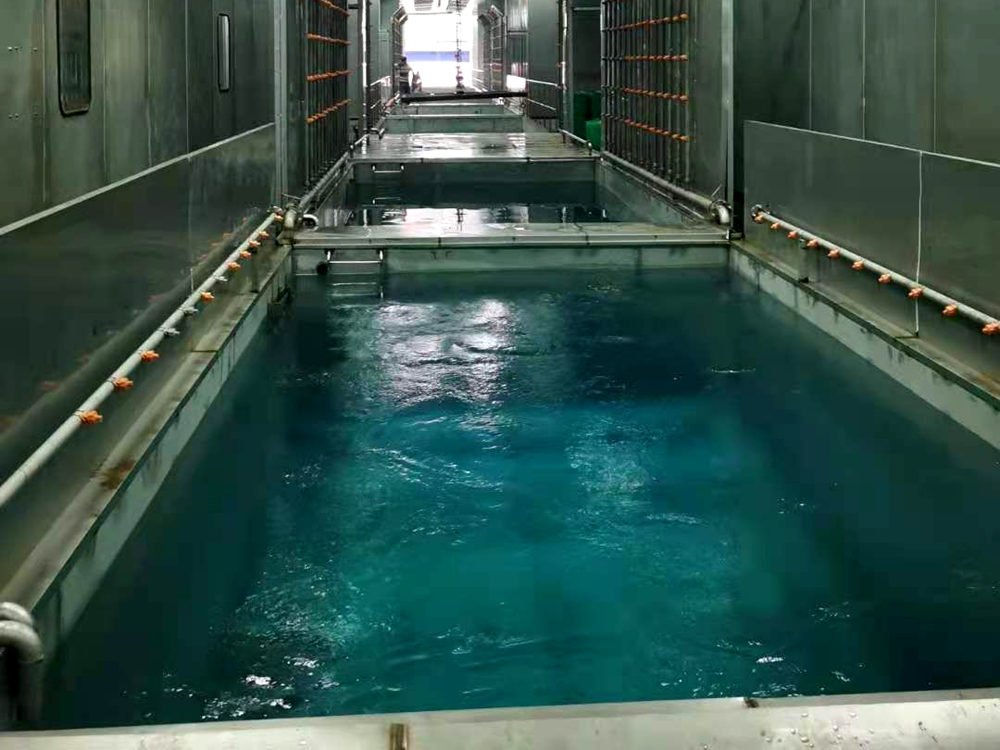
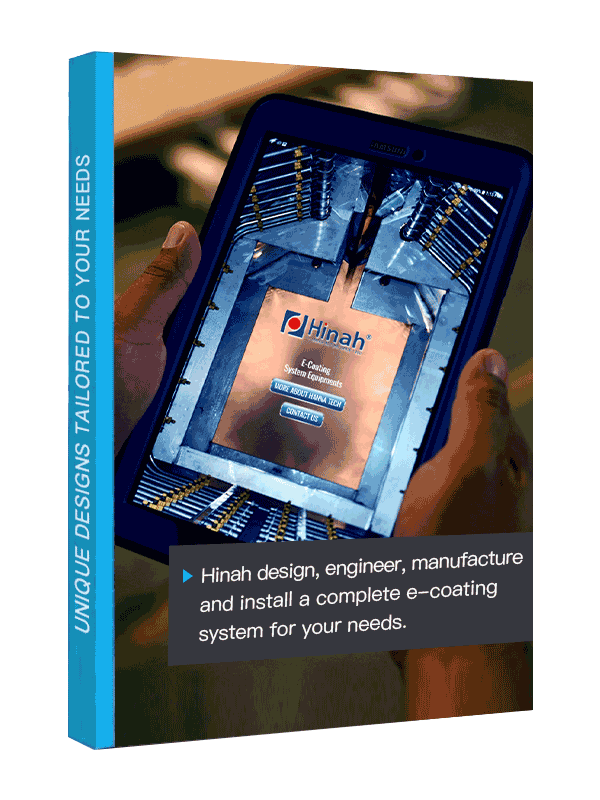
Let's Have A Chat
Get An E-coating Line Planning !
Match Your Products, Get The Solution & Price..
Common Adhesion Failure Points Related to Pretreatment in E Coat Line
Adhesion failures in electrocoating often originate from specific shortcomings within the pretreatment stages of the e coat line. Identifying these root causes is crucial for effective remediation. Here are the key failure points and their primary causes:
- Inadequate Cleaning: Residual Oils/Grease Under the Coating
Insufficient removal of contaminants due to low cleaner concentration, temperature, spray pressure/coverage, short dwell time, or contaminated bath.
- Poor Rinse Water Quality or Contamination Carryover
Ineffective rinsing leading to chemical or soil carryover into subsequent stages, caused by insufficient rinse volume/force, short dwell time, lack of counter-flow, or high contaminant load in rinse tanks.
- Issues with Conversion Coating
Problems like incomplete coverage (low concentration, temp, time), poor crystal structure (imbalanced chemistry, contamination), or bath contamination (carryover, sludge), directly undermining the adhesion foundation.
- Drying Problems After Final Rinse
Ineffective drying post-final rinse due to insufficient oven temperature/time, poor airflow, water entrapment in part geometry, or condensation from line stoppages.
- Line Speed and Immersion Time Mismatches in the E-Coat Line Pretreatment Section
Overall e coat line speed exceeding the designed capability of pretreatment tanks/zones, critically reducing dwell times for cleaning, rinsing, conversion, and final rinsing.
Addressing these specific pretreatment root causes is essential for resolving adhesion failures in the e-coat line.
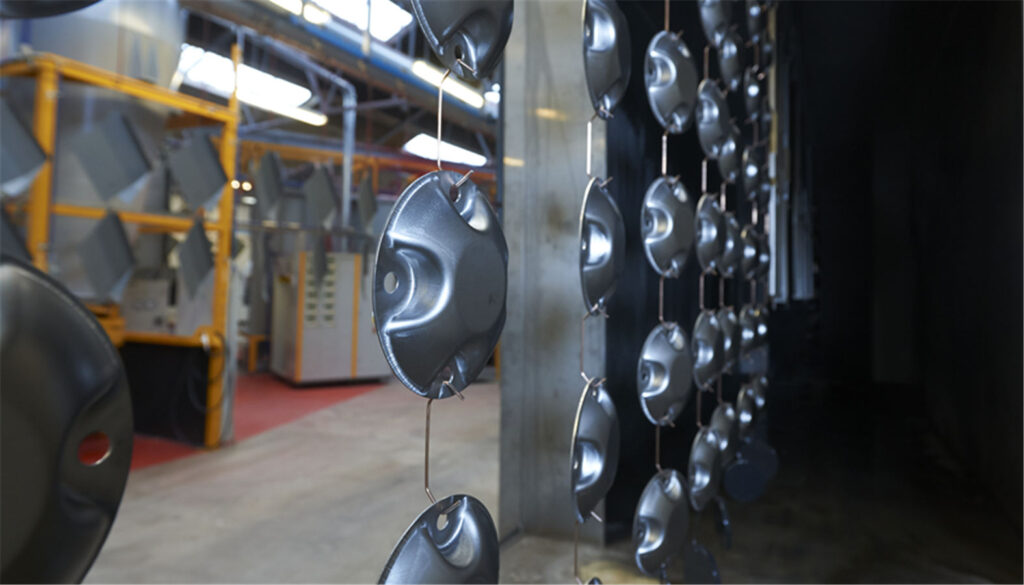
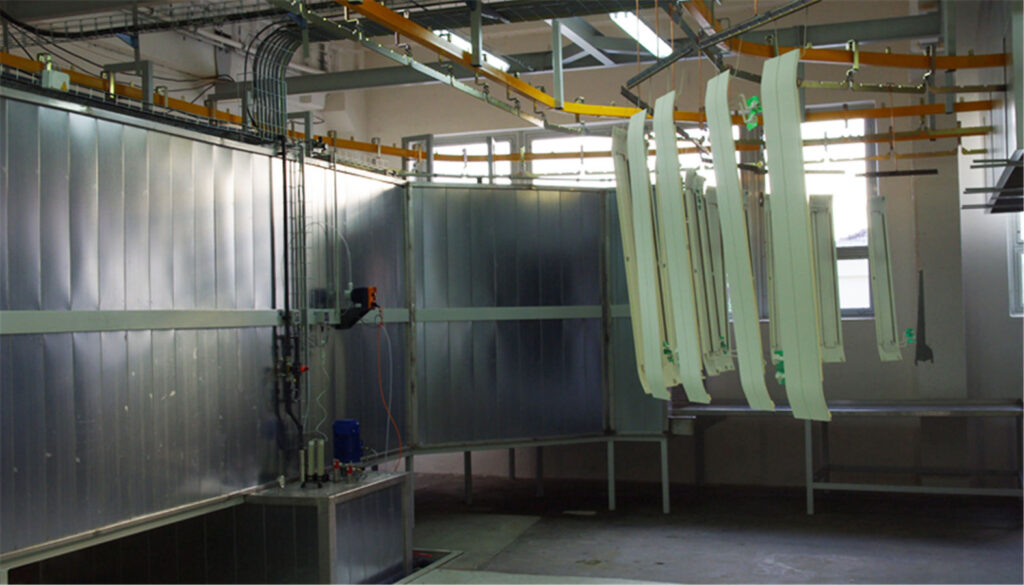
Optimization Strategies: Enhancing Pretreatment for Superior Adhesion
Consistent, high-performance adhesion in an e-coat line hinges on optimizing the pretreatment process. By focusing on four key strategic areas, manufacturers can systematically address common failure points and significantly boost coating adhesion and overall e-coat line reliability.
1. Precise Chemical & Parameter Control
Maintain peak cleaning and conversion coating effectiveness through strict monitoring and control of chemical concentrations, temperatures, and pH. Implement automated dosing systems for cleaners and conversion chemistries, ensure baths operate within specified temperature ranges using reliable controls, and continuously monitor/adjus pH to prevent scaling or reduced efficacy. Rigorous conductivity control in rinse tanks, particularly maintaining final DI rinse conductivity below 50 µS/cm, is critical to prevent ionic contamination and ensure surface purity before e-coat immersion. Establish disciplined bath dumping and replenishment schedules based on production volume.
2. Maximized Mechanical Action & Coverage
Enhance the physical removal of soils and ensure complete surface wetting by optimizing spray pressure, nozzle performance, and flooding. Use appropriate spray pressures for effective impingement, regularly inspect and clean nozzles to ensure full, uniform coverage patterns, and maintain correct fluid levels and flow rates for thorough part immersion or spray “flooding,” especially in complex geometries. Verify pump performance and manifold distribution to guarantee consistent force across all zones within the e-coat line’s pretreatment section.
3. Comprehensive Water & Conversion Coating Management
Prevent contamination carryover and ensure optimal conversion layer formation through robust water management and dedicated conversion bath care. Employ counter-current cascade rinsing and effective filtration on cleaner and key rinse tanks to minimize contaminant buildup. Diligently manage final DI rinse quality. For the conversion coating stage, go beyond basic parameters by closely monitoring specific metrics, implementing bath agitation/circulation, utilizing sludge removal systems, and performing regular coating weight/crystal structure checks as per supplier recommendations to guarantee a consistent, high-quality adhesive base.
4. Guaranteed Process Time & Effective Drying
Ensure sufficient reaction and drying times by aligning e-coat line speed with pretreatment requirements and optimizing drying efficiency. Calculate and validate minimum dwell times needed for each pretreatment stage based on chemistry, temperature, and part complexity; set the e-coat line speed to strictly meet or exceed these times across all pretreatment zones. Simultaneously, ensure the drying oven provides adequate temperature, dwell time, and optimized airflow patterns to completely eliminate residual moisture after the final rinse, preventing water entrapment and ensuring a perfectly dry surface before e-coat tank entry. Manage line stoppages effectively to avoid condensation.
Mastering these four integrated strategies transforms the pretreatment process into a reliable cornerstone for achieving durable, superior adhesion performance throughout the e coat line.