In the modern coating industry, pretreatment coating systems are crucial to the quality of the coating, which directly affect the adhesion, corrosion resistance and overall coating performance. Whether it is the traditional coating process or the more advanced e-coating line, precise control of the pre-treatment link is the basis for ensuring the quality of the final product. Any slight negligence may lead to coating defects, thereby increasing rework costs and even affecting the service life of the product. However, many companies often ignore the details of the pre-treatment system when maintaining it, resulting in a significant reduction in the coating effect.
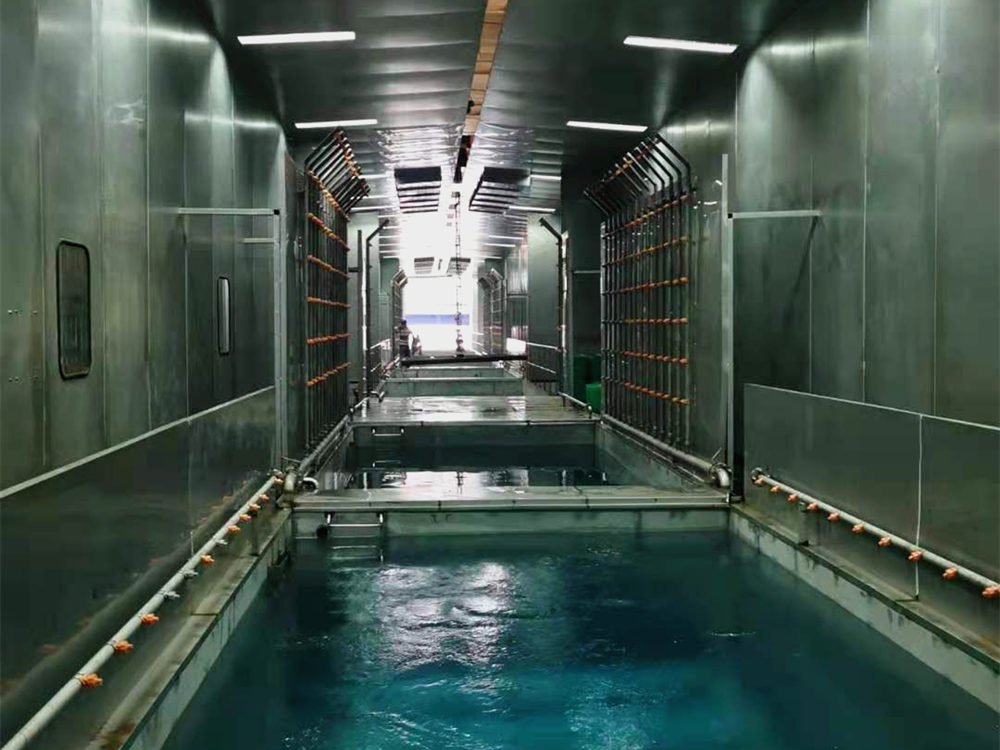
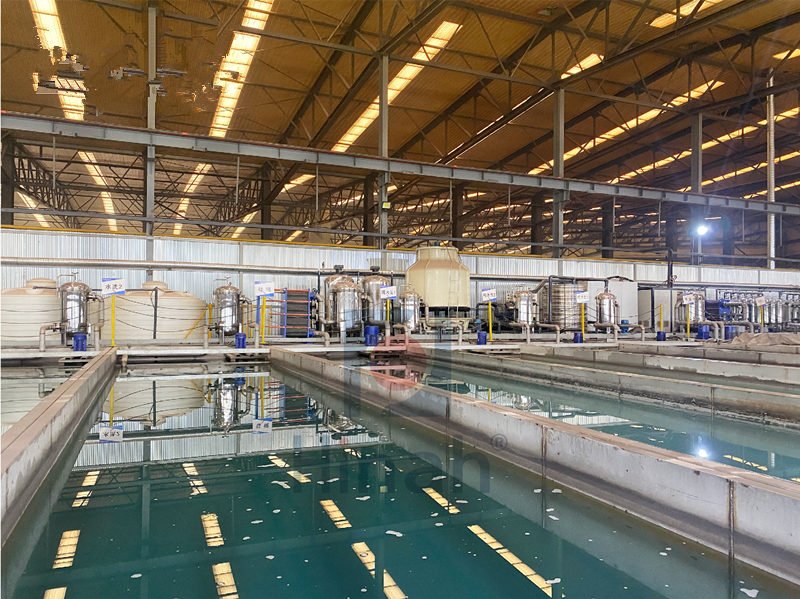
Mistake #1: Ignoring pH Balance in Pretreatment Coating Systems
In the pretreatment coating systems, the stability of pH value is crucial to the quality of the coating. However, many companies still rely on manual testing to monitor pH, which often leads to pH fluctuations. Due to manual operation errors and untimely adjustments, the pH value is prone to deviate from the ideal range, which in turn affects the treatment effect of the metal substrate. pH fluctuations will lead to accelerated oxidation of the metal substrate and uneven phosphating film, which will ultimately affect the adhesion and corrosion resistance of the coating. This unstable pre-treatment process will lead to a decline in coating quality, and even problems such as coating shedding and blistering, which will significantly increase the rework rate.
In order to avoid errors caused by manual testing, it is recommended to use automated pH monitoring technology. Through the real-time monitoring system, it can be ensured that the pH value is always kept within the optimal range to avoid fluctuations caused by human factors. Combining IoT sensors with real-time alarm systems, automated monitoring can be achieved to ensure that the pH value is adjusted in real time and alarms are issued in time.
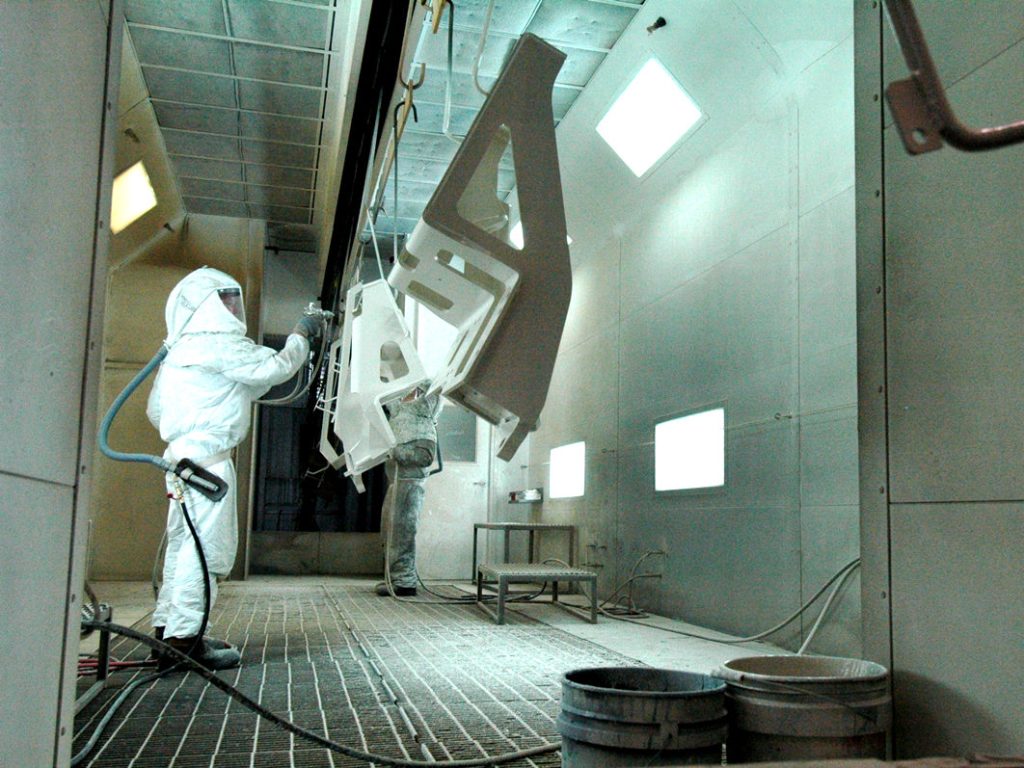
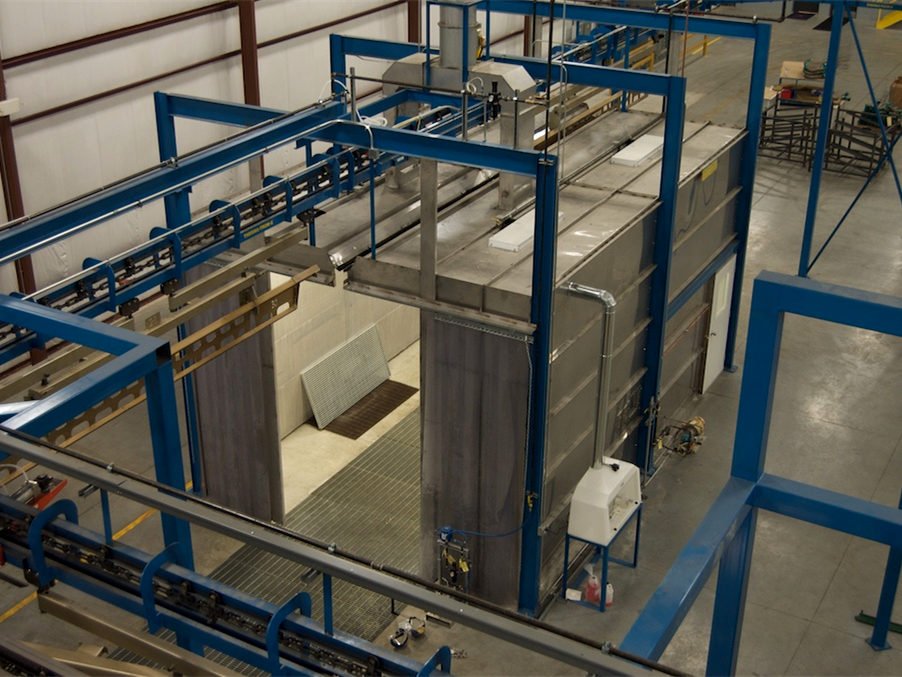
Mistake #2: Inadequate Rinsing Stages in Pretreatment Processes
During the pretreatment coating systems, the thoroughness of the rinsing stage is critical. However, many e-coating lines do not handle the rinsing process properly, resulting in incomplete removal of chemical residues. These residues will affect the adhesion of subsequent coatings and even cause blistering and uneven coatings. Through scanning electron microscopy, it is obvious that the negative impact of residual chemicals on coating quality, especially the changes in microstructure, leads to a significant decrease in coating adhesion.
Studies have shown that if rinsing is not thorough, coating adhesion may decrease by 30%. In addition, chemical residues will form bubbles during the coating process, affecting the appearance and durability of the coating, increasing rework and material waste.
In order to ensure thorough rinsing, it is recommended to optimize the design of the water washing tank and use more efficient rinsing technology. For example, countercurrent rinsing can more effectively remove residues than spray rinsing, thereby improving coating quality and consistency. Countercurrent rinsing uses the direction of water flow opposite to the direction of movement of the work object to ensure that every surface is fully cleaned.
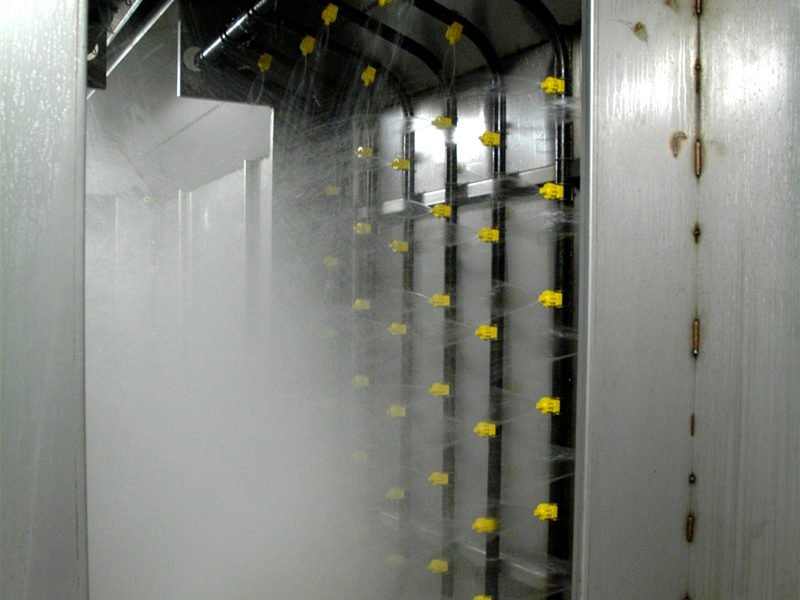
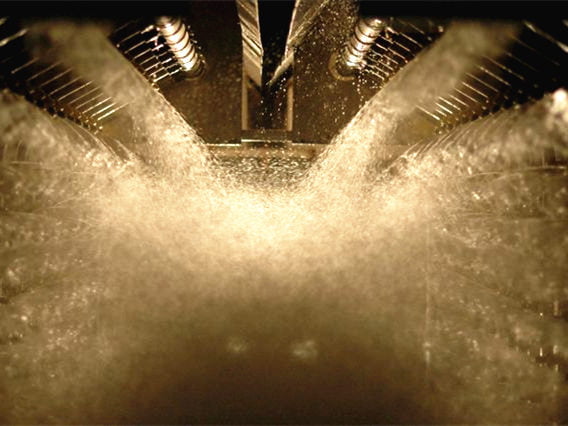
Mistake #3: Overlooking Filter Replacement in Pretreatment Coating Systems
In the pretreatment coating systems, the existence of filters is indispensable. It can remove particulate matter and impurities in the treatment fluid to ensure the smooth progress of the coating process. However, irregular replacement of filters will cause the filter element to be blocked. This will not only cause wear of the nozzle, but also cause pollution of the treatment fluid, further affecting the quality and stability of the coating.
The consequence of filter element blockage is often a shortened equipment life and increased energy consumption. Due to overload operation, the overall efficiency of the equipment will decrease, and the energy consumption will increase by 12% compared with the normal state. In addition, the wear of nozzles and other components will accelerate the aging of the equipment, further increasing the cost of maintenance and replacement.
In order to avoid the problems caused by untimely filter replacement, it is recommended to use an intelligent filter monitoring system. Through predictive maintenance technology, the system can monitor the status of the filter in real time and send a replacement signal in time according to the changes in pollutant load, thereby avoiding equipment damage and production interruption caused by filter element blockage.
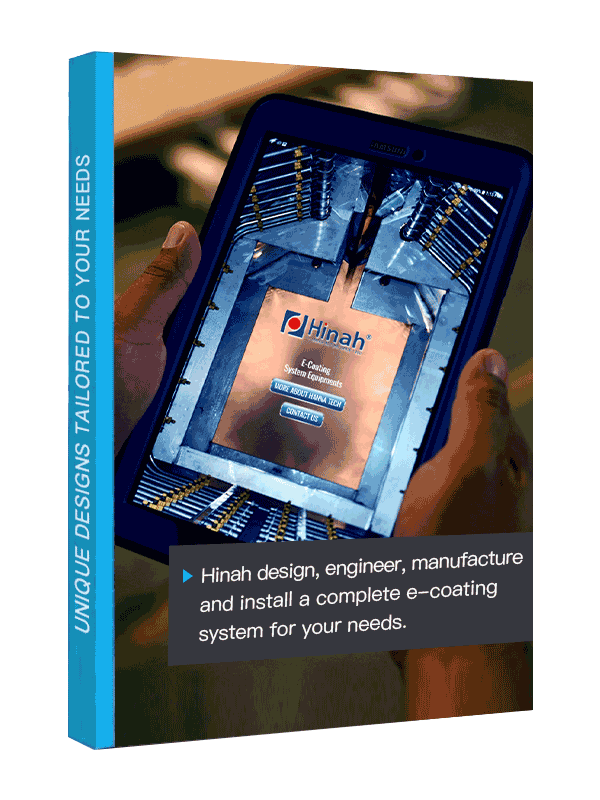
Let's Have A Chat
Get An E-coating Line Planning !
Match Your Products, Get The Solution & Price..
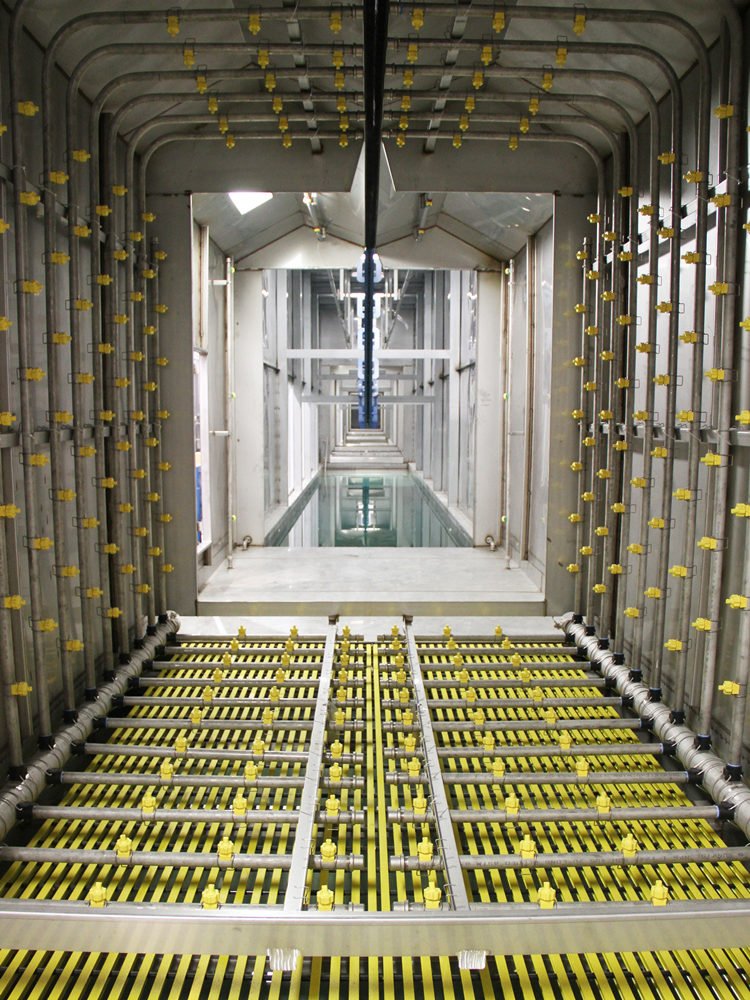
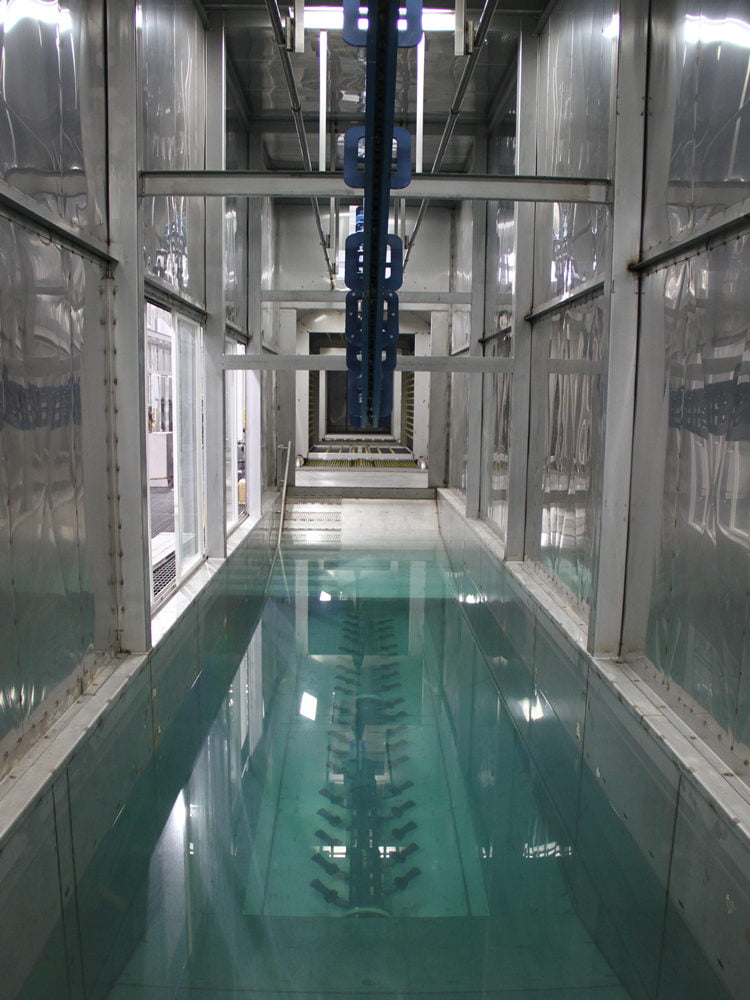
How to Build a Fail-Safe Maintenance Plan for Pretreatment Coating Systems
Establishing a reliable maintenance plan is key to ensuring long-term stable operation of the pretreatment coating systems. The following is a specific checklist and process:
- Daily inspection: Check pH, conductivity and temperature to ensure that they are within the ideal range. Check filters and nozzles for blockage or damage.
- Weekly inspection: Thoroughly inspect the water washing tank and backwashing system to ensure that all components are operating properly and to check for potential chemical residue issues. Check the overall operating status of the equipment to confirm that there is no abnormal noise or vibration.
- Monthly inspection: Conduct a comprehensive assessment of all systems, focusing on checking the status of filters to ensure timely replacement. Check all sensors and monitoring devices to ensure that they are accurate and effective.
These steps can help establish a reliable pretreatment coating system maintenance plan to maximize equipment life, reduce repair costs, and ensure the quality and consistency of the coating process.